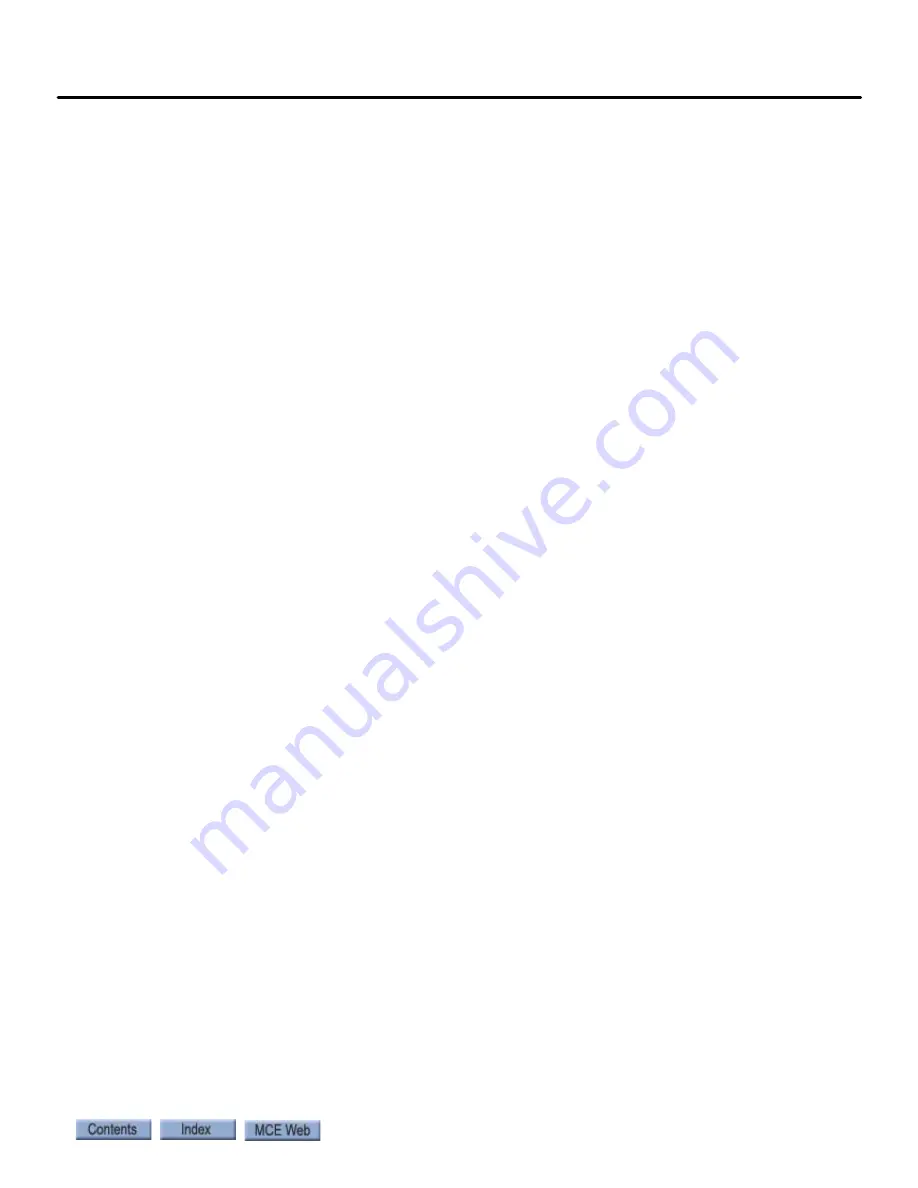
2-19
Setting Initial Operating Parameters
iControl AC
2
Learning the Safety Configuration
The controller is set to match the job safety configuration, according to the job survey, before
being shipped. By default, Construction Mode is enabled before the controller is shipped.
You
should not have to make changes to the Safety screen until you exit Construction
Mode.
The safety configuration for the job is stored in two locations (FLASH and EEPROM on the SAF
board). iControl constantly checks current safety information against stored data and also com-
pares the data in the two stored locations to make certain they continue to match. If you make a
change on the Safety screen, you will need to do a “learn” operation to write the new data to
iControl:
1. From the
View
menu select
Setup
and click
Safety
.
2. On the
Setup > Safety > Configuration tab
, make necessary changes.
3. Select
Acquire
from the
Write privilege
menu (if you have not yet acquired write privi-
leges to the iBox), then click
Send
to save the changes to iControl.
The controller will generate a safety mismatch fault because the settings you have just sent do
not match its stored information.
4. Verify that the iBox is in
Inspection
mode (Inspection switch set to INSP). Set the
Learn
switch to ON.
5. The
Learn
section of the
Setup > Safety > Configuration tab
should indicate that the
controller is ready to learn.
6. Click on the
Learn
button. The controller will take a few seconds to learn the new infor-
mation and will then confirm that the safety configurations again match.
7. Set the iBox Learn switch back to the OFF position.
The message window on the Safety> Configuration tab should report Safety Configura-
tions OK.
While iControl is in Construction Mode, specific safety and operational features are automati-
cally bypassed. These are:
• All cartop signals, including DP1 and DP2 (position encoder pulse streams).
• Normal and Emergency limit switches, NTS and ETS velocity and position logic. Except
Normal Limit Switches DNTD and UNTD.
• Only Machine Room and Cartop Inspection are allowed. Will not allow Hoistway Access or
COP Inspection.
• EQ signals, both seismic and counterweight derailment, are absent.
• Fire sensor signals are absent.
• No cartop comm.
Summary of Contents for Nidec iControl
Page 1: ...MOTION CONTROL ENGINEERING User Guide iControl with AC Drive...
Page 15: ......
Page 23: ...1 8 Manual 42 02 2223 iControl Overview...
Page 75: ...2 52 Manual 42 02 2223 Construction Mode...
Page 89: ...3 14 Manual 42 02 2223 Inspection Mode...