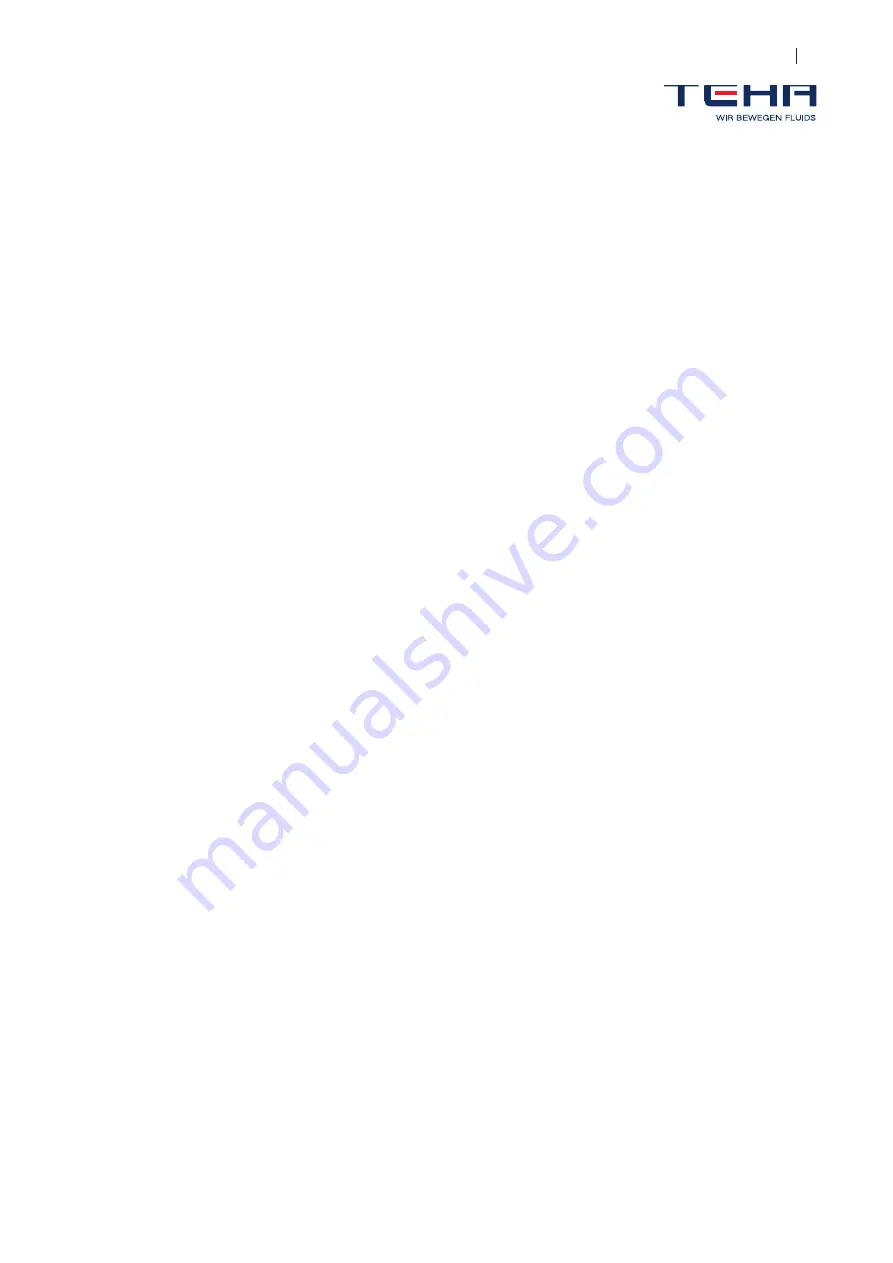
CoMBuSTIon ChaMBER GaS hEaTED InSTRuCTIonS-REGulaTIonS
EN
DiBO 31
8
That means:
The cross section of the feeder tube has to be chosen in such manner that a pressure of at least 10 mbar exists
during the operation of the burner. The gas pressure switch is adjusted to this value.
Attention! The maximum thermal capacity can only be achieved by a flow pressure of 20 mbar.
(at measuring point 1 see picture 3 on page 11)
Gas meter and pre-pressure reducer should guarantee the flow pressure.
The burner stops, if the value goes below 10 mbar.
Rule of thumb: feeder tube = or larger ¾“ nominal width.
9.1.3 Liquefied gas
The “Regulations for prevention of accidents - Use of liquefied gas” (VBG 21) have to be considered.
The admissible types of gas are Propane and Butane. Sources for the supply of the gas may be liquefied gas tanks,
gas bottles or groups of gas bottles, their contents being larger than 30 kg.
The connection between the bottles and the burner requires a fracture proof safety tube with pressure reducer.
Dimension of the tube
: R 1“ x 3000 mm
Pressure reducer
: V = 10 kg / h
: Pa = 25-50 mbar
The complete set for connection is available from the manufacturer’s accessories range.
After the installation the burner must always be readjusted by a well trained professional according to the
respective type of gas.
10. General mounting recommendations:
10.1 Gas conduit
A preliminary test and a principal test in the conduit as well as a combined loading and leak test have to be carried out
according to the intended pressure level (See also i.e. TRGI’86, paragraph 7). The air needed for the test or the inert gas
must be displaced from the conduit.
10.2 Gas fittings
Pay attention to the sequence and the flow direction!
10.3 Thread connection of tube
Only those sealants may be used, which are tested and released by the DVGW.
(DVGW=German Association for the gas and water area)
10.4 Type of gas – change-over
The change-over to another type of gas absolutely requires the readjustment of the burner.
10.5 Operating instructions
The operating instructions, which are enclosed to each machine, have to be suspended close to the machine in a visible
position. In this connection we refer to the DIN 4755, item 10 and DIN 4656, item 6. (DIN=German industrial norm)
The address of the service company has to be noted on the operating instructions.
10.6 Instructions
Operator’s mistakes are often the cause of failures. Therefore, the personnel have to be well instructed about the
functioning of the machine. In case of repeated malfunctions the after-sales-service has to be called.
10.7 Installation recommendation
Machines, which are not being installed in closed rooms but in the open air, require special proceedings against damages
or frost. The manufacturer can be asked for the corresponding information.
Summary of Contents for SBH-G-D
Page 2: ......
Page 4: ......
Page 54: ...NL Brander BR1000G instructies en voorschriften DiBO 54 31...
Page 55: ...Brander BR1000G instructies en voorschriften NL DiBO 55 32...
Page 56: ...NL Brander BR1000G instructies en voorschriften DiBO 56 33...
Page 57: ...Brander BR1000G instructies en voorschriften NL DiBO 57 34...
Page 66: ......
Page 68: ......
Page 98: ......
Page 100: ......
Page 150: ...EN Combustion chamber gas heated instructions regulations DiBO 54 31...
Page 151: ...Combustion chamber gas heated instructions regulations EN DiBO 55 32...
Page 152: ...EN Combustion chamber gas heated instructions regulations DiBO 56 33...
Page 153: ...Combustion chamber gas heated instructions regulations EN DiBO 57 34...
Page 162: ......
Page 164: ......
Page 206: ...DE Brennerkammer BR1000G Anweisungen Vorschriften DiBO 46 23 30 Schaltplan BR1000G...
Page 214: ...DE Brennerkammer BR1000G Anweisungen Vorschriften DiBO 54 31...
Page 215: ...Brennerkammer BR1000G Anweisungen Vorschriften DE DiBO 55 32...
Page 216: ...DE Brennerkammer BR1000G Anweisungen Vorschriften DiBO 56 33...
Page 217: ...Brennerkammer BR1000G Anweisungen Vorschriften DE DiBO 57 34...