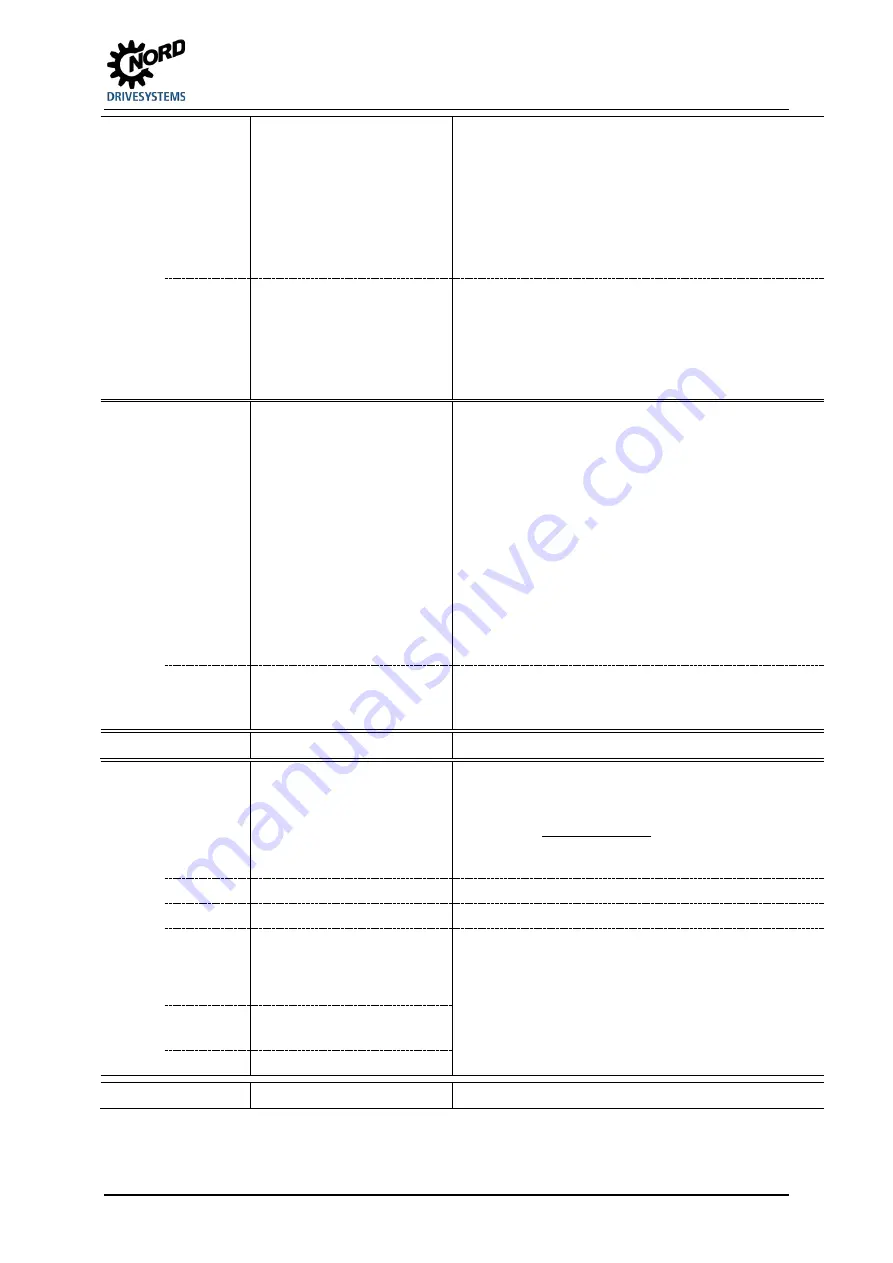
6 Operating status messages
BU 0180 en-4118
163
E004
4.0
Overcurrent module
Error signal from module (short duration)
• Short-circuit or earthing fault at FI output
• Motor cable is too long
• Use external output choke
• Brake resistor faulty or resistance too low
Do not shut off P537!
The occurrence of a fault can significantly shorten the
service life of the device, or even destroy it.
4.1
Overcurrent measurement
"Overcurrent measurement"
P537 (pulse current switch-off) was reached 3x within 50 ms
(only possible if P112 and P536 are disabled)
• FI is overloaded
• Drive sluggish, insufficiently sized
• Ramps (P102/P103) too steep -> Increase ramp time
• Check motor data (P201 … P209)
E005
5.0
Overvoltage UZW
Link circuit voltage too high
• Increase deceleration time (P103)
• If necessary, set switch-off mode (P108) with delay
(not with lifting equipment)
• Extend emergency stop time (P426)
• Fluctuating speed (e.g. due to high centrifugal
masses)
adjust U/f characteristic curve if
necessary (P211, P212)
Devices with brake chopper:
• Reduce energy return using a braking resistor
• Check the function of the connected braking resistor
(broken cable)
• Resistance value of connected braking resistor too
high
5.1
Mains overvoltage
Mains voltage is too high
• See technical data (
)
E006
---
Reserved
E008
8.0
Parameter loss
(maximum EEPROM value
exceeded)
Error in EEPROM data
• Software version of the stored data set not
compatible with the software version of the FI.
NOTE:
Faulty parameters are automatically reloaded
(default data).
• EMC interferences (see also E020)
8.1
Inverter type incorrect
• EEPROM faulty
8.2
Reserved
8.3
EEPROM KSE error
(Customer unit incorrectly
identified (customer’s interface
equipment))
The upgrade level of the frequency inverter was not
correctly identified.
• Switch mains voltage off and on again.
8.4
Internal EEPROM error
(Database version incorrect)
8.7
EEPR copy not the same
E009
---
Reserved
Summary of Contents for SK 180E Series
Page 1: ...BU 0180 en NORDAC BASE SK 180E SK 190E Users Manual for Frequency Inverters...
Page 4: ...NORDAC BASE SK 180E SK 190E Users Manual for Frequency Inverters 4 BU 0180 en 4118...
Page 185: ...8 Additional information BU 0180 en 4118 185 8 3 4 EU Declaration of Conformity...
Page 211: ...Key word index BU 0180 en 4118 211...
Page 212: ...6071802 4118...