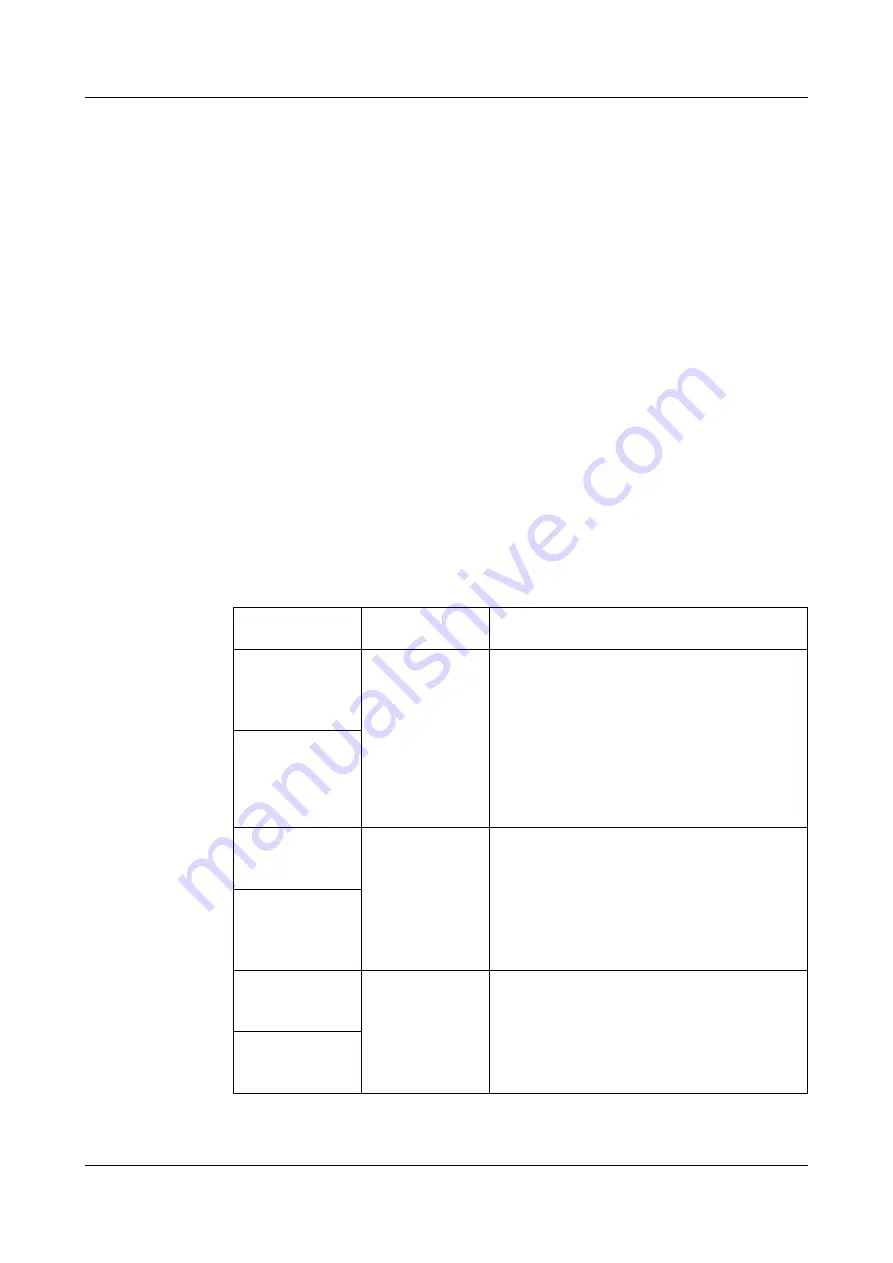
9 Parameterization
110
9.2
Parameter Sets (Controller parameter)
The parameters for the controller channels determine the control response of
the individual control circuits. For stable control response, these parameters
must be matched to the prevailing process conditions. Each controller channel
has two parameter sets; the selection is made by means of a binary signal. "Pa-
rameter set 1" is active by default. The second set can be activated as an alter-
native via the binary signal. In this way, it is possible to match each controller
channel to the changing process conditions in order to maintain a stable control
response.
The best parameter settings can usually be found by the controllers' self-optimi-
zation function. This approach, however, works only with linear processes.
Operating the controllers Page 93
For nonlinear processes (control paths), it is advisable to set the parameters
manually.
The following table provides an overview of the parameter sets for the controller
channels. Depending on the configuration of the particular controller channel,
only valid parameters are active for entry. Those not used appear in light gray,
but cannot be edited. Duplicate parameters refer to the first and second control-
ler output.
Open:
Device Menu
r
Parameterization
r
Parameter
Sets
r
Controller 1 to 4
r
Parameter Set 1 and 2
.
Parameter
(Formula sym.)
Setting op-
tions
Explanation
Proportional-
range 1
(X
p1
)
0 to 9999.9
(Unit
dependent on
the actual value
input variable)
factory setting:
0.0
Range of the actual value in which the con-
troller output is proportional to the control
deviation. The smaller the proportional
band selected, the larger the change in
controller output for the control deviation.
If the proportional band is set to a value of
0, the controller functions automatically as
a limit monitor without a PID controller
structure.
Proportional-
range 2
(X
p2
)
Rate time 1
(T
v1
)
0 to 9999 s
factory setting:
80.0 s
Affects the derivative component (D-term)
of the controller output signal. The purpose
of the D-term is to damp the change of the
actual value with time, and thereby sup-
press the hunting tendency.
The effect of the D-term increases as the
derivation time increases
Derivative time
2
(T
v2
)
Reset time 1
(T
n1
)
0 to 9999 s
factory setting:
350.0 s
Affects the integral component (I-term) of
the controller channel.
The purpose of the I-term is to minimize
persistent control deviations. The effect of
the I-term decreases as the reset time in-
creases.
Reset time 2
(T
n2
)
Summary of Contents for AQUIS touch P 202580
Page 12: ...Content...
Page 26: ...4 Identifying the device version 26...
Page 29: ...29 5 Mounting Mounting depth with Ci conductivity sensor 283 3 mm 2 3 mm 36 mm 25 mm 23 2 mm...
Page 32: ...5 Mounting 32...
Page 64: ...7 Startup 64...
Page 100: ...1 2 3 4 5...
Page 107: ...107 8 Operation Example of a Quad View...
Page 108: ...8 Operation 108...
Page 114: ...9 Parameterization 114...
Page 160: ...10 Configuration 160...
Page 182: ...13 Calibrating a pH measuring chain 182...
Page 196: ...16 Calibrating CR conductivity sensors 196...
Page 206: ...17 Calibrating Ci conductivity sensors 206...
Page 214: ...18 Calibrating universal inputs 214...
Page 228: ...19 PC Setup Program 228...
Page 319: ...319 20 Technical data...
Page 320: ...20 Technical data 320...
Page 321: ......