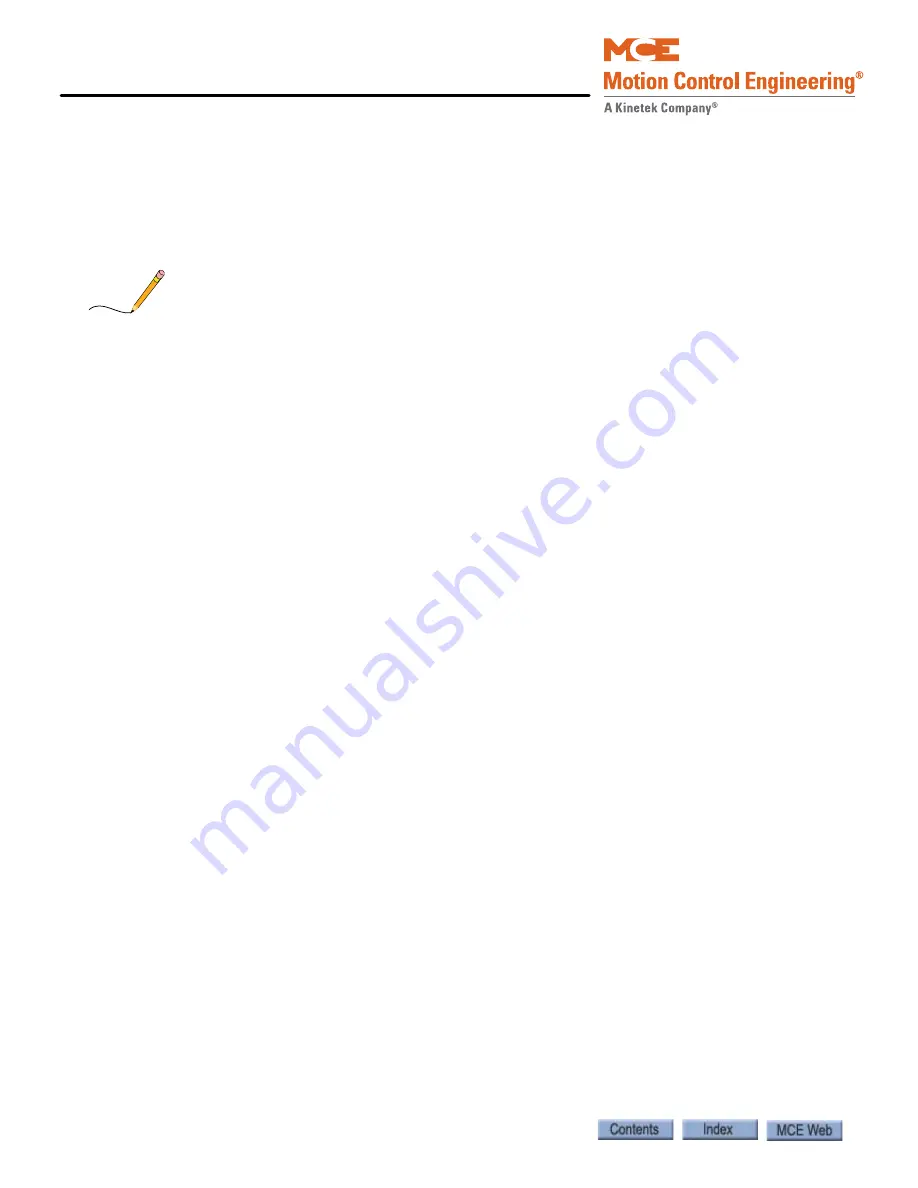
Final Adjustments
3-36 Manual # 42-02-2P24
How to Reset Excessive Faults
Many of the faults generated while performing acceptance tests are self-resetting once the fault
condition is corrected. However, this controller has excessive faults logic which will generate an
EXCESSIVE FAULTS SHUTDOWN if more than the established limit of faults occur within the
circumscribed period of time. To reset this fault:
• Press the Fault Reset button on the HC-CTL board.
Note
You can review speed and position information through an F5-accessed menu for assistance in
seeing what is actually happening in the hoistway.
Please refer to “MPI Diagnostic Menu” on
Safety String Test
This test verifies the Safety String is working correctly.
SAFH Safety String Test
1. Remove the wire from PMT terminal 15 or activate any safety device in the string.
2. A safety message will scroll on the MPU display.
3. Verify that the Safety Relay has dropped out and that the car cannot be run.
4. Reinstall the wires.
SAFC Safety String Test
1. On the CTL board, remove all wires from the SAFC input or activate any safety device in
the string.
2. The message CAR SAFETY DEVICE OPEN should scroll on the MPU board display.
3. Verify that the Safety Relay has dropped out and that the car cannot be run.
4. Reinstall the wires.
Motor Contactor Proofing Test
This test simulates a stuck motor contactor. The test should be performed with the car stopped
and with the car in motion. Once the fault is generated, the car should not be allowed to move
until the contactor is unstuck.
Car Stopped at Floor
This test is performed with the car stopped at a floor.
1. Use a non-metallic object to activate the PM contactor.
2. Observe that the car will not run. MPU displays “PMP input failed to activate”.
Car in Motion
The car is in motion when this test is performed.
1. Place a call.
2. Once the car is in motion, use a non-metallic object to activate and hold the PM contac-
tor “on”.
3. After the car stops at the designated floor, verify that it will not continue to run.
Summary of Contents for Motion 4000
Page 20: ...xiv Manual 42 02 2P24 5 20 13 ...
Page 38: ...Motion 4000 Traction Elevator Control 1 18 Manual 42 02 2P24 ...
Page 178: ...Final Adjustments 3 56 Manual 42 02 2P24 ...
Page 322: ...User Interface 4 144 Manual 42 02 2P24 ...
Page 391: ...PC Board Quick References 5 69 5 Motion 4000 Figure 5 11 Example MC CPI Wiring ...
Page 439: ...Customer Notations A 27 A Motion 4000 Customer Notations Table A 4 Customer Notation Area ...
Page 444: ...Appendix A 32 Manual 42 02 2P24 ...