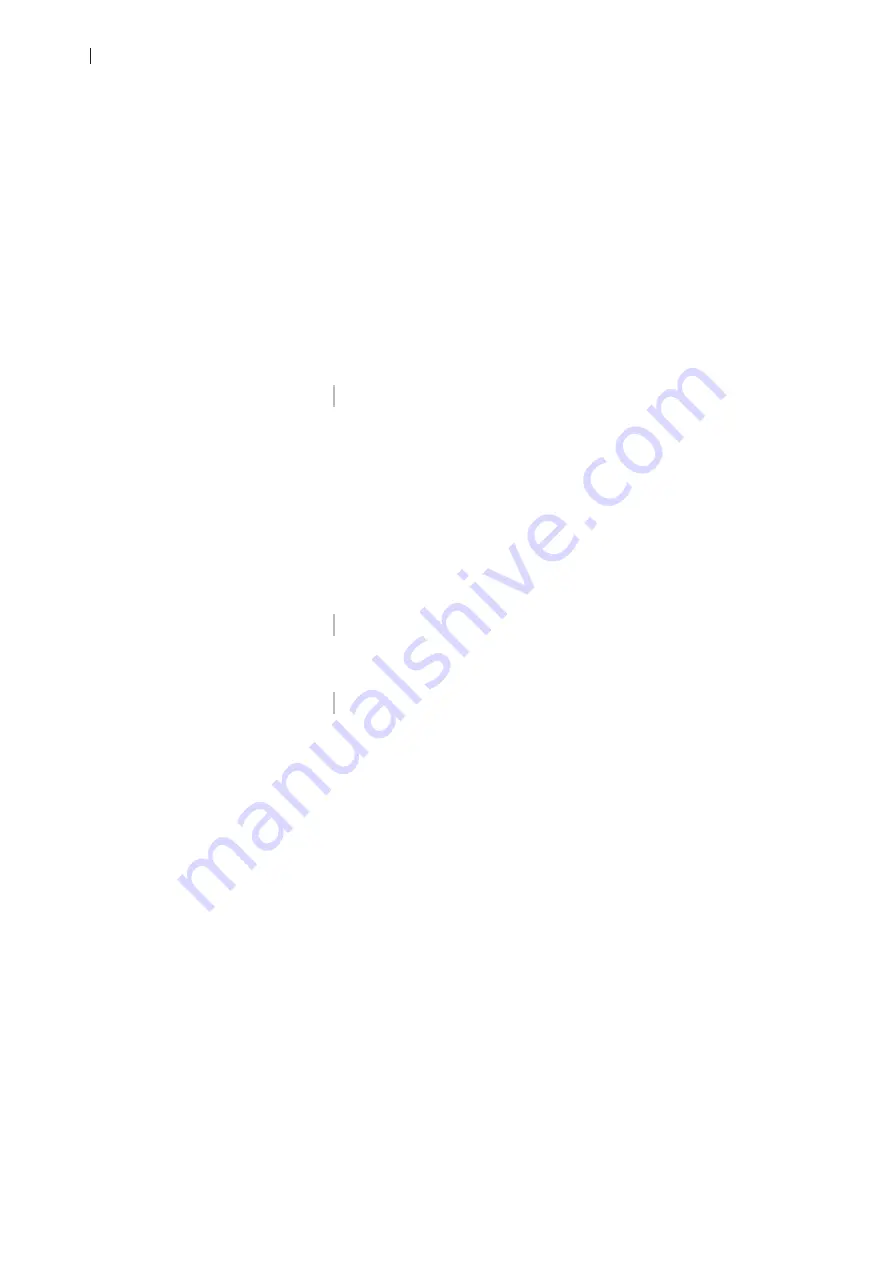
EN
BEFoRE CoMMISIonInG
DiBO 14
Before commisioning
Before every start up, all essential parts of the high-pressure cleaner must be
checked, by taking them in consideration like for example: is the lance coupling
tight, check the high pressure hoses and the electrical wiring on damages.
Check, before plug in the plug in the socket or the electric indications on the
name plate are suitable with the values of the main power supply (for example:
elektric tension,...) (if applicable). operate the machine. Rinse the hoses,
spray gun and lance minimum 1 minute with clean water (aim the spray gun in
free space). Check whether hazardous substances such as asbestos and oil
can come loose from the object to be cleaned and pollute the environment.
persuade yourself of the safety requirements mentionned in previous chapter.
leave the main switch / key switch on position 0- oFF. Before putting into
use: close the protective cap (if applicable) & at option tarpaulin (if applicable):
dismount the tarpaulin.
ACCOMPLISH WATER SUPPLY AND WATER DISCHARGE
1
Accomplisch water supply
The water supply line can be connected (according circumstances) on their own
water supplies (under pressure, ...) or on a drinking water supply with a water
barge. When the machine is connected to the drinking water supply, the existing
regulations about that must be observed (En 1717). If necessary place a filter in
the water supply line.
• Water supply under pressure:
Maximum hose length 50 m (160 ft), minimum hose diameter (internal) 12.7
mm (1/2”).
Check the water pressure by means of a watermeter.
• Water supply at units with hT- pumps:
When the unit has a hT- pump a pre-pressure pump must be installed.
2
Discharging water
Verify whether all water drains are correctly connected to the sewer system.
Take the necessary measures to ensure that the waste water is pure enough to
discharge/drain.
3
Anti- legionella bacterium measure
If the machine has estood still some time, the water in the machine must be
discharged above a drain.
Stagnant water that is warm between 20-55 ° C can cause the legionella
bacterium.
• Clean therefore the pipes and vessels annually.
• Rinse periodically.
• Remove possible sediment.
FILLING THE FUEL TANK
The cleaner will be delivered with empty fuel tank, fill the tank with the right fuel
before the first use. When the fuel tank is empty, the fuel pump runs dry and
these become defective! avoid mess of fuel, certainly on warm machine parts.
The tank of the burner fill with light fuel oil or diesel oil ( DIn 51 603 ). Respect
the fill capacity of the fuel tank. See technical data for tank reserve and fuel
type.
At temperatures under 8°C the fuel starts coagulate (paraffin
dissidence). As a result, difficulties can arise at starting the diesel
engine and/or burner. DiBO advise to add an coagulation point - or
flow improvement during the cold period (winter months) to the fuel.
As an alternative “winter diesel” can be refuelled in a filling station.
Summary of Contents for SBH-G-D
Page 2: ......
Page 4: ......
Page 54: ...NL Brander BR1000G instructies en voorschriften DiBO 54 31...
Page 55: ...Brander BR1000G instructies en voorschriften NL DiBO 55 32...
Page 56: ...NL Brander BR1000G instructies en voorschriften DiBO 56 33...
Page 57: ...Brander BR1000G instructies en voorschriften NL DiBO 57 34...
Page 66: ......
Page 68: ......
Page 98: ......
Page 100: ......
Page 150: ...EN Combustion chamber gas heated instructions regulations DiBO 54 31...
Page 151: ...Combustion chamber gas heated instructions regulations EN DiBO 55 32...
Page 152: ...EN Combustion chamber gas heated instructions regulations DiBO 56 33...
Page 153: ...Combustion chamber gas heated instructions regulations EN DiBO 57 34...
Page 162: ......
Page 164: ......
Page 206: ...DE Brennerkammer BR1000G Anweisungen Vorschriften DiBO 46 23 30 Schaltplan BR1000G...
Page 214: ...DE Brennerkammer BR1000G Anweisungen Vorschriften DiBO 54 31...
Page 215: ...Brennerkammer BR1000G Anweisungen Vorschriften DE DiBO 55 32...
Page 216: ...DE Brennerkammer BR1000G Anweisungen Vorschriften DiBO 56 33...
Page 217: ...Brennerkammer BR1000G Anweisungen Vorschriften DE DiBO 57 34...