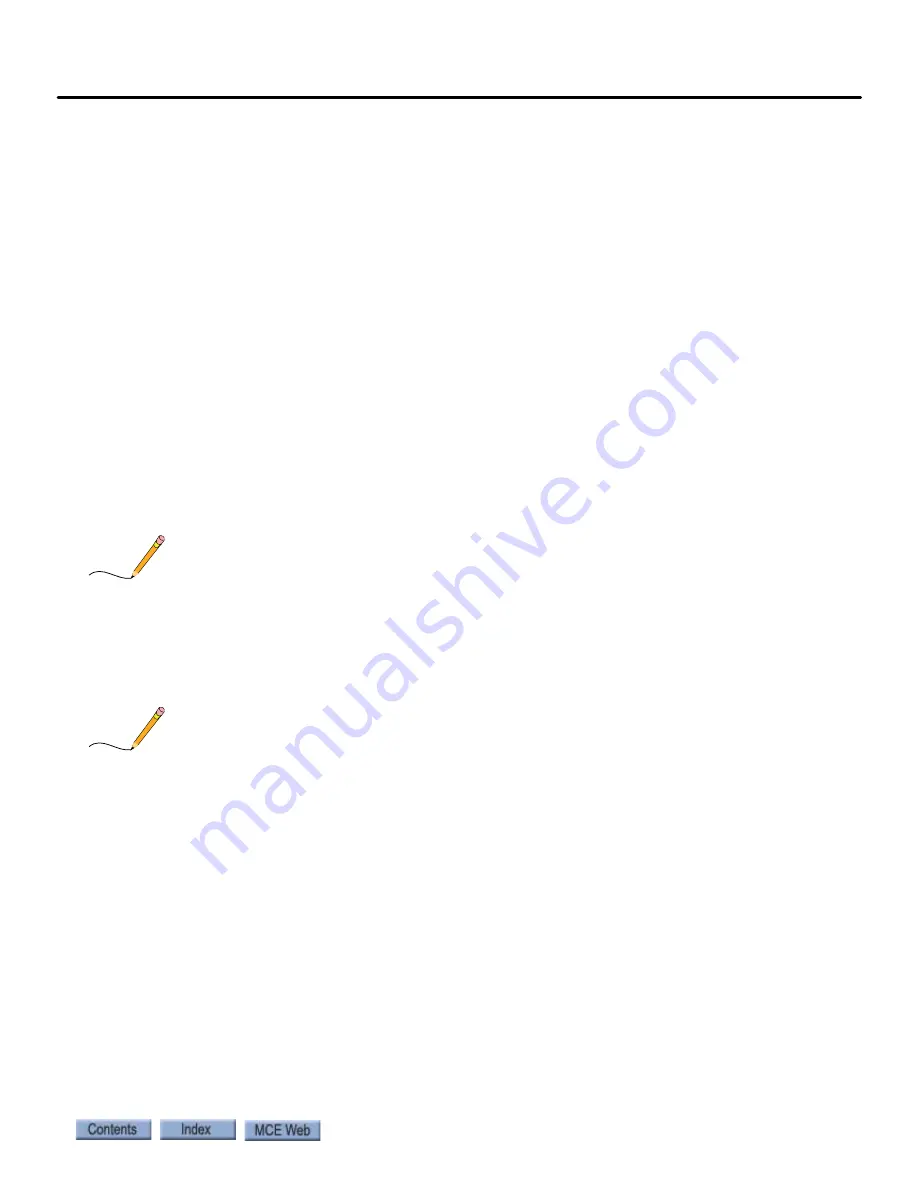
2-51
Running on Machine Room Inspection
iControl AC
2
Verify Electronic Motor Overload Protection (TORQMAX F5)
Provided the car is running normally on Inspection operation and is drawing normal current,
perform the following test to verify the drive electronic motor overload protection is correctly
set to protect the motor from overload conditions:
1. Verify LM08, Electronic Motor Protection, is set to ON (LF.08).
2. Note (write down) the value of LM09, Electronic Motor Protection Current (LF.09. This
value must be equal to LM03, Motor Current (LF.12).
3. Lower the value of LM09 to 20% of the noted setting (LM09 x 0.20).
4. Run the car on Inspection. After one minute the drive should trip an EOH2,
Error
Motor Protection
fault and shut down the car (E.0H2).
5. After five seconds, the fault will automatically clear and the car will be ready to run on
Inspection again.
6. Set the value of LM09 back to the noted setting (Motor FLA or LM03).
Additional Adjustments and Checks
1. On the Configuration > Pattern > Common tab, set
Pattern scaling
to 100%.
2. On the Configuration > Pattern > Modes tab, set
Inspection/High Speed
to the desired
value (maximum Inspection speed is 150 fpm). Set
Inspection/Low Speed
to 25 fpm.
Note
If the Terminal Switches (UNT5/DNT5) have been installed, and you wish to use the reduced inspection
speed option, you may enable it by checking
Reduced inspection speed
on the Configuration > Pattern >
Modes tab. If not, you may enable Reduced Inspection speed after the Terminal Switches are installed.
(Enabling it now, without switches, would cause the car to run at 25 fpm.)
3. Stop the car so that the car top can be accessed from the top hall door.
Note
NOTE: Car Top Inspection operation automatically overrides Car Panel Inspection operation.
4. Run the car from the Car Top Inspection station, checking the up and down buttons and
the stop switch.
5. While running the car, check clearances and door locks. When all doors are locked,
remove any jumpers from door lock terminals.
6. Verify directional limit switch and final limit switch operation and position according to
page MRW1 or MRW2 of the job prints. The distance between the two switches should
ideally be greater than the distance required to stop the car after the direction command
is removed with the car on Inspection operation.
7. Verify the brake has sufficient tension to hold the car under all conditions likely to be
encountered during the installation phase.
Summary of Contents for Nidec iControl
Page 1: ...MOTION CONTROL ENGINEERING User Guide iControl with AC Drive...
Page 15: ......
Page 23: ...1 8 Manual 42 02 2223 iControl Overview...
Page 75: ...2 52 Manual 42 02 2223 Construction Mode...
Page 89: ...3 14 Manual 42 02 2223 Inspection Mode...