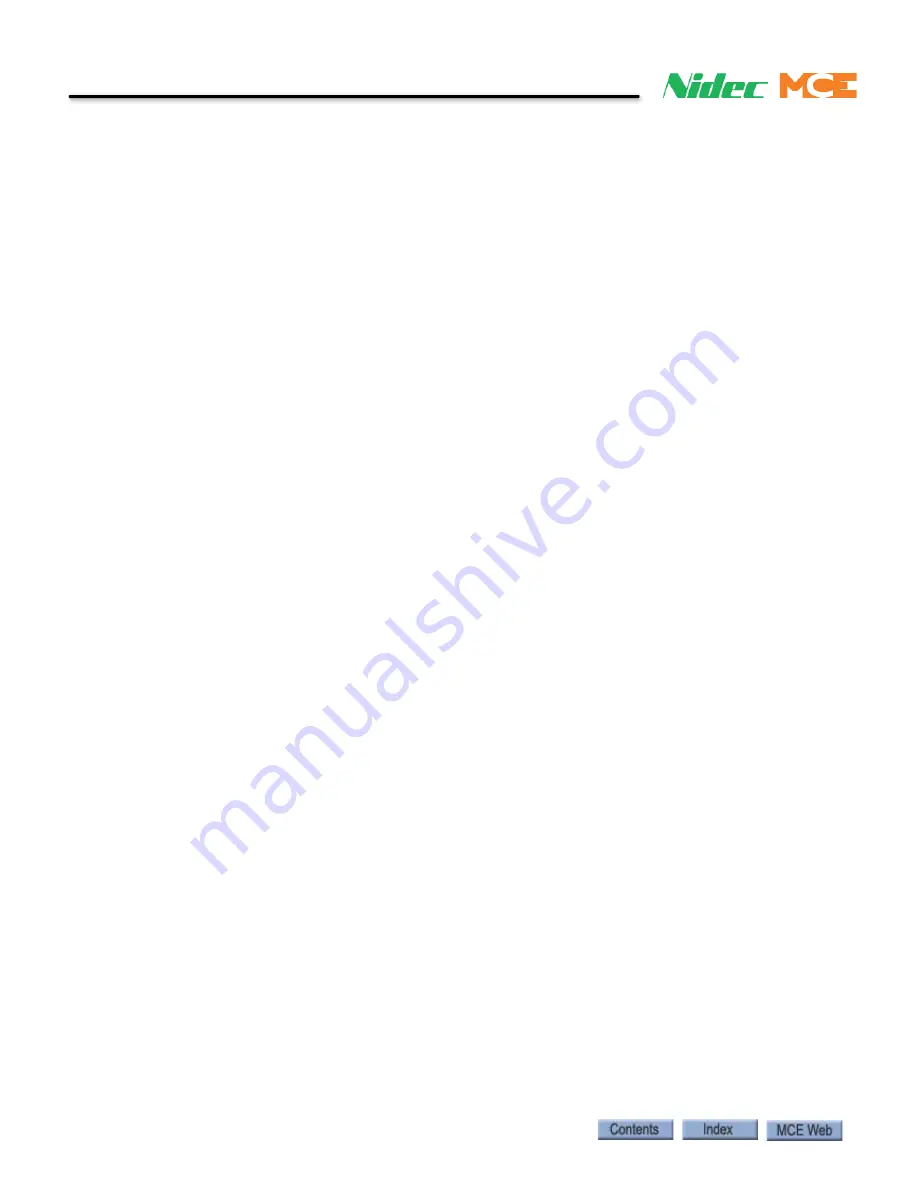
6-2 Manual # 42-02-2223
Troubleshooting
Troubleshooting Tools
The iBox provides status and trouble shooting information:
• The status line of the iBox display scrolls messages about system operation.
Please refer to
“LCD Display and Keypad” on page 7-2
.
• The iBox Event Log captures a FIFO file of the last 50 system events by event number and
name and provides additional data for each event captured. Press softkey (1) beneath the
Car label, scroll down to View Event Log and press Enter. To view event details, scroll to
the desired event and press Enter. Scroll down to see all of the data, including the event
name. A description and troubleshooting suggestions for each event can be found in iView
online Help (Help > iView Help > Messages Reference) and in the iControl Messages table
in this user guide.
Please refer to “iControl Messages” on page 6-14
.
iView provides an extensive toolset to help you diagnose problems:
• Hoistway: The Hoistway window (Controller > View > Hoistway) shows the current posi-
tion of the car, registered calls, car speed and current operating mode.
• Operational Status tab: The Operational Status tab shows the current speed, position, pat-
tern, and motion of the car. Also, Safety and Cartop processor status, safety circuits, level-
ing sensors and door locks. The Faults and Car status text boxes show general and car
operation faults and car status so that you can monitor them easily while viewing hoistway
information and running the car. A description and troubleshooting suggestions for each
fault or status message can be found in iView online Help (Help > iView Help > Messages
Reference) and in the iControl Messages table in this guide.
Please refer to “iControl Mes-
sages” on page 6-14
.
• Event Log: The Event Log tab (View > Diagnostics > Event Log) monitors and records sys-
tem events. You can easily save event log information to a file on your iView PC for archi-
val and future reference. A description and troubleshooting suggestions for each event can
be found in iView online Help (Help > iView Help > Messages Reference) and in the iCon-
trol Messages table in this guide.
Please refer to “iControl Messages” on page 6-14
.
• Fault Bypass: The Fault Bypass tab (View > Diagnostics > Fault Bypass) allows you to
bypass over 50 system faults. The Fault Bypass switch on the iBox must be ON and each
fault bypass times out after fifteen minutes to prevent the possibility of unintended, long
term bypassing of critical faults. To bypass faults, the car must be on Machine Room
Inspection or Test Operation.
• Diagnostic Flags: The Diagnostic Flags tab (View > Diagnostics > Diagnostic Flags) allows
you to view system diagnostic flags and car status in four classifications (Operation,
Motion, Safety, Drive).
• Terminal Switches Status: The Terminal Switches Status tab (View > Diagnostics > Termi-
nal Switches Status) shows information about the speed and position of the car when each
Normal and Emergency Terminal Switch opened.
• Diagnostic Outputs: Diagnostic Outputs (View > Diagnostics > Diagnostic Outputs win-
dow) allows you to choose and simultaneously monitor up to 16 system outputs.
• Virtual Oscilloscope: The oscilloscope (View > Diagnostics > Virtual Oscilloscope) allows
you to select and view two system outputs simultaneously on a “virtual oscilloscope”.
Summary of Contents for Nidec iControl
Page 1: ...MOTION CONTROL ENGINEERING User Guide iControl with AC Drive...
Page 15: ......
Page 23: ...1 8 Manual 42 02 2223 iControl Overview...
Page 75: ...2 52 Manual 42 02 2223 Construction Mode...
Page 89: ...3 14 Manual 42 02 2223 Inspection Mode...