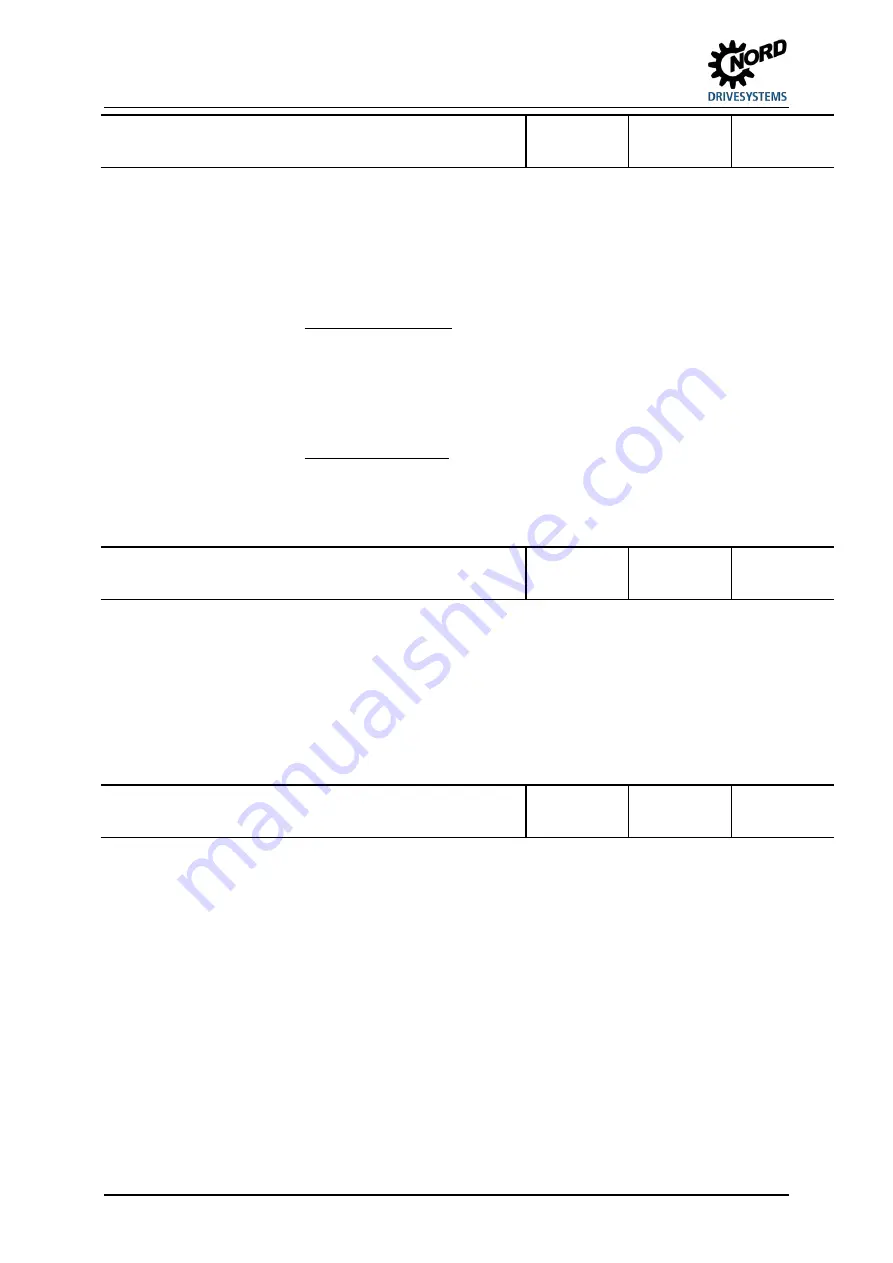
NORDAC BASE (SK 180E / SK 190E) – Users Manual for Frequency Inverters
134
BU 0180 en-4118
P503
Master function output
(Master function output)
S
0 ... 3
{ 0 }
For master-slave applications this parameter specifies on which bus system the master transmits
the control word and the master values (P502) for the slave. On the slave, parameters (P509),
(P510), (P546 ) define the source from which the slave obtains the control word and the master
values from the master and how these are to be processed by the slave.
Specification of communication mode on the system bus for ParameterBox and NORDCON.
0 = Off
No
control word and master value
output,
If
no individual BUS option (e.g.
SK xU4-IOE) is connected to the
system bus, only the device directly
connected to the ParameterBox or
NORDCON is visible.
2 = System bus active
No
control word and master value
output,
All
FIs connected to the system bus
are visible in the ParameterBox or
NORDCON, even if no bus option is
connected. Prerequisite: all FIs must be
set to this mode.
1 = CANopen (system bus)
Control word
and master values are
transferred to the system bus.
If
no individual bus option (e.g.
SK xU4-IOE) is connected to the
system bus, only the device directly
connected to the ParameterBox or
NORDCON is visible.
3 = C system bus active
Control word
and master values are
transferred to the system bus
All
FIs connected to the system bus
are visible in the ParameterBox or
NORDCON, even if no bus option is
connected. Prerequisite: all other FIs
must be set to mode { 2 } "System bus
active"
P504
Pulse frequency
(Pulse frequency)
S
3.0 ... 16.0 kHz
{ 6.0 }
The internal pulse frequency for controlling the power unit can be changed with this parameter.
A higher setting reduces motor noise, but leads to increased EMC emissions and reduction of the
possible motor nominal torque.
NOTE:
The best possible degree of interference suppression for the device is adhered to by
using the default value and taking the wiring directives into consideration.
NOTE:
Raising the pulse frequency leads to a reduction of the possible output current,
depending on the time (I
2
t curve). When the temperature warning limit (C001) is
reached, the pulse frequency is gradually lowered to the default value. If the inverter
temperature drops by a sufficient amount, the pulse frequency is increased to the
original value.
P505
Abs. minimum frequency
(Absolute minimum frequency)
S
P
0.0 ... 10.0 Hz
{ 2.0 }
Specifies the frequency value that cannot be undershot by the FI. If the setpoint is less than the
abs. minimum frequency, the FI switches off or switches to 0.0Hz.
At the absolute minimum frequency, braking control (P434) and the setpoint delay (P107) are
actuated. If a setting value of "Zero" is selected, the brake relay does not switch during reversing.
When controlling lift equipment without speed feedback, this value should be set to a minimum of
2Hz. From 2Hz, the current control of the FI operates and a connected motor can supply sufficient
torque.
NOTE:
Output frequencies of < 4.5 Hz lead to current limitation (please see chapter 8.4.3 "Reduced
overcurrent due to output frequency").
Summary of Contents for SK 180E Series
Page 1: ...BU 0180 en NORDAC BASE SK 180E SK 190E Users Manual for Frequency Inverters...
Page 4: ...NORDAC BASE SK 180E SK 190E Users Manual for Frequency Inverters 4 BU 0180 en 4118...
Page 185: ...8 Additional information BU 0180 en 4118 185 8 3 4 EU Declaration of Conformity...
Page 211: ...Key word index BU 0180 en 4118 211...
Page 212: ...6071802 4118...