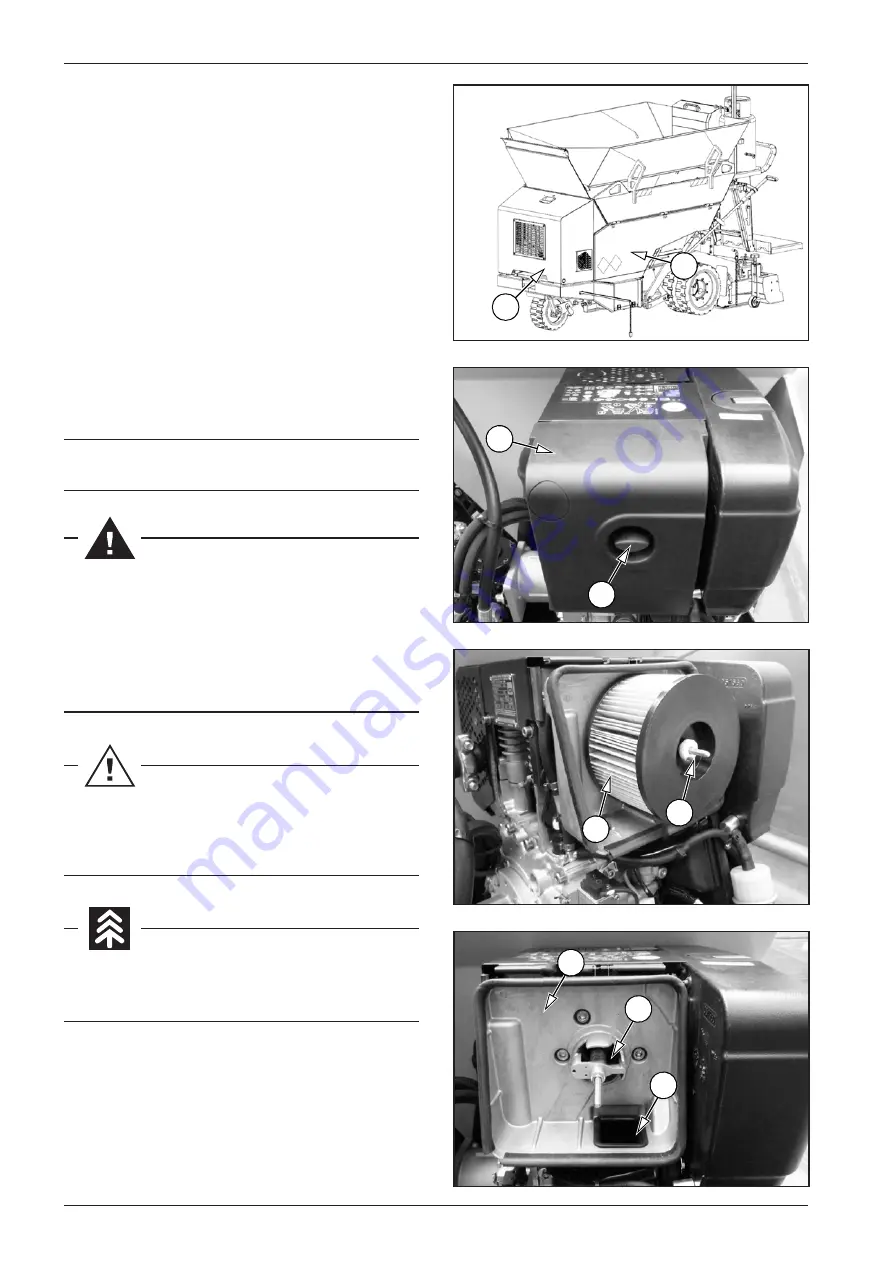
162
F80W
D451143
6
5
D451144
9
8
7
D451126
1
2
D451127A
3
4
3.6 Lubrication and maintenance operations
3.6.24 Air filter replacement
Perform air filter replacement when the machine is parked on
a flat and solid surface with the engine and battery disconnecter
off.
Air filter replacement procedure:
• Open the left material hopper side cover (1).
• Open the engine bonnet (2).
• Unlock the air filter cap (3) and remove the inlet air filter
cover (4).
• Remove the nut (5) and the air filter (6).
• Tighten the inlet openings (7) and (8) are free of dirt and for-
eign objects.
• Clean the air filter body (9) and the air filter cover (4).
• Mount a new air filter (6) and screw the nut (5).
• Mount the air filter cover (4) ad lock the air filter cap (3).
Air filter
Order number: 4812088419
Perform air filter replacement when the machine is
parked on a flat and solid surface with the engine and
battery disconnecter off.
When replacing the air filter, use the prescribed protec-
tive equipment.
There is a risk of burns from the hot parts of the engine.
Do not use compressed air to clean the air filter body and
cover; there is a risk of ingress of foreign objects to suc-
tion holes of air inlets.
Hand over the dismounted air filter for disposal accord-
ing to the national regulations.
Summary of Contents for Dynapac F80W
Page 1: ...OPERATING MANUAL Asphalt paver wheeled F80W Hatz 4812217930 ...
Page 2: ......
Page 4: ......
Page 6: ......
Page 14: ...8 F80W ...
Page 15: ...9 F80W SPECIFICATION MANUAL 1 SPECIFICATION MANUAL F80W Hatz Tier 4 Final ...
Page 18: ...12 F80W W1 W2 W W3 W4 B L L1 H H1 D451170A A L2 1 2 Dimensional drawing of the machine ...
Page 32: ...26 F80W Notes ...
Page 33: ...27 F80W SPECIFICATION MANUAL Notes ...
Page 34: ...28 F80W ...
Page 35: ...29 F80W OPERATING MANUAL 2 OPERATING MANUAL F80W Hatz Tier 4 Final ...
Page 62: ...56 F80W ...
Page 79: ...73 F80W 451043 451044 D451042 OPERATING MANUAL Augers Screed Conveyor ...
Page 123: ...117 F80W OPERATING MANUAL Notes ...
Page 124: ...118 F80W ...
Page 125: ...119 F80W MAINTENANCE MANUAL 3 MAINTENANCE MANUAL F80W Hatz Tier 4 Final ...
Page 126: ...120 F80W ...
Page 191: ...185 F80W 451190 MAINTENANCE MANUAL ...
Page 193: ...187 F80W 451900 1 1 1 11 5 A 12 V 2 2 10 12 3 3 3 4 5 4 6 7 8 9 8 MAINTENANCE MANUAL ...
Page 196: ...190 F80W 3 8 Appendices Notes ...
Page 197: ......
Page 198: ...www dynapac com ...