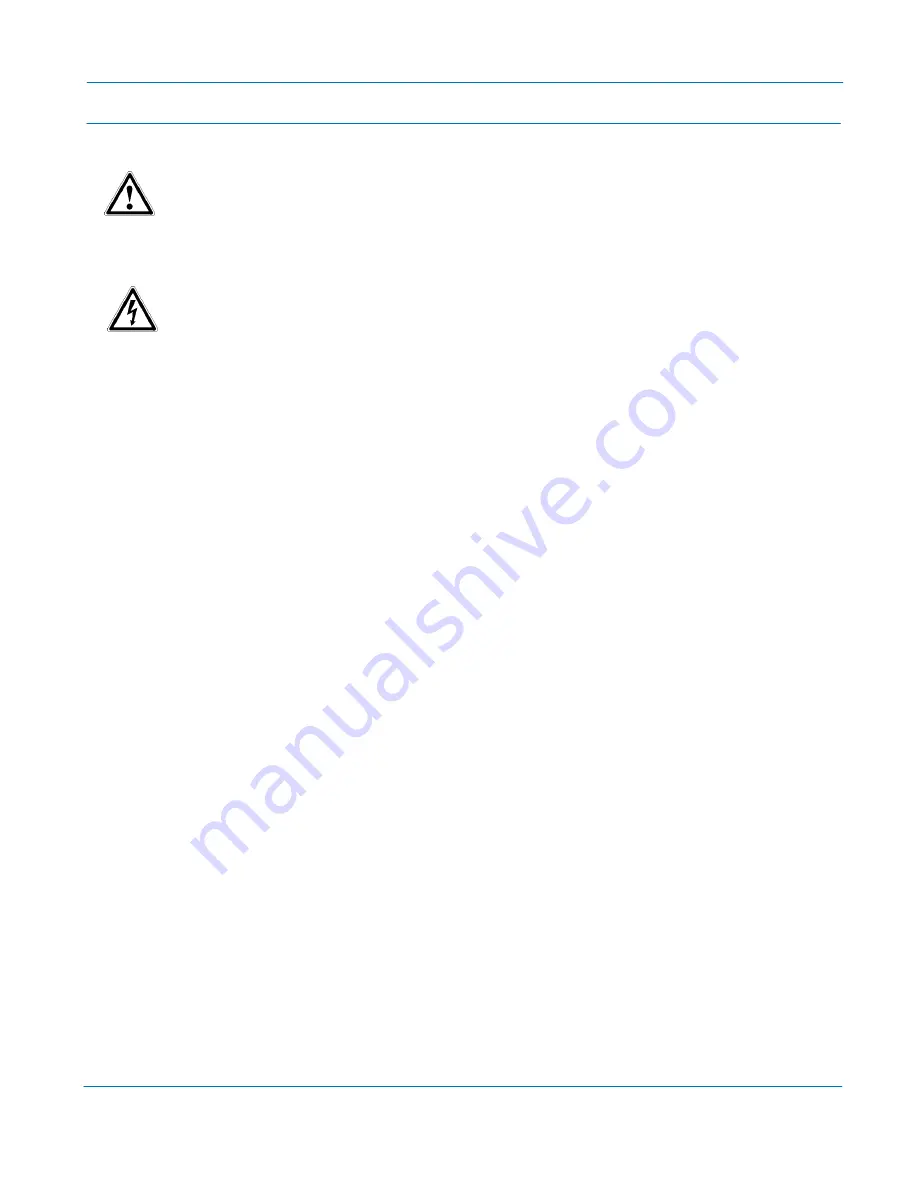
IMPORTANT – Read this first !!
Instruction
Manual:
Smartstart
®
6000
IMI0042
rev
K
Page
1
Read
all
operating
instructions
before
installing,
wiring,
operating,
servicing
or
inspecting
the
Smartstart
®
6000.
Ensure
that
the
instruction
manual
is
made
available
to
the
final
user
of
the
product
as
well
as
all
personnel
involved
in
any
aspect
of
installation,
adjustment
or
maintenance.
Your
Smartstart
®
6000
must
be
applied
and
installed
by
a
suitably
qualified
and
experienced
electrical
tradesperson
in
accordance
with
this
manual,
good
engineering
practice
and
all
local
rules
and
regulations.
There
are
hazardous
voltages
inside
the
Smartstart
®
6000
whenever
it
is
connected
to
an
electrical
supply.
The
Smartstart
®
6000
contains
high
energy
circuits
that
may
be
hazardous.
Do
not
operate
with
the
covers
removed
or
the
doors
of
the
enclosure
in
which
it
is
installed
open.
Do
not
touch
the
terminals
of
the
Smartstart
®
6000
or
any
associated
motor
and
wiring
when
it
is
energised,
even
if
the
Smartstart
®
6000
and
motor
are
stopped.
Electric
shock
may
result.
Do
not
modify
this
equipment
electrically,
mechanically
or
otherwise.
Modification
may
create
safety
hazards
as
well
as
voiding
the
UL
listing
of
models
so
listed.
The
Smartstart
®
6000
is
designed
to
drive
an
appropriately
rated
and
otherwise
suitable
3
phase
induction
motor.
It
is
not
suitable
for
single
phase
motors
or
other
types
of
motor
or
non
‐
motor
load.
Use
with
inappropriate
load
types
may
create
a
safety
hazard.
Where
the
Smartstart
®
6000
is
used
as
a
component
part
of
another
product,
it
is
the
purchaser's
responsibility
to
ensure
that
the
final
product
meets
all
of
the
necessary
safety,
EMC,
regulatory,
operational
and
other
requirements
for
that
product.
Requirements
for
the
purchaser's
final
product
may
be
substantially
different
to
the
requirements
for
stand
‐
alone
inverters.
The
Smartstart
®
6000
is
intended
for
use
only
in
fixed
wiring
applications.
It
is
not
intended
for
use
on
a
flexible
supply
cable.
Mount
the
Smartstart
®
6000
on
a
vertical,
incombustible
surface
such
as
metal
or
masonry.
Do
not
place
combustible
or
flammable
material
near
the
Smartstart
®
6000.
Failure
to
observe
these
precautions
may
create
a
fire
hazard
The
Smartstart
®
6000
is
manufactured
under
strict
quality
control
arrangements,
however
additional
and
independent
safety
equipment
must
be
installed
if
the
application
is
such
that
failure
of
the
product
may
result
in
personal
injury
or
property
damage.
Ensure
the
Smartstart
®
6000
is
applied
in
a
manner
that
does
not
adversely
affect
the
proper
operation
of
other
equipment
or
systems,
particularly
those
that
have
a
safety
function.
Install
emergency
stop
circuitry
that
removes
power
from
the
Smartstart
®
6000
and
does
not
depend
on
any
feature
of
the
product
for
proper
and
safe
operation.
The
Smartstart
®
6000
has
features
that
may
be
used
to
cause
an
automatic
restart
in
certain
circumstances.
The
overall
application
(machine
etc)
must
be
designed
such
that
automatic
restart
is
not
hazardous.
Do
not
install
this
equipment
in
locations
where
mechanical
damage
to
the
enclosure
is
possible.
In
particular,
consider
vehicles,
vandalism
and
attack
by
insects
or
animals.
Severe
equipment
damage
and
safety
hazards
may
result.
The
Smartstart
®
6000
offers
an
Essential
Services
Over
‐
ride
(ESO)
mode
of
operation.
This
mode
of
operation
intentionally
ignores
some
motor
and
starter
protection.
As
a
result
the
equipment
may
operate
outside
its
thermal
rating
and
void
any
warranty.
Содержание SMARTSTART 6000
Страница 1: ...ZENER VARIDRIVE SOLUTIONS ZENER SMARTSTART 6000 Soft Starter Instruction Manual...
Страница 2: ......
Страница 49: ...Appendix B Application Diagrams Technical Manual Smartstart 6000 IMI0042 rev K Page 46 General Purpose...
Страница 51: ...Appendix B Application Diagrams Technical Manual Smartstart 6000 IMI0042 rev K Page 48 Irrigation Pump...