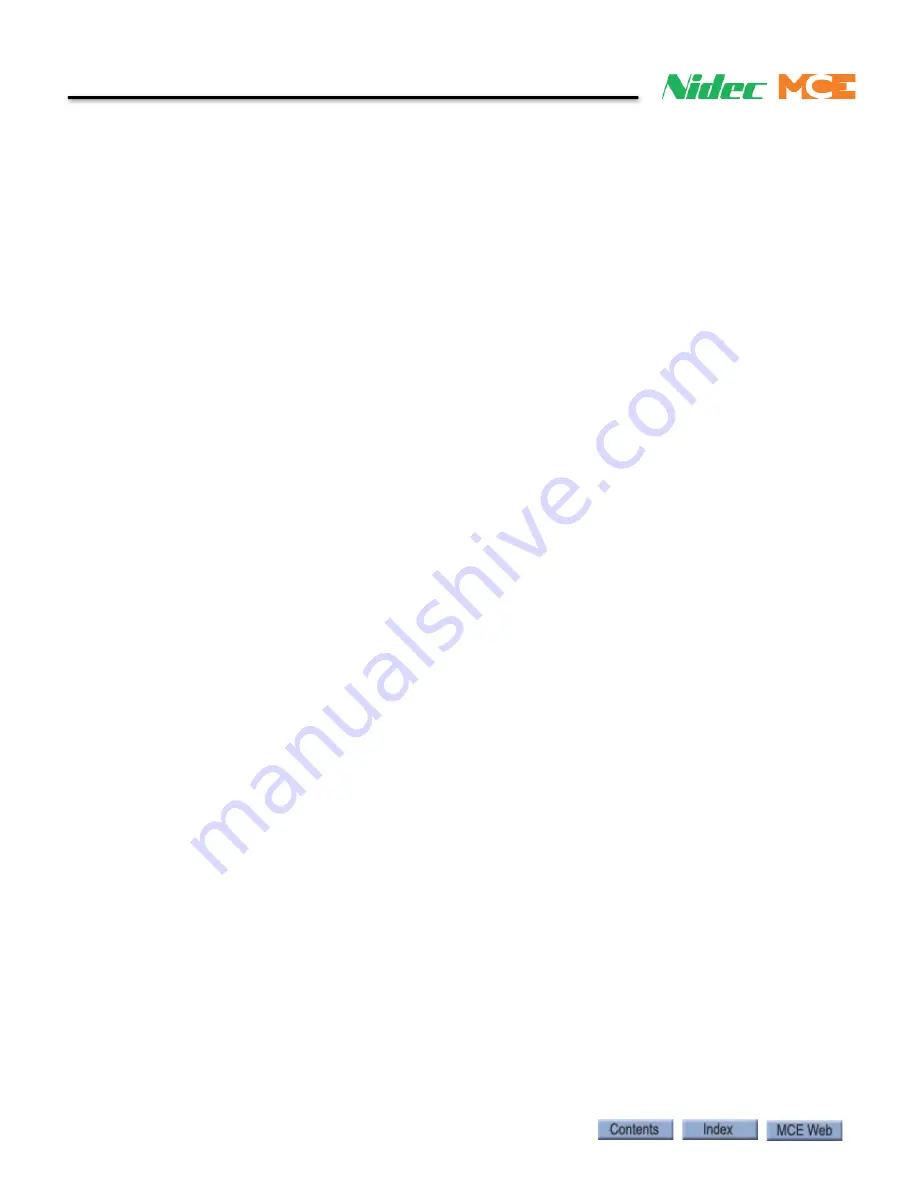
2-36 Manual # 42-02-2223
Construction Mode
Auto Tuning and Encoder Alignment
Drives used in iControl applications provide auto tuning procedures that allow the drive to
directly learn motor characteristics. Tuning improves performance and automatically calculates
some motor values you would otherwise have to enter manually.
Learning Encoder Data From PM Machines, TORQMAX F5
Please refer to
Motor Data > Permanent Magnet Motors
and
Encoder Data
in Section 5 -
Initial Start
Up
of the TORQMAX F5 Elevator Drive v3.xx manual
.
Encoder Alignment HPV 900 S2
This instruction is for permanent magnet (PM) motors only. Refer to the
PM Start-Up Proce-
dure
in the Magnetek drive manual.
Auto-tuning the PM motor HPV 900 S2
This instruction is for permanent magnet (PM) motors only. Refer to the
PM Start-Up Proce-
dure
and
Auto-Tune Procedure
in the Magnetek Drive Technical Manual.
Drive Response HPV 900 S2
1. For initial setup, set the Pick delay, Speed pick delay 1, and Speed pick delay 2 via the
iView Configuration > Brake > Timer tab to a sufficiently long value to allow enough
time for the drive to respond to a run request.
• If Pick delay is too short, a DRO fault will occur.
• Once the elevator is moving under control in the correct direction and at the com-
manded speed, these delays can be adjusted to a more optimum value.
• Set Pick delay to 1.0 second.
• Set Speed pick delay 1 to 1.75 seconds.
• Set Speed pick delay 2 to 0.75 seconds.
2. Depending on drive tuning, the amount of lag between commanded speed and drive
response can vary. As a result, as the drive is adjusted, the Lag delay parameter on Con-
figuration > Pattern > Common > General will need to change as well.
• If lag delay is insufficient, the elevator will plow into a landing. The acceleration and
jerk rate during deceleration to a landing will be greater than profile values indicate.
• If lag delay is excessive, the elevator will drag into a landing. Acceleration and jerk
rate during deceleration to a landing will be less than profile values indicate. In
addition, a discontinuity in the profile will occur during the transition from acceler-
ation to deceleration for movement between floors where a stabilized speed is not
reached. Under normal operation, this would occur when contract speed is not
reached.
• To adjust Lag delay, observe “Acceleration (Raw)” on the virtual oscilloscope via
Diagnostics > Virtual Oscilloscope. Perform one-floor-run movement and observe
the transition through zero (peak acceleration transitioning to peak deceleration as
the elevator reaches its peak speed that is less than contract speed). This transition
should have no vertical (too much Lag delay) or horizontal (too little Lag delay) dis-
continuity. This transition adjustment is only valid when the elevator is unable to
Summary of Contents for Nidec iControl
Page 1: ...MOTION CONTROL ENGINEERING User Guide iControl with AC Drive...
Page 15: ......
Page 23: ...1 8 Manual 42 02 2223 iControl Overview...
Page 75: ...2 52 Manual 42 02 2223 Construction Mode...
Page 89: ...3 14 Manual 42 02 2223 Inspection Mode...