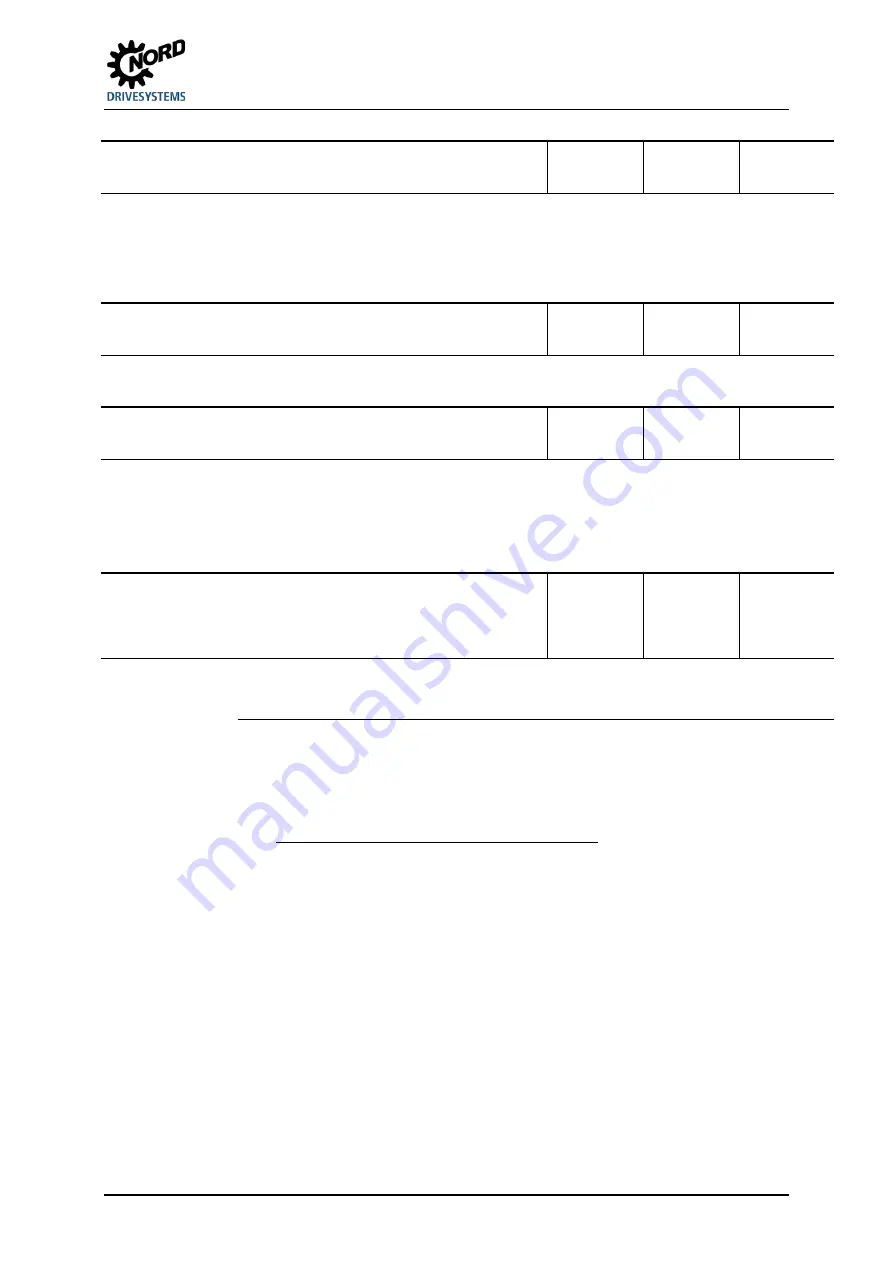
5 Parameter
BU 0180 en-4118
111
P318
Field weakening controller P
(Field weakening controller P)
S
P
0 ... 800 %
{ 150 }
The field weakening controller reduces the field setpoint when the synchronous speed is
exceeded. Generally, the field weakening controller has no function; for this reason, the field
weakening controller only needs to be set if speeds are set above the nominal motor speed.
Excessive values for P318 / P319 will lead to controller oscillations. The field is not weakened
sufficiently if the values are too small or during dynamic acceleration and/or delay times. The
downstream current controller can no longer read the current setpoint.
P319
Field weakening controller I
(Field weakening controller I)
S
P
0 ... 800 % / ms
{ 20 }
Only affects the field weakening range, see P318 >Field weakening controller P<
P320
Field weakening limit
(Field weakening limit)
S
P
0 ... 110 %
{ 100 }
The field weakening limit determines at which speed / current the controller will begin to weaken
the field. At a set value of 100% the controller will begin to weaken the field at approximately the
synchronous speed.
If values much larger than the standard values have been set in P314 and/or P317, then the field
weakening limit should be correspondingly reduced, so that the control range is actually available
to the current controller.
P330
Rotor starting position detection
(Rotor starting position detection)
S
(Former designation: "
PMSM Regulation
")
0 ... 1
{ 0 }
Selection of the method for determination of the starting position of the rotor (initial value of the
rotor position) of a PMSM (Permanent Magnet Synchronous Motor).
The parameter is only relevant for the control method "CFC closed-loop" (P300, setting "1").
0 = Voltage controlled
: With the first start of the machine, a voltage indicator is memorised
which ensures that the rotor of the machine is set to the rotor position "zero". This type of
starting position of the rotor can only be used if there is no counter-torque from the machine
(e.g. flywheel drive) at frequency "zero". If this condition is fulfilled, this method of
determining the position of the rotor is very precise (<1° electrical). In principle, this method
is not suitable for lifting equipment, as there is always a counter-torque.
For operation
without encoders, the following applies:
Up to the switch over frequency P331
the motor (with the nominal current memorised) is driven under voltage control. Once the
switch over frequency has been reached, the method of determining the rotor position is
switched over to the EMF method. If, taking hysteresis (P332) into account, the frequency
falls below the value in (P331), the frequency inverter switches back from the EMF method
to voltage controlled operation.
1 = Test signal method
: The starting position of the rotor is determined with a test signal. This
method also functions at a standstill with the brake applied, however it requires a PMSM
with sufficient anisotropy between the inductivity of the d and q axes. The higher this
anisotropy is, the greater the precision of the method. By means of parameter (P212) the
voltage level of the test signal can be adjusted and with parameter (P213) the position of the
motor position control can be adjusted. For motors which are suitable for use with the test
signal method, a rotor position accuracy of 5°…10° electrical can be achieved (depending
on the motor and the anisotropy).
Summary of Contents for SK 180E Series
Page 1: ...BU 0180 en NORDAC BASE SK 180E SK 190E Users Manual for Frequency Inverters...
Page 4: ...NORDAC BASE SK 180E SK 190E Users Manual for Frequency Inverters 4 BU 0180 en 4118...
Page 185: ...8 Additional information BU 0180 en 4118 185 8 3 4 EU Declaration of Conformity...
Page 211: ...Key word index BU 0180 en 4118 211...
Page 212: ...6071802 4118...