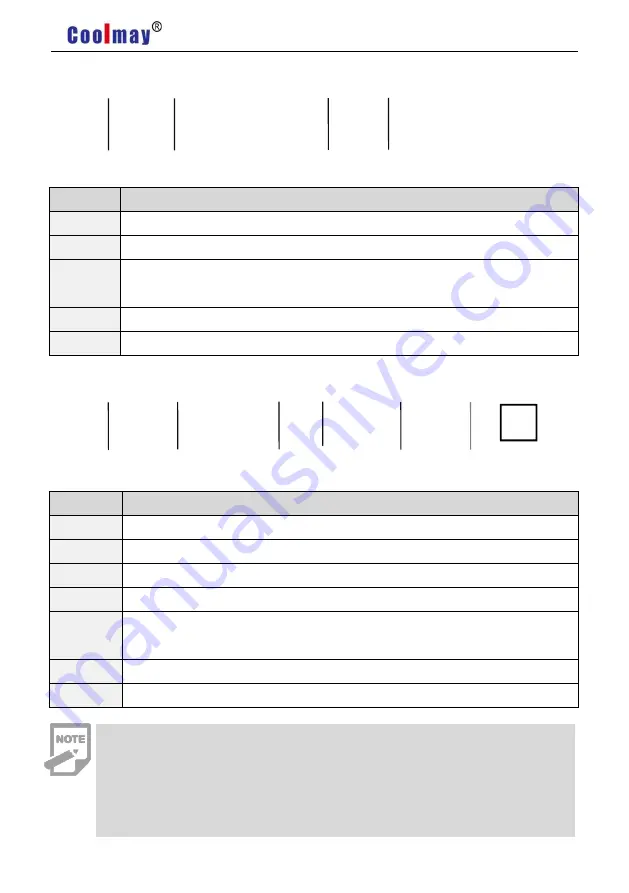
C200H AC Servo Manual
7
2.2
Servo Drive Naming Rule
C
200
H
-
-
-
□□□
2.3
Servo Motor Naming Rule
CN
130
-
040 25
A6
-
MH
B
Serial No.
Definition
①
Coolmay technology C series servo driver.
②
Power: 100:0.05KW~1KW. 200:1KW~2KW.
③
H: High performance and for 2500ppr incremental encoder or 17-bit
single/multi-turn absolute encoder.
④
The branch power range below 1KW: 40: 0.05KW~0.4KW; 75:0.4KW~0.75KW.
⑤
Special specifications: Customization.
Serial No.
Definition
①
Motor type, CN: CN series 4 opposite pole servo motor
②
Flange: 40(mm),60(mm),80(mm),90(mm),110(mm),130(mm).
③
Rated torque(
×
0.1N.m): 040=4N.m.
④
Rated speed(
×
100rpm): 25=2500rpm.
⑤
A6:17-bit single turn absolute. A1:17-bit multi-turn absolute. I2: 2500ppr
incremental encoder.
⑥
TJA: AMP connector. MH: Aviation connector.
⑦
B: with a brake, Null: without a brake.
①
②
③
④
⑤
②
③
④
⑤
⑥
⑦
①
1. The code 04025 means the motor rated toque is 4N.m and rated speed is
2500rpm.
2. The rated power: P=0.1047
×
N
×
T=0.1047
×
4
×
2500=1047W
≈
1KW.
T=rated torque, N=rated speed.
Summary of Contents for C200H Series
Page 1: ...https en coolmay com ...
Page 2: ...C200H AC Servo Manual https en coolmay com ...
Page 43: ...C200H AC Servo Manual 36 Pic 4 17 Ground Connection Handling Of Noise Filter ...
Page 52: ...C200H AC Servo Manual 45 5 2 2 Speed Mode Wiring 三相 Pic5 4 Speed Mode Wiring ...
Page 55: ...C200H AC Servo Manual 48 5 3 2 Torque Mode Wiring Pic5 6 Torque Mode Wiring ...