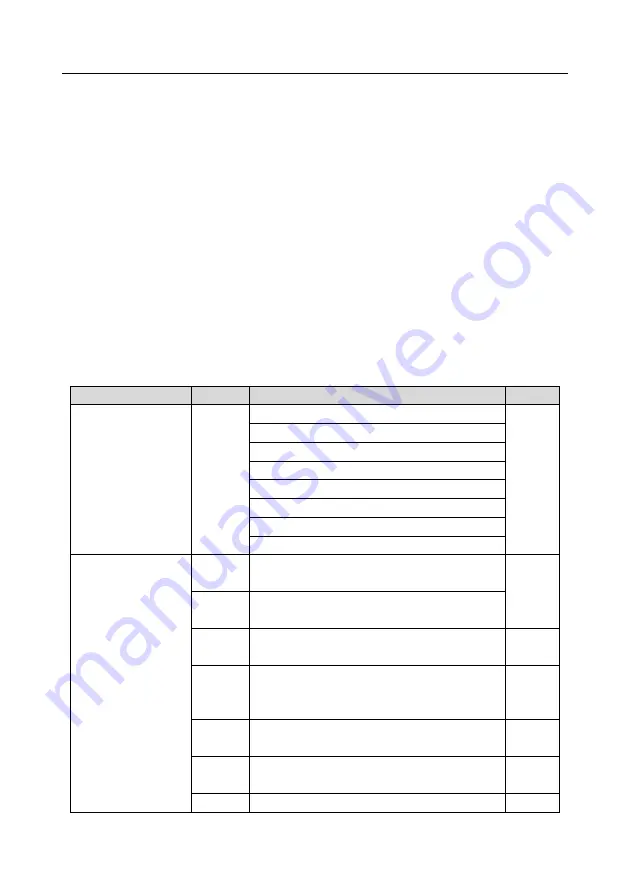
Goodrive350 series high-performance multifunction VFD
Communication
-317-
Note:
The parameters in the P99 group are set by the manufacturer. They cannot be read or modified.
Some parameters cannot be modified when the VFD is running; some cannot be modified
regardless of the state of the VFD. Pay attention to the setting range, unit, and related description
of a parameter when modifying it.
The service life of the Electrically Erasable Programmable Read-Only Memory (EEPROM) may
be reduced if it is frequently used for storage. Some function codes do not need to be stored
during communication. The application requirements can be met by modifying the value of the
on-chip RAM, that is, modifying the MSB of the corresponding function code address from 0 to 1.
For example, if P00.07 is not to be stored in the EEPROM, you need only to modify the value of
the RAM, that is, set the address to 8007H. The address can be used only for writing data to the
on-chip RAM, and it is invalid when used for reading data.
9.4.5.2 Description of other Modbus function addresses
In addition to modifying the parameters of the VFD, the master can also control the VFD, such as start
and stop it, and monitor the operation state of the VFD.
The following table describes other function
parameters.
Function
Address
Data description
R/W
Communication-based
control command
2000H
0001H: Forward running
R/W
0002H: Reverse running
0003H: Forward jogging
0004H: Reverse jogging
0005H: Stop
0006H: Coast to stop
0007H: Fault reset
0008H: Jogging to stop
Communication-based
value setting
2001H
Communication-based frequency setting (0
–
Fmax, unit: 0.01 Hz)
R/W
2002H
PID setting, range (0
–1000, 1000 corresponding
to 100.0%)
2003H
PID feedback, range (0
–1000, 1000
corresponding to 100.0%)
R/W
2004H
Torque setting (-3000
–+3000, 1000
corresponding to 100.0% of the rated current of
the motor)
R/W
2005H
Setting of the upper limit of the forward running
frequency (0
–Fmax, unit: 0.01 Hz)
R/W
2006H
Setting of the upper limit of the reverse running
frequency (0
–Fmax, unit: 0.01 Hz)
R/W
2007H
Upper limit of the electromotion torque (0
–3000,
R/W