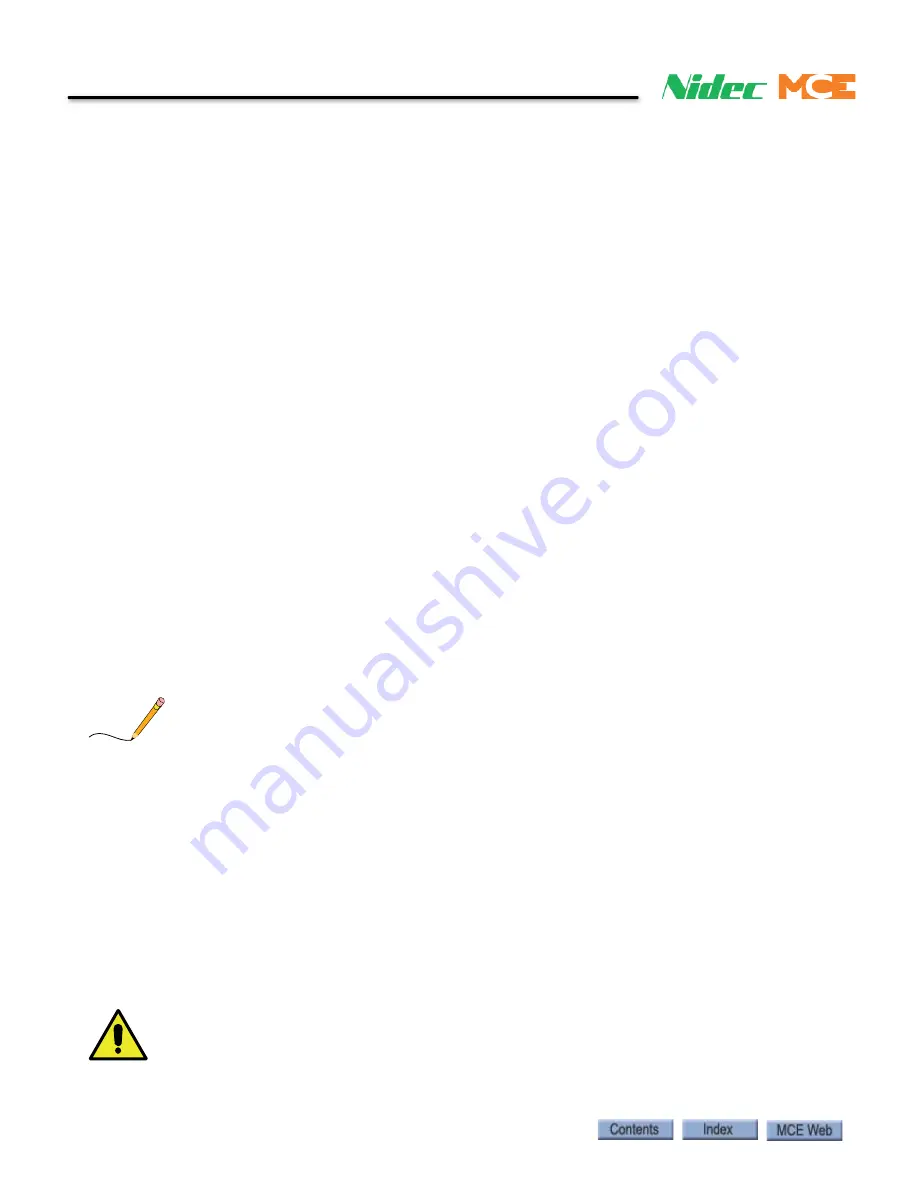
2-44 Manual # 42-02-2223
Construction Mode
Running on Machine Room Inspection
Once you are satisfied that the brake is picking properly, then do the following
1. Verify car movement (direction) and motor control and troubleshoot if not correct (
see
“Verifying Car Direction and Motor Control (TORQMAX F5)” on page 2-44
) or
see “Ver-
ifying Car Direction and Encoder Phasing (Magnetek)” on page 2-45
.
2. Verify pattern command vs. drive speed feedback tracking (
see “Verify Pattern Com-
mand and Drive Speed Feedback” on page 2-46
).
3. Calibrate the actual car speed (
see “Calibrating Actual Car Speed” on page 2-47
).
4. Set the following error margin (
see “Following Error Margin” on page 2-49
).
5. Set the following error and tach error tripping thresholds (
see “Following Error Margin”
on page 2-49
and
see “Tach Error Tripping Threshold Adjustment” on page 2-50
).
6. Verify electronic motor overload protection (
see “Verify Electronic Motor Overload Pro-
tection (TORQMAX F5)” on page 2-51
).
7. Perform additional adjustments and checks (
see “Additional Adjustments and Checks”
on page 2-51
).
Verifying Car Direction and Motor Control (TORQMAX F5)
1. If the brake picks but the car does not move, oscillates, or trips an EEnC1 fault (E.ENC1),
change the setting of the F5 drive LE03 parameter on the
Home > Prog > Encoder Data
Parameters menu
(LF.28). This parameter swaps encoder channels and/or reverses
motor rotation internally in the drive. Physically changing encoder or motor connec-
tions is not necessary and is not recommended. The LE03 options are:
0 = nothing reversed
1 = encoder channels A-B swapped
2 = motor rotation reversed
3 = motor rotation reversed and encoder channels A-B swapped
Note
For PM Synchronous Motors, if the A/B encoder channels are swapped, the encoder pole position value
in LE06 (LF.77) will have a different corresponding value and must be relearned. See
Encoder Learn
in
Section 5 -
Initial Start Up
of the TORQMAX Drive v3.xx manual.
1. If the car moves opposite of the intended direction while drawing normal current,
change parameter LN03 from 0 to 2 or 1 to 3. Motor current can be verified by display-
ing F5 drive parameter 7 on the
Home > Diag. #1 screen (
LF.93).
2. If the car moves in the intended direction while drawing excessive current, change
parameter LE03 from 0 to 1 or 2 to 3. Motor current can be verified by displaying F5
drive parameter 7 on the Home > Diag. #1 screen (LF.93).
3. Try to run the car on Inspection. If the drive still trips an EEnC1 fault, again change the
F5 drive parameter LN03 (LF.28). (Refer to LN03 parameter options in step 1). The car
should now move in the correct direction and draw normal current.
Caution
For PM motors, the direction of motion should not be changed by swapping motor phases (connec-
tions).
Summary of Contents for Nidec iControl
Page 1: ...MOTION CONTROL ENGINEERING User Guide iControl with AC Drive...
Page 15: ......
Page 23: ...1 8 Manual 42 02 2223 iControl Overview...
Page 75: ...2 52 Manual 42 02 2223 Construction Mode...
Page 89: ...3 14 Manual 42 02 2223 Inspection Mode...