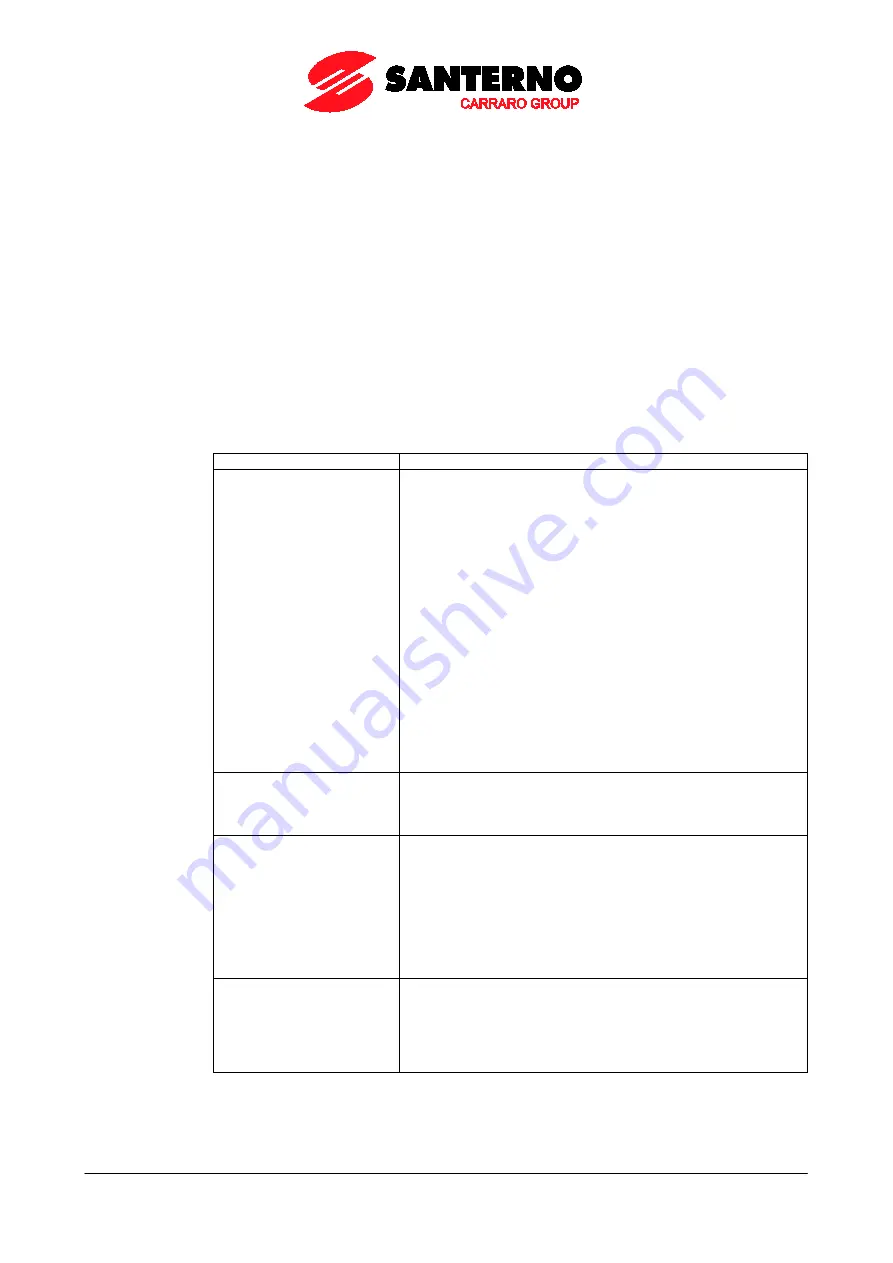
SINUS PENTA
PROGRAMMING GUIDE
44
/
486
attained. Decrease
P128
and
P129
by approx. 30%, then decrease the high values set for integral
time in
P125
and
P126
(keep both values equal) until an acceptable setpoint response is obtained.
Check to see if the motor runs smoothly at constant speed.
10) Possible
failures:
If no failure occurred, go to step 11. Otherwise, check the drive connections paying particular
attention to supply voltages, DC link and input reference. Also check if alarm messages are
displayed. In the MEASURES MENU, check the reference speed (
M000
), the reference speed
processed by the ramps (
M002
), the supply voltage of the control section (
M030
), the DC-link
voltage (
M029
), the condition of the control terminals (
M033
). Check to see if these readouts
match with the measured values.
11) Additional
parameter
modifications:
If the motor control is underperfoming, make sure that the following measurements are consistent
with the expected motor operation:
- estimated speed
M004
in respect to speed ramp
M002
,
- output frequency
M006
,
- generated torque
M012
and torque demand
M011
,
- output current
M026
,
- output voltage
M027
.
Proceed as follows:
Issue
What to do
Generation of weak torque
or inaccurate torque
delivery
Increase the flux boost at low frequency
P175h1
and adjust the
frequency range for the boost to occur via parameters
P175i1
and
P175j1
. The magnetization current at low frequency with
active current boost equals the no-load current value in
C021
increased by the value in
P175h1
(for example, if
C021
=27%
and
P175h1
=30%,
the magnetization current is
27%x1.3=35.1%). Up to the frequency value in
P175i1
, the
magnetization current is
C021
x (1+
P175h1
); at a frequency
higher than
P175j1
, the magnetization current is
C021
; at
intermediate frequency values, the magnetization current follows
a linear pattern. Too high magnetization current values may lead
to saturation of the motor flux, lower efficiency due to greater no-
load current, inaccurate torque adjustment or controller
instability. It is suggested that
P175j1
be applied at its maximum
value up to 50% of the rated frequency. Also, set
P175i1
in such
a way so as to obtain a rather smooth pattern (for example,
P175i1
set to half the value in
P175j1
). In case
P175i1
and
P175j1
are not correctly adjusted, torque adjustment may be
uneven or current variations may occur.
Generation of weak torque
at high speed
If the motor is not capable of delivering high torque at high speed
(close to rated torque or field weakening torque) or requires
excessive current in respect to the expected current, it is
possible to adjust rotor time constant
C025
.
Generation of weak torque
at low speed or in
regenerative mode
Change current distortion compensation parameters in VTC
control
P175a
,
P175b
,
P175c
. Change current distortion
compensation
P175b
first, then change positive and negative
current split
P175c.
For high values in
P175b
, also increase the linear pattern
threshold in
P175a
. If parameter
P175b
is set too high or
P175a
is set too low, rotor oscillations may occur, or it may happen that
the rotor is not kept standstill even in no-load conditions. If this is
the case, set lower values for the parameters above.
Low output voltage or weak
torque in field weakening
mode
Disable static field weakening by setting
C030
= Disable and
enable automatic field weakening by setting
C030a
>0.
In that way, the field weakening amplitude is automatically
adjusted to ensure adjusting the required speed at the maximum
allowable voltage fitting the rated motor voltage and the available
DC voltage.
When parameter
P003
= Standby Only (condition required for changing
Cxxx
parameters), you
can change
Cxxx
parameters only when the drive is DISABLED or STOPPED, whereas if
P003
=
S Fluxing, you can change
Cxxx
parameters when the motor is stopped but the drive is
enabled.
Before changing any parameters, remember that the correct code for parameter
P000
must be
Содержание PENTA MARINE
Страница 173: ...PROGRAMMING GUIDE SINUS PENTA 173 486 Figure 27 Response to the step based on the value of Kp when Ti is kept constant...
Страница 196: ...SINUS PENTA PROGRAMMING GUIDE 196 486 Figure 34 ANALOG Mode Figure 35 DOUBLE DIGITAL Mode...
Страница 197: ...PROGRAMMING GUIDE SINUS PENTA 197 486 Figure 36 General structure of the parameterization of a digital output...