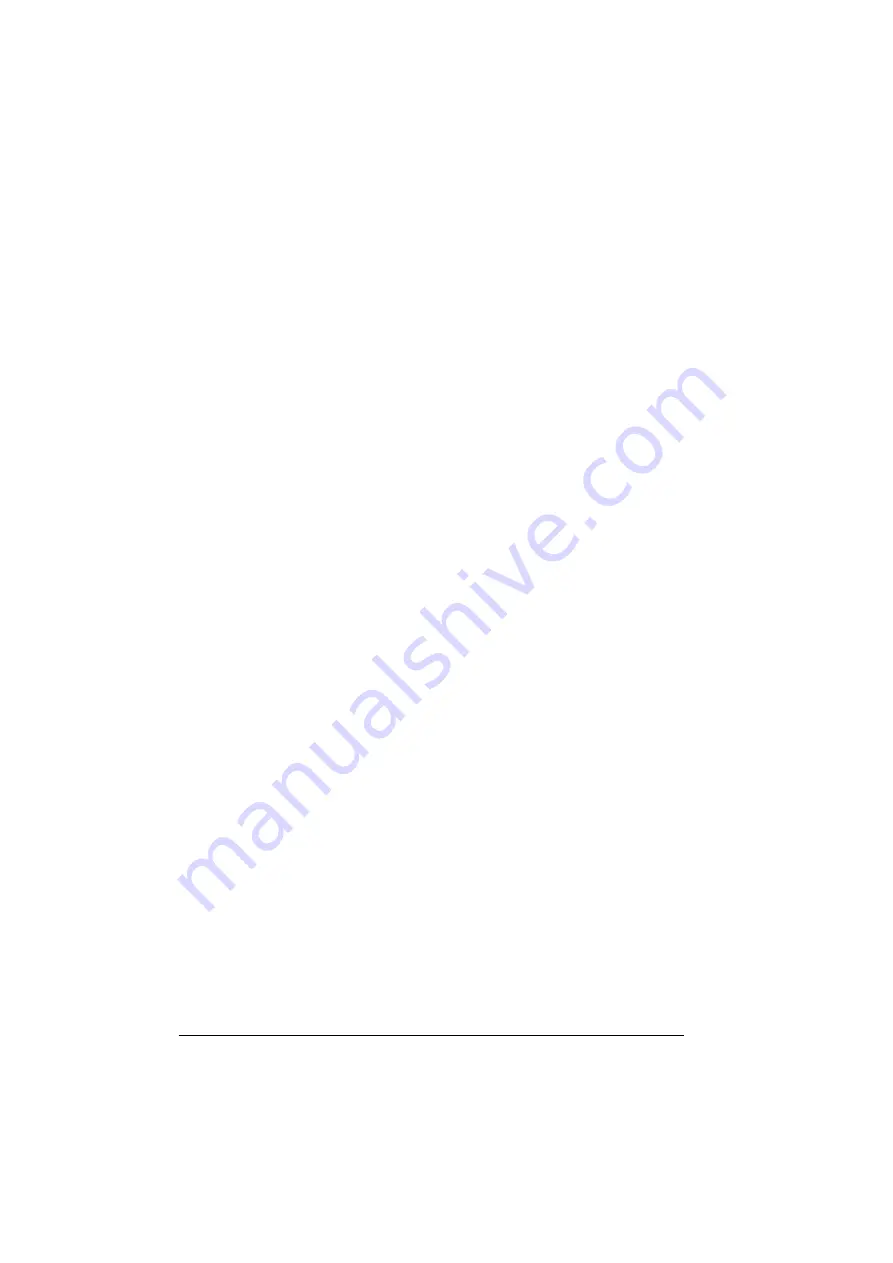
70 Program features
Notes:
• The function can be enabled only when the drive is a speed-controlled follower in
remote control mode.
• Drooping (
) is ignored when the load share function is active.
• The master and follower should have the same speed control tuning values.
• The speed correction term is limited by the speed error window parameters
and
. An active limitation
is indicated by
.
Communication
A master/follower link can be built by connecting the drives together with fiber optic
cables (may require additional equipment depending on existing drive hardware), or
by wiring together the XD2D connectors of the drives. The medium is selected by
parameter
Parameter
defines whether the drive is the master or a follower on
the communication link. Typically, the speed-controlled process master drive is also
configured as the master in the communication.
The communication on the master/follower link is based on the DDCS protocol, which
employs data sets (specifically, data set 41). One data set contains three 16-bit
words. The contents of the data set are freely configurable using parameters
…
. The data set broadcast by the master typically contains the control
word, speed reference and torque reference, while the followers return a status word
with two actual values.
The default setting of parameter
is
. With this
setting in the master, a word consisting of bits 0…11 of
four bits selected by parameters
is broadcast to the followers.
However, bit 3 of the follower control word is modified so that it remains on as long as
the master is modulating, and its switching to 0 causes the follower to coast to a stop.
This is to synchronize the stopping of both master and follower.
Note:
When the master is ramping down to a stop, the follower observes the
decreasing reference but receives no stop command until the master stops
modulating and clears bit 3 of the follower control word. Because of this, the
maximum and minimum speed limits on the follower drive should not have the same
sign – otherwise the follower would be pushing against the limit until the master finally
stops.
Three words of additional data can optionally be read from each follower. The
followers from which data is read are selected by parameter
in the master. In each follower drive, the data to be sent is selected by
…
. The data is transferred in integer format over the link, and
displayed by parameters
in the master. The data can then be
forwarded to other parameters using
…
Summary of Contents for ACS880-01 Series
Page 1: ...ABB industrial drives Firmware manual ACS880 ESP control program option N5600 ...
Page 4: ......
Page 12: ...12 Table of contents ...
Page 20: ...20 Introduction to the manual ...
Page 22: ...22 Using the control panel ...
Page 28: ...28 Control locations and operating modes ...
Page 146: ...146 Application macros ...
Page 502: ...502 Parameters ...
Page 606: ...606 Fault tracing ...
Page 662: ...662 Control chain diagrams ...