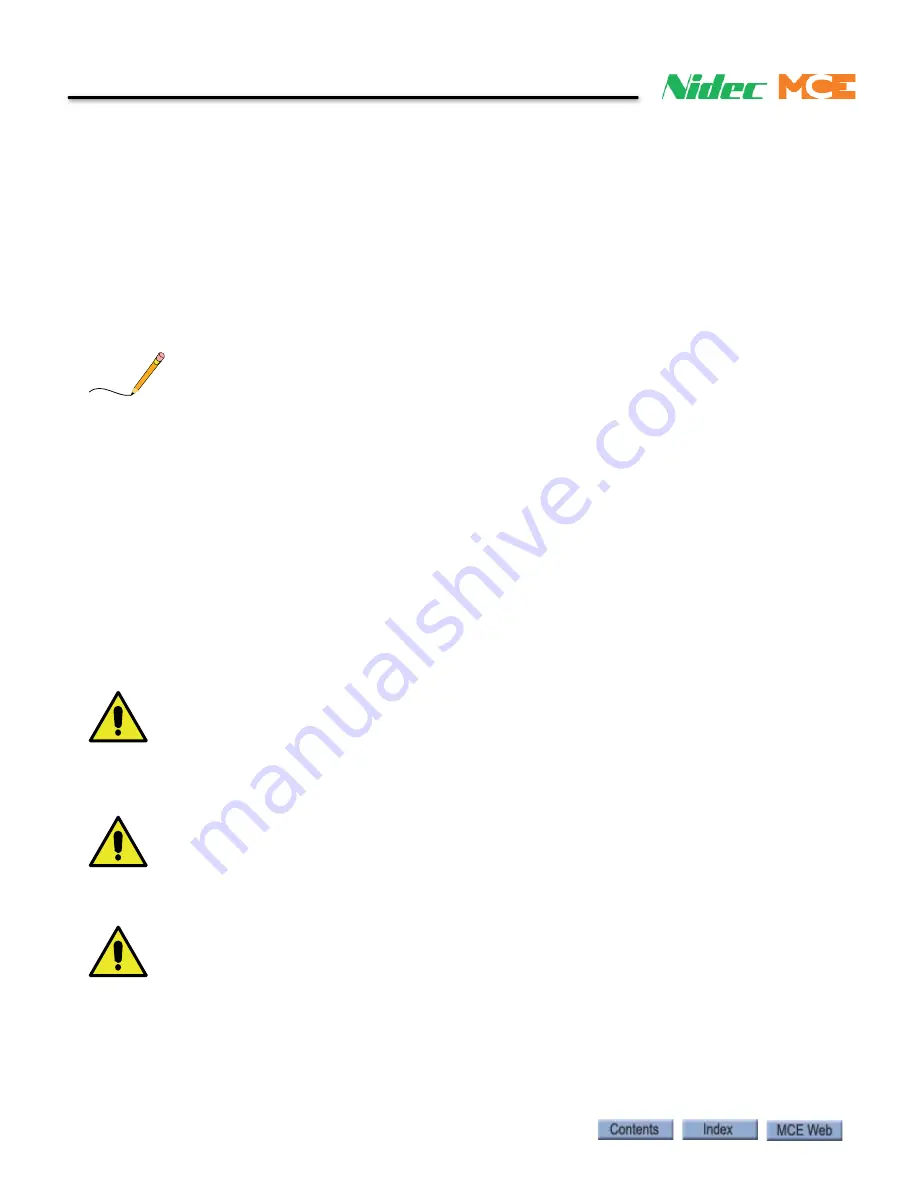
2-10 Manual # 42-02-2223
Construction Mode
Wiring the Brake
• Refer to job print drawing D3. Connect brake wires to terminals B1 and B2 located just
below the iPower box.
Brake wires must not be routed in the same conduit with AC motor wires or velocity encoder
wires.
Velocity Encoder Installation and Wiring
Do not place the encoder or its wiring close to a magnetic field (the motor or brake coils). Mag-
netic fields can induce AC into the encoder signal. This can cause the Drive to miscount, pro-
ducing erratic control at lower speeds.
Note
The encoder wiring must use a separate grounded conduit. Inside the controller cabinet, if control wires
must cross power wires, they must cross at right angles to reduce the possibility of interference. Some
cables, like the EnDat encoder cable, require a one inch or larger conduit due to the size of the connector.
Encoder Wiring
A shielded cable with an appropriate connector at the encoder end is provided.
Please refer to
“Encoder Cables” on page 2-11
. The controller end of the cable exposes trimmed and tinned
individual conductors. The encoder cable must be routed into the controller cabinet in a sepa-
rate conduit.
1. Connect the cable to the encoder using the cable/connector provided.
2. Route the cable through a separate conduit to the controller cabinet. Inside the control-
ler cabinet, if the encoder wires must cross power wires, they must cross at right angles
to reduce the possibility of interference.
3. Connect the controller end of the cable to the drive as shown in the job prints.
Caution
Do not coil excess encoder cable near high voltage components — noise may be induced. If the cable
must be shortened, trim it at the controller end. Do not cut and re-splice in the middle of the cable or
shorten at the encoder end (see also caution below).
Caution
The cable supplied with the Heidenhain ENC1313 EnDat encoder must not be altered, cut or short-
ened. Therefore, a 1.5 inch conduit is required to accommodate the cable connector.
Caution
Permanent magnet (PM) AC Gearless Machines must by synchronized with the AC Drive. Please
refer to
Motor Data > Permanent Magnet Motors
and
Encoder Data
in Section 5 -
Initial Start Up
of
the TORQMAX F5 Elevator Drive v3.xx manual.
Summary of Contents for Nidec iControl
Page 1: ...MOTION CONTROL ENGINEERING User Guide iControl with AC Drive...
Page 15: ......
Page 23: ...1 8 Manual 42 02 2223 iControl Overview...
Page 75: ...2 52 Manual 42 02 2223 Construction Mode...
Page 89: ...3 14 Manual 42 02 2223 Inspection Mode...