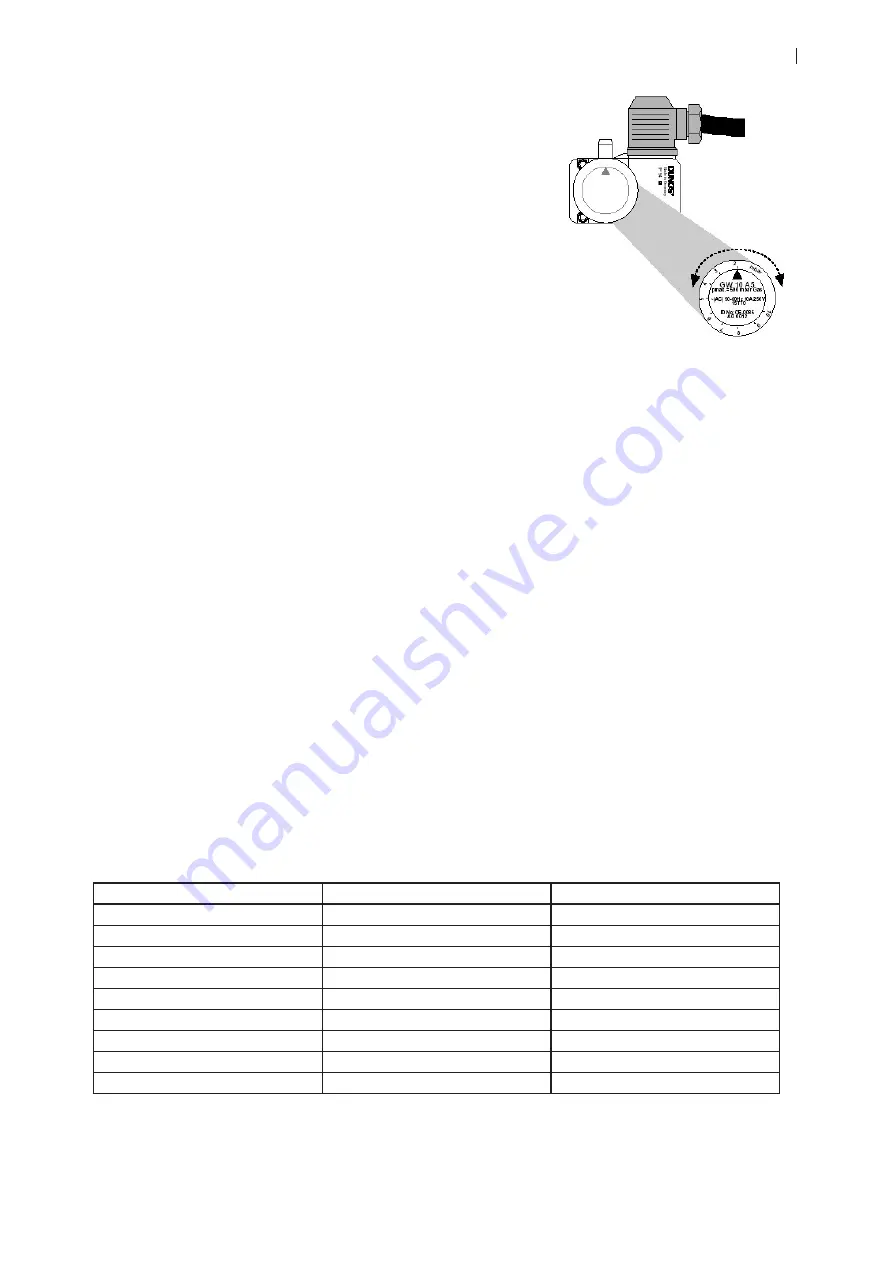
CoMBuSTIon ChaMBER GaS hEaTED InSTRuCTIonS-REGulaTIonS
EN
DiBO 35
12
14.12 The gas pressure control device
( Picture 4 )
Adjustment: 10 mbar
14.13 Basic adjustment of the gas burner
14.13.1 Gas pressure:
Initial position: Turn the pressure regulating screw to the left up to the limit stop.
Natural gas L : ca. 7-8,8 mbar (30 rotations to the right).
Natural gas H : ca. 7,5-8 mbar (18 rotations to the right).
Liquefied gas : ca. 6-6,3 mbar (12 rotations to the right).
The pressure measurement should be tapped from No. 5 (page 11, picture 3).
14.13.2 Quantity of air:
Place the gate valve in such manner, that approx. 2/3 of the intake stays free.
14.13.3
Please see data sheet page 17 for
the adjustment of the electrodes and baffle plate!
Attention: The basic adjustment only serves to take the burner into operation.
After that the correct adjustment must absolutely be carried out by means of a flue gas tester.
14.14 Tighten heating coils nuts
After 50 operating hours the nuts of the heating coils have to be tightened again, as the heating coil can gravitate in
the oxid ceramic disc. Especially when operating in mobile areas.
15. The gas firing automat type Siemens
Type LME21.130 C2 has the following tasks:
a. Observation of the air and gas pressure.
b. Observation of the flame by means of the ionization current.
c. Observation of the burner motor and the gas valve.
(see attachment page 31-36)
16. Adjustment data for the combustion chamber BR1000G
16.1 Gas burner
The factory carries out the adjustment of the gas burner regarding the distances of the electrodes and the baffle plate
according to drawing page 17.
This fixed adjustment must absolutely not be changed under any circumstances.
16.2 Heating capacity and modification of the gas type
The heating capacity of the burner can be varied between 45 and 70 KW. If the heating capacity and the gas type are being
modified, only the quantities of gas and air have to be changed accordingly. These adjustments should be carried out by
well trained personnel only.
16.3 Regulation- and safety devices in general
The BR1000G Gas is equipped with the following regulating and safety devices:
Description
Adjustment value
Remarks
Barometric pressure cell for gas
10 mbar
measuring point 1, see page 11 picture 3
Barometric pressure cell for air
2 mbar
Gas pressure switch
adjustable
Depending on type of gas and capacity
Regulator of gas quantity
max
Water-flow switch
6 Ltr./min.
Water-pressure switch
20 bar
Fixed adjustment
Exhaust temperature limiter
250°C
adjustable 230 – 400°C
Digital(Thermostat)
0 – 95°C
adjustable
Safety valve
adjustable 20 – 220 bar
Each maintenance and service should include the verification and – if necessary – the re-adjustment of the values.
Picture 4
Summary of Contents for SBH-G-D
Page 2: ......
Page 4: ......
Page 54: ...NL Brander BR1000G instructies en voorschriften DiBO 54 31...
Page 55: ...Brander BR1000G instructies en voorschriften NL DiBO 55 32...
Page 56: ...NL Brander BR1000G instructies en voorschriften DiBO 56 33...
Page 57: ...Brander BR1000G instructies en voorschriften NL DiBO 57 34...
Page 66: ......
Page 68: ......
Page 98: ......
Page 100: ......
Page 150: ...EN Combustion chamber gas heated instructions regulations DiBO 54 31...
Page 151: ...Combustion chamber gas heated instructions regulations EN DiBO 55 32...
Page 152: ...EN Combustion chamber gas heated instructions regulations DiBO 56 33...
Page 153: ...Combustion chamber gas heated instructions regulations EN DiBO 57 34...
Page 162: ......
Page 164: ......
Page 206: ...DE Brennerkammer BR1000G Anweisungen Vorschriften DiBO 46 23 30 Schaltplan BR1000G...
Page 214: ...DE Brennerkammer BR1000G Anweisungen Vorschriften DiBO 54 31...
Page 215: ...Brennerkammer BR1000G Anweisungen Vorschriften DE DiBO 55 32...
Page 216: ...DE Brennerkammer BR1000G Anweisungen Vorschriften DiBO 56 33...
Page 217: ...Brennerkammer BR1000G Anweisungen Vorschriften DE DiBO 57 34...