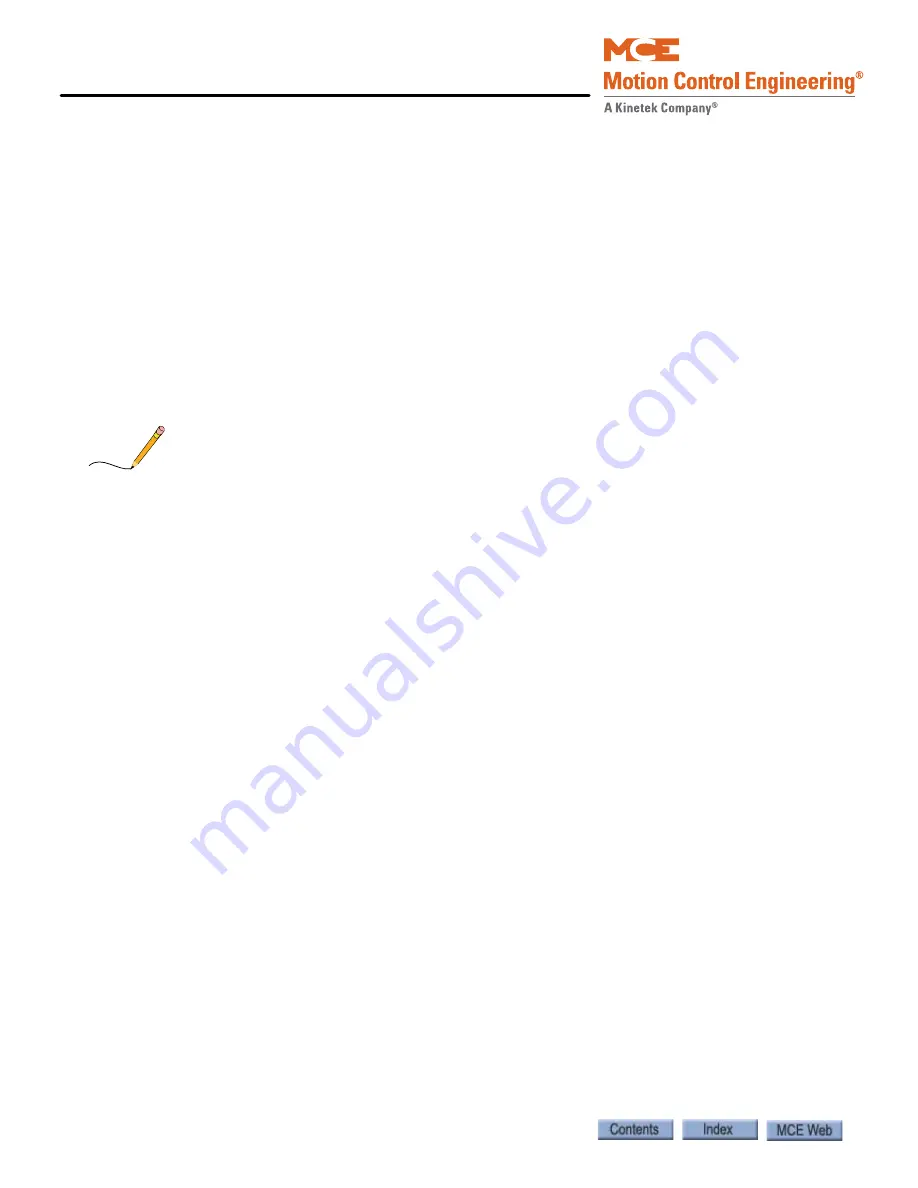
Installation
2-10 Manual # 42-02-2P24
AC Power Connections
• All conductors entering or leaving the controller must be through conduit.
• High voltage, high current conductors must be separated from control wires.
• Velocity encoder or tachometer wires must be routed in a separate conduit from high volt-
age, high current wires.
• Incoming power to the controller and outgoing power to the motor must be through sepa-
rate, grounded conduits.
Brake Module
If your job uses a brake control module, your job drawings may show aux-
iliary power connections specific to the brake from an isolation transformer. Follow the draw-
ings carefully.
1. Check the AC input specifications on your job prints. Verify that the AC supply is as
specified.
Note
Proper motor branch circuit protection in the form of a fused disconnect switch or circuit
breaker must be provided for each elevator according to applicable electrical code. Refer to the
drive manufacturer manual for proper drive circuit fuse sizing. Each disconnect or breaker
must be clearly labeled with the elevator number. The electrical contractor must determine the
wire size for the main AC power supply and for the wiring from the disconnect or breaker to the
controller or isolation transformer.
2. Connect AC supply wiring as shown in the job prints.
Power Check
After connecting power, it is a good practice to temporarily power up the control to check func-
tionality before connecting any field wiring.
1. Verify that the Inspection switch on the Control Board is in the Inspection position.
2. Visually check for loose connections or components.
3. Verify that fuses FB1 and FB2 are disengaged to prevent the brake from lifting.
4. Have a helper power up the controller and remain by the disconnect ready to shut down
immediately if needed.
5. Check that the Power On LED on the CHP (CAN Hub) board is on.
• Verify all transformer and power supply voltage levels are correct per the job prints.
• Verify all fuses are intact.
• Check phase-to-phase input voltage. If necessary, shut off main power and swap two of
the incoming feeds at the controller main terminal.
6. After verification, shut down the controller and engage fuses FB1 and FB2 before con-
tinuing with field connections.
Summary of Contents for Motion 4000
Page 20: ...xiv Manual 42 02 2P24 5 20 13 ...
Page 38: ...Motion 4000 Traction Elevator Control 1 18 Manual 42 02 2P24 ...
Page 178: ...Final Adjustments 3 56 Manual 42 02 2P24 ...
Page 322: ...User Interface 4 144 Manual 42 02 2P24 ...
Page 391: ...PC Board Quick References 5 69 5 Motion 4000 Figure 5 11 Example MC CPI Wiring ...
Page 439: ...Customer Notations A 27 A Motion 4000 Customer Notations Table A 4 Customer Notation Area ...
Page 444: ...Appendix A 32 Manual 42 02 2P24 ...