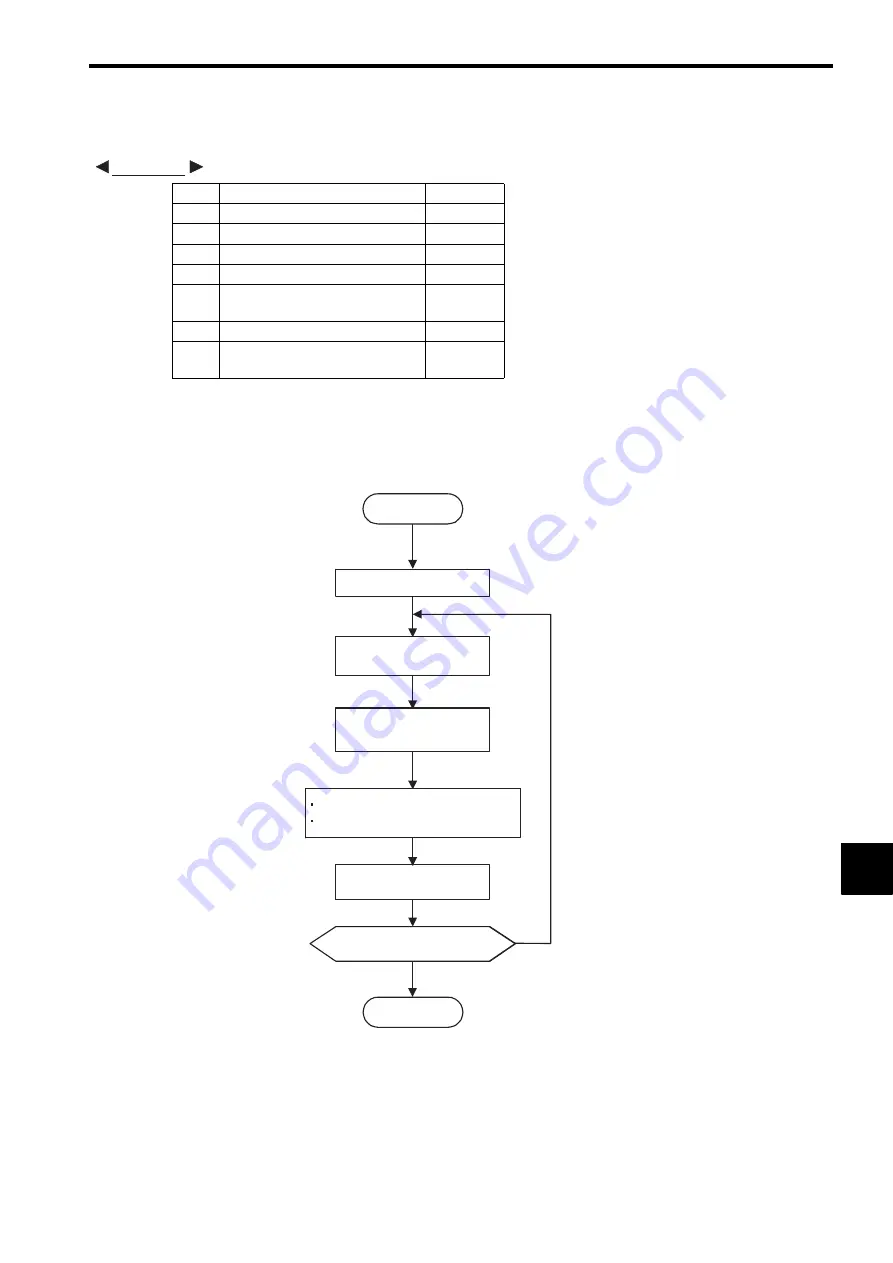
10.3 Using an Absolute Encoder
10-17
10
(c) Application Example of Simple Absolute Infinite Length Position Control Function
An example of using the simple absolute infinite length position control function is given below.
(d) Setting the Zero Point for a Simple Absolute Infinite Length Axis
Set the zero point as described here after initializing the absolute encoder to set the zero point of the machine
coordinate system and establish the machine coordinate system.
The procedure to set the zero point for a simple absolute infinite length axis is shown below.
* 1. The OL
48 value must be saved when it is set.
* 2. See the information on the next page for more details on saving the OL
48 value.
* 3. Execute with the ZSET command.
No.
Name
Setting
■
Calculation of the Number to Turns to Reset
360000 * 6 / 360000 * 5 = 6/5 (number of turns to reset)
■
Conditions
(59705+1) / (6/5) = 49755
The result is an integer, i.e., the remainder is 0, so the
simple absolute infinite length position control function
can be used.
4
Command Unit
2: deg
6
Command Unit per Revolution
360000
8
Gear Ratio [MOTOR]
6
9
Gear Ratio [LOAD]
5
10
Maximum Value of Rotary
Counter
360000
36
Encoder Resolution
16384
38
Max. Revolution of Absolute
Encoder
59705
EXAMPLE
Repeat for every axis.
Start
Servo ON
STEP to move to the
zero point.
OL
48 = OL
48 - IL
10
Save OL
48
*2
End
JOG to move close to
the zero point.
YES
NO
Set the zero point.
* 3
* 1
Has the setting for the required
axis been completed?