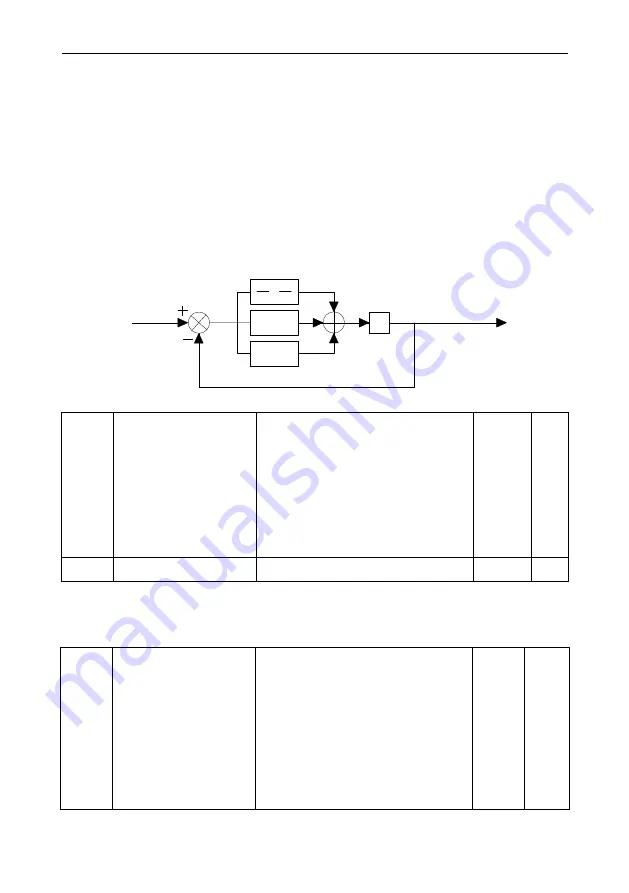
Parameter Description VD520 Series Inverter User Manual
- 148 -
FA Process PID Parameter Group
Process PID closed-loop control is the control mode in the control system using proportion (P),
integral (I) and differential (D) controller of three parts, make the diviation between the feedback value
and the instruction valueis gradually reduced, suitable for the flow rate, pressure, temperature and
other process control.
Proportional control (P)
The control variable of proportional to the deviation.
Integral control (I)
The control variable of proportional to deviation integral value, can eliminate the steady-state error.
Differential control (D)
The control variable of proportional to deviation variation rate, can predict the change trend of
deviation, rapid response to the dramatic changes, improve the dynamic performance, but easy to
introduce and enlarge the interference signals and cause the system unstable, please use caution.
Ti
S
1
1
Td*s+1
1
p
PID output
quantity
Feedback
Target
quantity
Fig 6-17 Process PID principle block diagram
FA-00
PID Given Source
0: FA-01 setting
1: AI1
2: AI2
3: Reserved
4: PULSE setting
5: Communication setting
6: Multi-reference setting
7: Keypad potentiometer
0
○
FA-01
PID Digital Giving
0.0%~100.0%
50.0%
○
This parameter is used to select the target volume for a given channel of process PID.
The set target volume of the process PID for the relative value, set range is 0.0%~0.0%. Similary, the
feedback quantity of PID also is relative quantity, the function of PID is to make the two relatively
equal.
FA-02
PID Feedback Source
0: A1
1: AI2
2: Reserved
3: AI1-AI2
4: PULSE setting
5: Communication setting
6: AI1+AI2
7: MAX (IAI1I, IAI2I)
8: MIN (IAI1I, IAI2I)
0
○
This parameter is used to select the feedback signal channel of process PID.
Содержание VD520 Series
Страница 2: ......
Страница 9: ...VD520 Series Inverter User Manual Safety and Precautions 5 damage or performance reduce ...