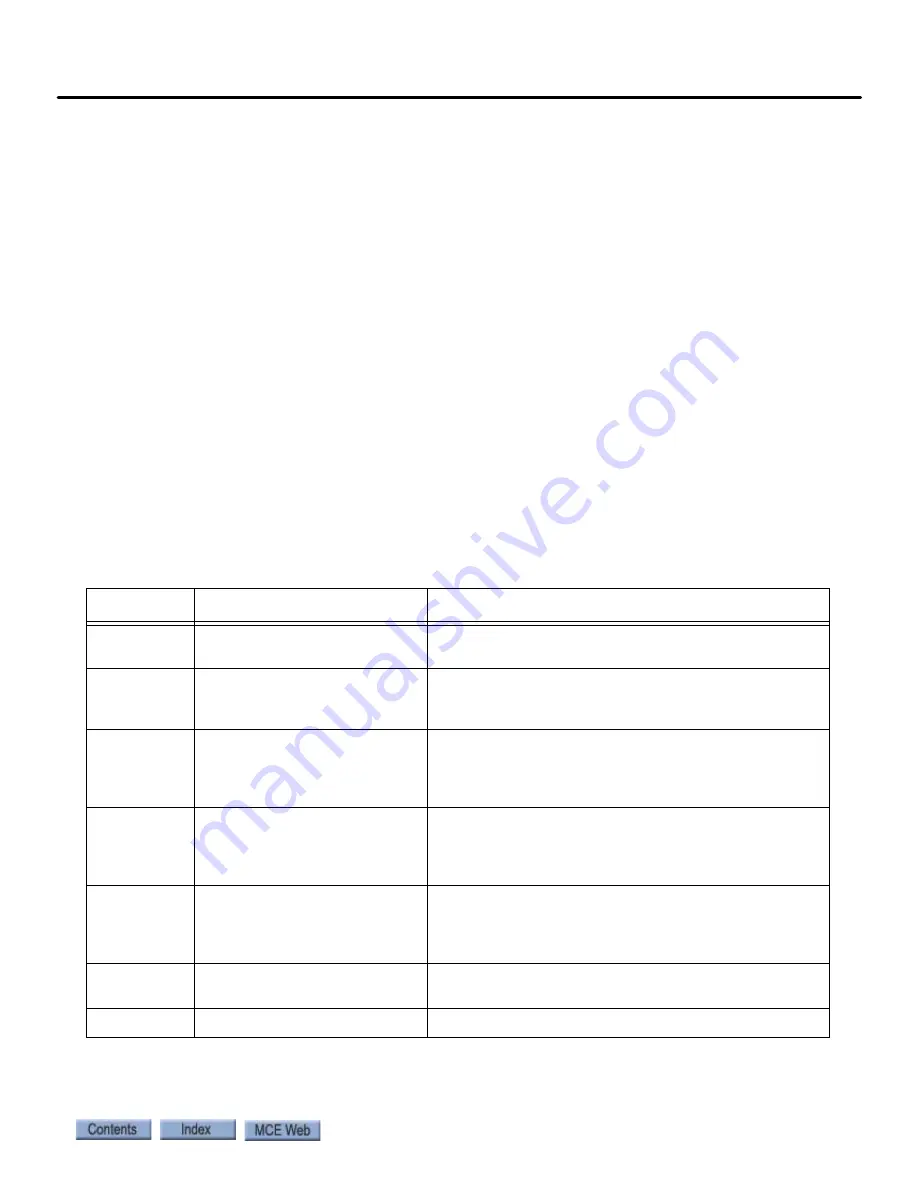
Motion Brake Module
5-89
5
Motion 4000
Discrete Control Adjustment
Check that there is no CAN connection to the brake module. This procedure is for discrete volt-
ages control.
1. Apply power to the controller. Place the elevator on Machine Room Inspection opera-
tion and pick a direction.
2. With the brake picked, adjust R67 to attain the brake manufacturer pick voltage. Verify
that the brake picks cleanly.
3. After the brake settles to hold position, adjust R68 to attain manufacturer hold voltage.
Verify that the brake is not dragging.
4. Disconnect power from the controller.
5. Disconnect the Relevel output from the module (place a wire nut on the wire end for
safety). Move the Hold wire to the Relevel output.
6. Reconnect power to the controller.
7. On Inspection, pick direction and allow the brake to pick. The brake hold position is
being controlled through the relevel output.
8. Adjust relevel R69 until the brake is just dragging but remains quiet.
9. Disconnect power from the controller. Return connections to their proper states.
CAN Control Adjustment
1. Apply power to the controller. Place the elevator on Machine Room Inspection.
2. Verify and/or set F7 brake parameters:
F7 #
Parameter
Description
133
Normal Brake Pick Delay
Time in milliseconds after drive enable command issued
and acknowledged before the brake should pick.
134
Speed Pick Delay
Time in milliseconds after brake is picked before the
speed command is issued. Used to prevent beginning
movement under a slow-picking brake. Default 500.
135
Normal Brake Hold Delay
After take off, the brake is held fully picked until this
timer expires, at which point, it settles to hold position/
voltage. Geared machine default 2000. Gearless
machine default 800.
136
Normal Brake Drop Delay
Delay in milliseconds that the brake should be delayed
from dropping after the speed command is dropped.
Goal is to avoid dropping the brake until the motor has
just stopped moving. Default 250.
138
Drive Disable Delay
Time in milliseconds after stopping at a floor which the
drive should maintain electrical control of the motor.
May be used to compensate for a slow dropping brake.
Default 1250.
139
Speed Hysteresis Delay
Provides a delay between when the speed command is
issued and when it begins to accelerate the load.
185
Brake Type
Module 1, Module 2, or Discrete. Select as configured.
Summary of Contents for Motion 4000
Page 20: ...xiv Manual 42 02 2P24 5 20 13 ...
Page 38: ...Motion 4000 Traction Elevator Control 1 18 Manual 42 02 2P24 ...
Page 178: ...Final Adjustments 3 56 Manual 42 02 2P24 ...
Page 322: ...User Interface 4 144 Manual 42 02 2P24 ...
Page 391: ...PC Board Quick References 5 69 5 Motion 4000 Figure 5 11 Example MC CPI Wiring ...
Page 439: ...Customer Notations A 27 A Motion 4000 Customer Notations Table A 4 Customer Notation Area ...
Page 444: ...Appendix A 32 Manual 42 02 2P24 ...