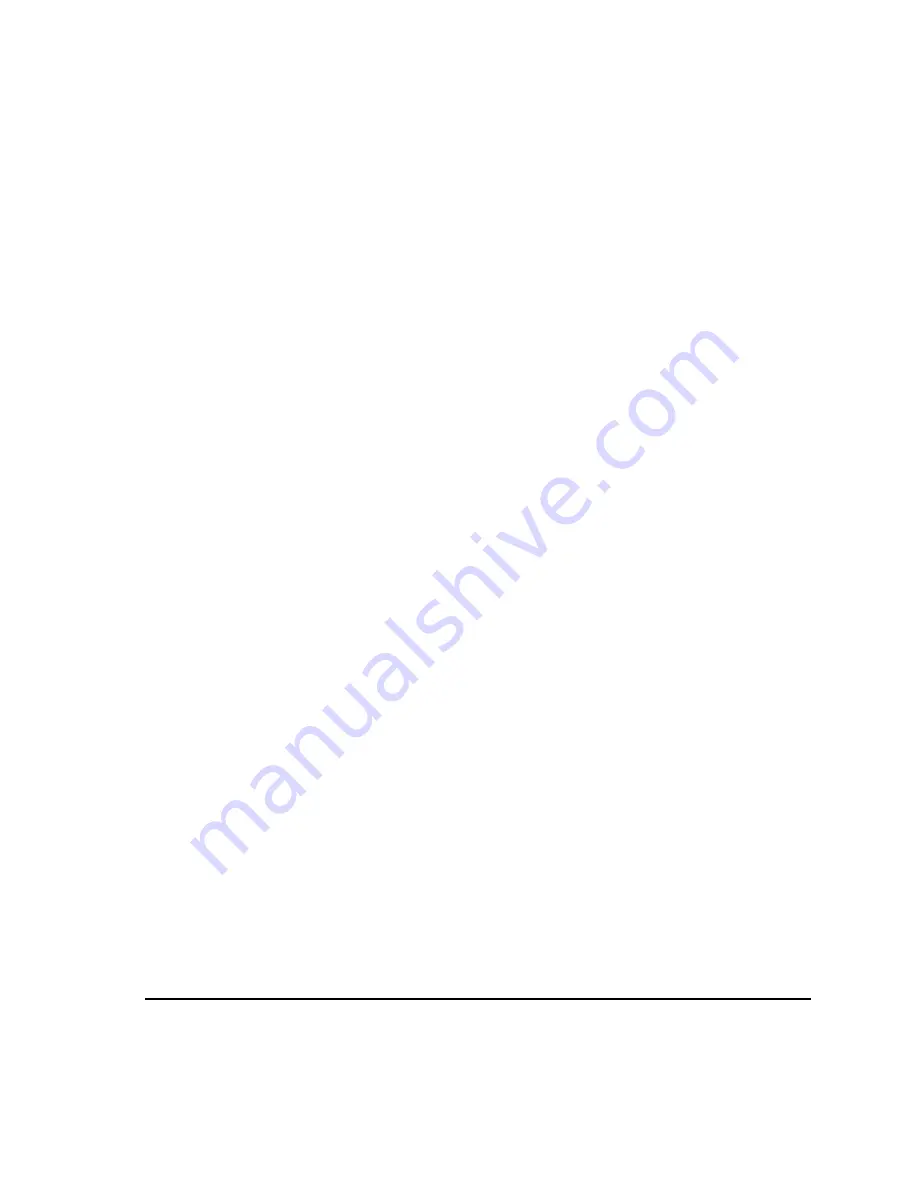
3-171
Laser Address Selection
Sine Curve Shape
The sine curve for each machine is used to determine the alignment condition of
the machines and the quality of the acquired data. The lower the curve fit per-
centage is during an alignment job the more of a problem and difficult, if not
impossible, it can become to complete the alignment job. When a low curve fit per-
centage occurs, the process of determining its cause needs to begin. The best place
to start is to look at the sine fit curve.
If the data points appear grouped in straight horizontal rows configured in a stair
step pattern the acquired data is possibly bad. Make sure that both laser heads are
mounted properly on the shaft of each machine, check the coupling, and acquire
new data. When the only place to mount the laser heads is on a flexible type cou-
pling, make sure the laser heads are mounted on sections of the coupling that flex
independently of each other. If the coupling is a rigid coupling, whether you
mount the laser heads on the shafts or the coupling, the coupling must be removed
or broken loose.
If the machines are connected by a jackshaft, spool, or spacer coupling do not
mount the laser heads on the center section of the coupling. Mounting the laser
heads on the same section of a flexible coupling, on machines connected by a rigid
coupling, or on the center section of a jackshaft is like mounting the laser heads on
a straight piece of rigid pipe. In this case, the stair step pattern is the result of no mis-
alignment being present. A small amount of sag in the pipe and a low variability
level due to something other than misalignment may appear as misalignment. For
this reason, placing the laser heads on a straight piece of rigid pipe to check them
is not recommended.
If the laser heads are mounted correctly and the data still appears grouped in the
stair step pattern, check the status of the laser heads for a possible hardware
problem.
Although the 8215/8225 laser fixtures are designed to be rotated a full revolution
in two seconds, make sure to use a smooth, uniform acceleration and deceleration
during the rotation for accurate, reliable, and repeatable data. Also, make sure no
obstacles are blocking the laser beam during the rotation and make sure both
beams remain in the targets for at least 45° of the rotation of the laser heads.
Emerson recommends you sweep at least 90°; however accuracy still may be
reduced even at 90°.
If the laser heads are being swept correctly check the status of the laser heads for a
possible hardware problem.
Summary of Contents for 2130 RBM Consultant Pro
Page 6: ...vi ...
Page 20: ...1 8 Fixtures Case Layout top section ...
Page 90: ...3 10 Horizontal Alignment ...
Page 364: ...5 22 Straightness Measurements ...