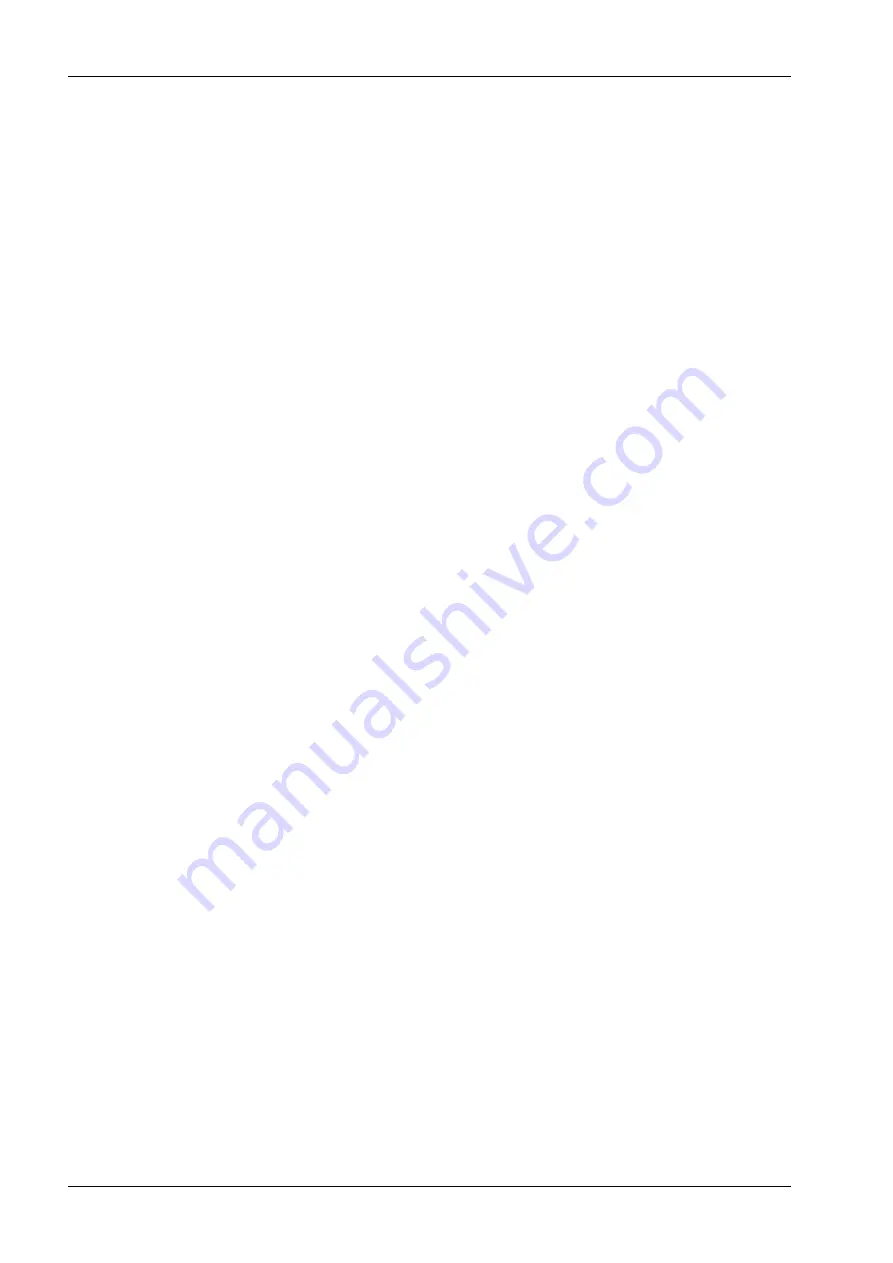
9.14 Operation of hold (OPERATION OF HOLD)...........................................................................................................82
9.15 Print command (PRINT COMMAND)......................................................................................................................82
9.16 Accumulation ............................................................................................................................................................83
9.17 Graph trigger mode (GRAPHIC TRIGGER SETTING)............................................................................................83
9.18 Graph trigger level setting (GRAPH TRIGGER LEVEL) ........................................................................................84
9.19 Hold of comparative result (COMPARATIVE RESULT HOLD) ............................................................................84
9.20 Hold of 2-pin method serial interface (S-I/F HOLD) ...........................................................................................84
9.21 Hold of weight display value (LOAD DISPLAY VALUE HOLD) ...........................................................................85
Weight Controller CSD-918
Table of contents
EN-4
Minebea Intec
Summary of Contents for CSD-918 Series
Page 239: ......