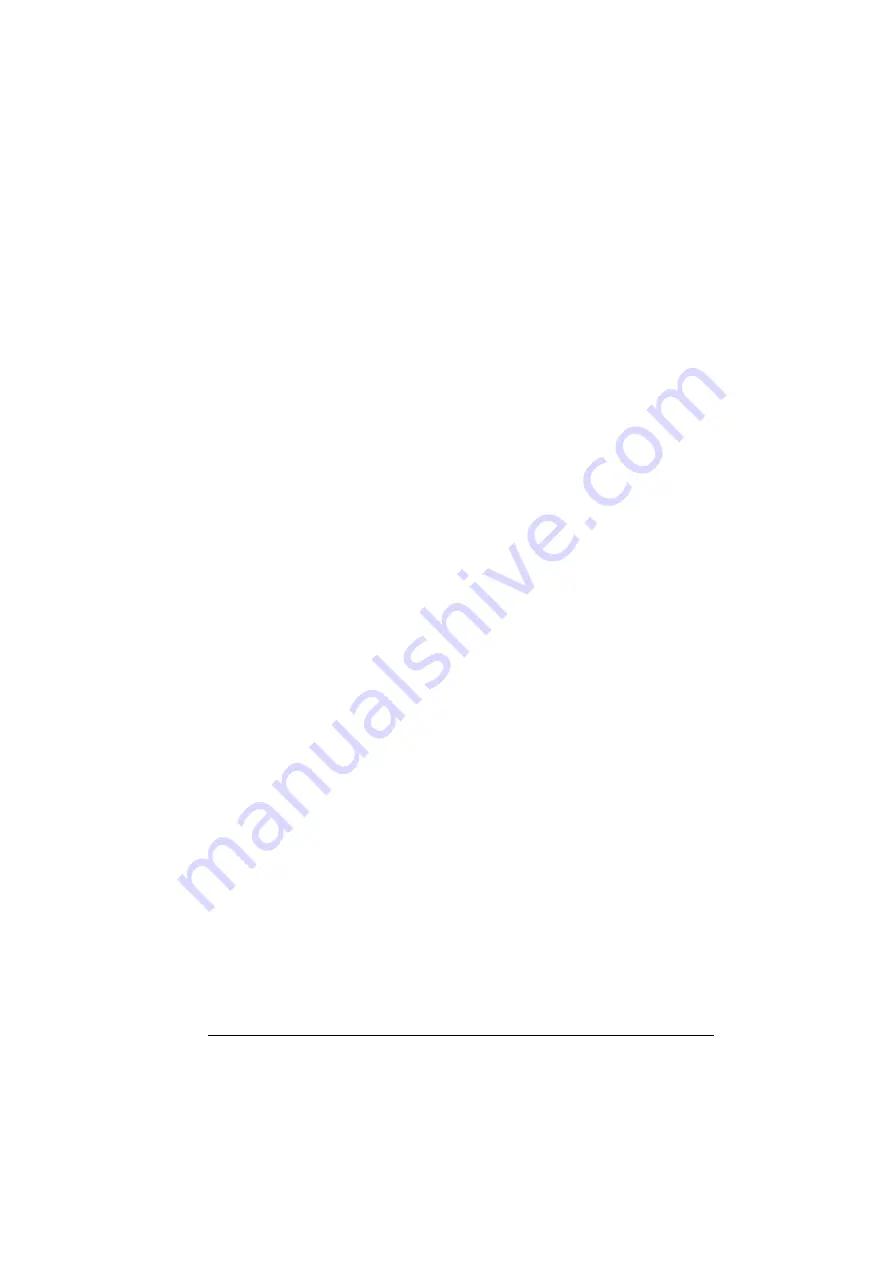
Program features 91
•
•
The cable drum turns one revolution per 50 revolutions of the motor shaft.
•
= 1)
•
= 1)
(These parameters need not be changed as position estimate is not being used
for feedback.)
•
= 7
•
= 10
The load moves 70 centimeters, ie. 7/10 of a meter, per one revolution of the
cable drum.
The load height in meters can be read from
, while
displays the rotational speed of the cable drum.
Example 2: Using two encoders
One encoder (encoder 1) is used for motor feedback. The encoder is connected to
the motor shaft through a gear. Another encoder (encoder 2) measures the line
speed elsewhere in the machine. Each encoder is configured as shown in
Configuration of HTL encoder motor feedback
above. In addition, the following
settings are made:
•
)
•
= 1)
•
The encoder turns three revolutions per one revolution of the motor shaft.
•
The line speed measured by encoder 2 can be read from
. This
value is given in rpm which can be converted into another unit by using
. Note that the feed constant gear
cannot be used in this conversion because it does not affect
.
Example 3: ACS 600 / ACS800 compatibility
With ACS 600 and ACS800 drives, both the rising and falling edges from encoder
channels A and B are typically counted to achieve best possible accuracy. Thus the
received pulse number per revolution equals four times the nominal pulse number of
the encoder.
In this example, an HTL-type 2048-pulse encoder is fitted directly on the motor shaft.
The desired initial position to correspond the proximity switch is 66770.
Summary of Contents for ACS880-01 Series
Page 1: ...ABB industrial drives Firmware manual ACS880 ESP control program option N5600 ...
Page 4: ......
Page 12: ...12 Table of contents ...
Page 20: ...20 Introduction to the manual ...
Page 22: ...22 Using the control panel ...
Page 28: ...28 Control locations and operating modes ...
Page 146: ...146 Application macros ...
Page 502: ...502 Parameters ...
Page 606: ...606 Fault tracing ...
Page 662: ...662 Control chain diagrams ...