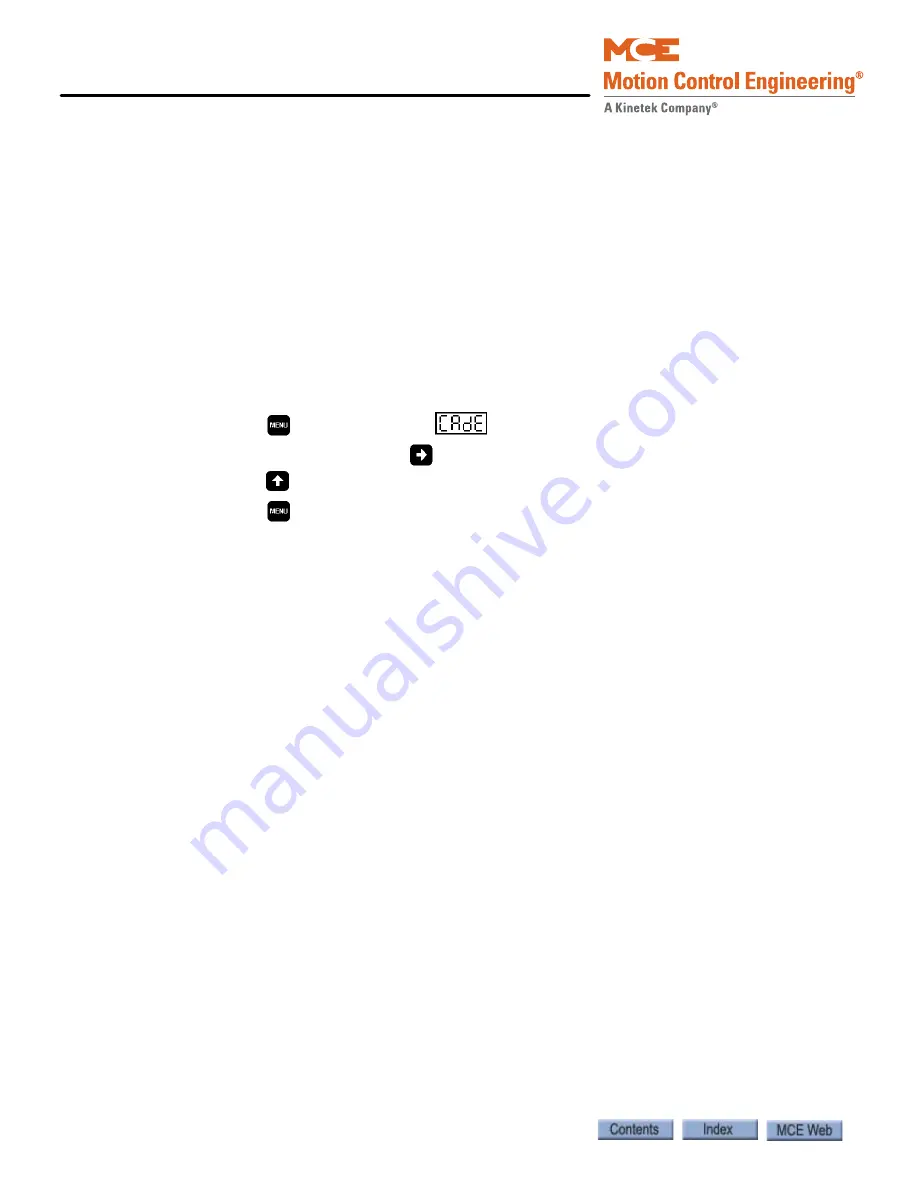
Final Adjustments
3-32 Manual # 42-02-2P24
Auto-zero Calibration
The EMCO load weigher has an auto-zero calibration option which can be used if needed. Typi-
cally this option is recommended for 2 to 1 roping or where guide shoes, rather than guide roll-
ers, are used.
How auto-zero calibration works:
• The control unit must see no power on the Hold terminals. (Some installations use these
terminals to indicate when the doors are closed but these terminals are not used with MCE
controls.)
• The CAde parameter must be set to 50.
• When the control unit senses no change in weight for two minutes, it automatically per-
forms the CEro zero load calibration (learns the empty car weight).
To enable auto-zero calibration:
1. Press the
menu button until
is displayed.
2. Enter the value 50. Press the
button to select a digit (blinks when selected) and
press the
button to set the value.
3. Press the
menu button twice to save the value.
Analog Weigher Additional Calibration
1. Connect the multimeter across UIO IO16 and Common. Verify that the reading is the
same as the measurement at terminals 0-10v and Com on the EMCO control unit.
2. To verify the linearity of the load weigher, place weights in the car that represent the fol-
lowing and observe the voltage values:
• Empty car - about 0.0 volts
• 25% of overload weight - about 2.5 volts
• 50% of overload weight - about 5.0 volts
• 75% of overload - about 7.5 volts
• Full load weight - about 8 volts
• Overload weight - about 10 volts.
Verifying Empty Car Weight for Analog Weighers
We recommend verifying zero calibration:
• If the ropes are new calibration may change slightly as the ropes stretch. After the first 30
days of operation, check the empty car weight, with the car in the middle of the hoistway,
using the display on the EMCO Load Weigher. If the empty car weight has changed (no
longer zero), the empty car weight must be re-learned.
• If the car experiences violent motion (emergency stop, buffer contact, etc.), verify zero cal-
ibration as described above.
Summary of Contents for Motion 4000
Page 20: ...xiv Manual 42 02 2P24 5 20 13 ...
Page 38: ...Motion 4000 Traction Elevator Control 1 18 Manual 42 02 2P24 ...
Page 178: ...Final Adjustments 3 56 Manual 42 02 2P24 ...
Page 322: ...User Interface 4 144 Manual 42 02 2P24 ...
Page 391: ...PC Board Quick References 5 69 5 Motion 4000 Figure 5 11 Example MC CPI Wiring ...
Page 439: ...Customer Notations A 27 A Motion 4000 Customer Notations Table A 4 Customer Notation Area ...
Page 444: ...Appendix A 32 Manual 42 02 2P24 ...