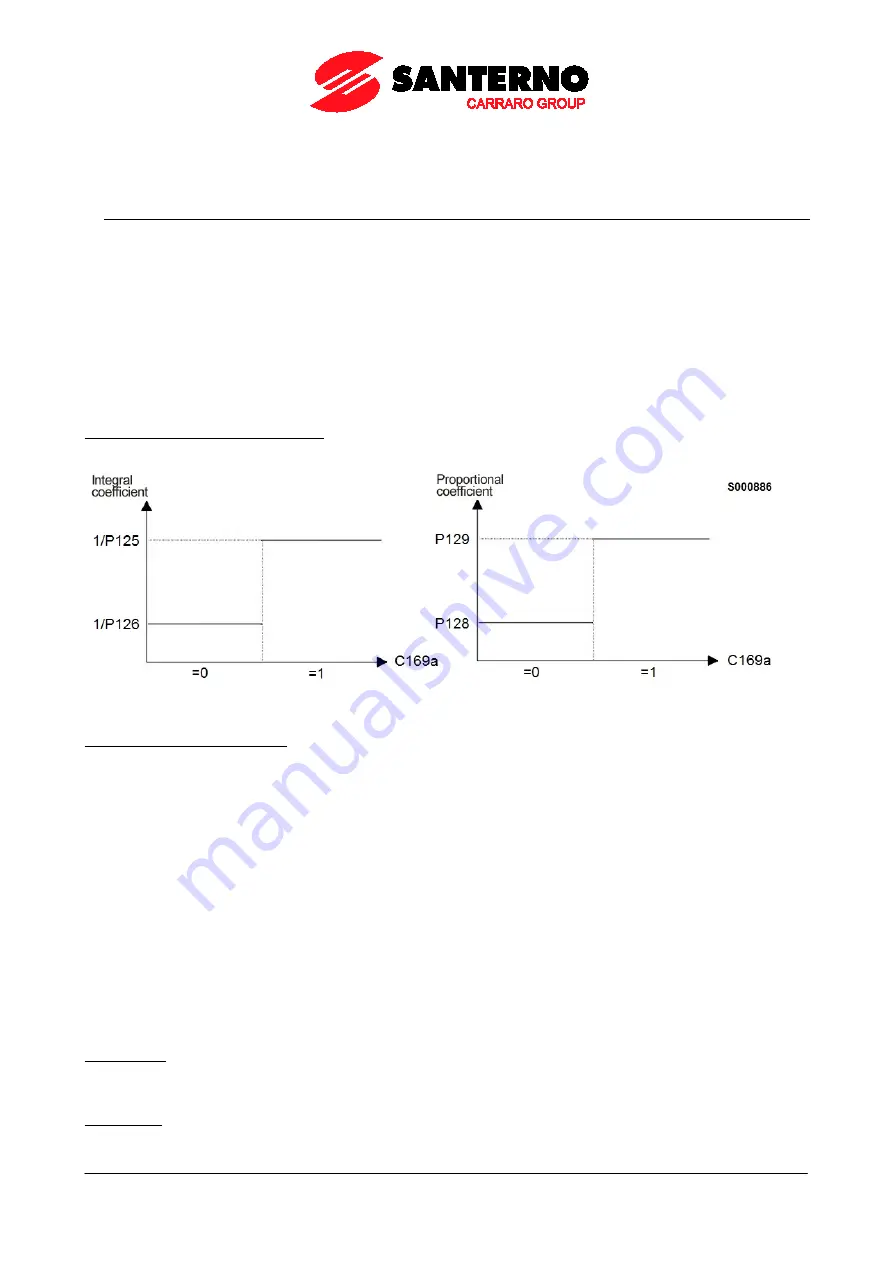
PROGRAMMING GUIDE
SINUS PENTA
135
/
486
19. SPEED
LOOP
AND
CURRENT
BALANCING
MENU
19.1.
Overview
The SPEED LOOP AND CURRENT BALANCING MENU, for VTC and FOC controls, allows setting the parameter
values of the speed regulators for the three connected motors and to manually adjust the motor current balancing (see
parameter
P152
).
The speed regulator for each motor has two parameterization functions: two integral terms and two proportional terms.
As per factory settings, only parameters
P126
(Maximum Integral Time) and
P128
(Minimum Integral Time) are used.
Adopting the remaining two parameters
P125
(Minimum Integral Time) and
P129
(Maximum Proportional Constant) is
based on two possible control logics:
•
Status of the digital input set in
C169a
(FOC control only);
•
Logics based on the adjustment error.
Status of the digital input set in
C169a
: if the input is low, parameters
P126/P128
will be active; otherwise (high logic
level) parameters
P125/P129
will be active.
Figure 14: Example of dual parameterization activated by a digital input
Logic based on adjustment error: This second logic enables a regulator’s response dynamically related to the speed
error; in that way, the speed regulator will be more reactive to big errors and less sensitive to small errors. To activate
this control logics, speed error thresholds
P130
and
P131
(expressed as a percentage of the rated speed) are to be set
to different values.
The response of the speed regulator can be dynamically linked with the speed error; in this way, the speed regulator will
be more sensitive to remarkable speed errors and less sensitive to negligible speed errors.
Factory setting: because two identical error thresholds are set, only two parameters are used:
P126
(maximum integral
time)
and
P128
(minimum proportional constant).
The setup of min. integral time and max. proportional constant is enabled provided that two different error thresholds are
used.
Example:
P125
100
[ms]
Minimum integral time
P126
500
[ms]
Maximum integral time
P128
10.00
Minimum proportional constant
P129
25.00
Maximum proportional constant
P130
2
[%]
Minimum error threshold
P131
20
[%]
Maximum error threshold
Error ≤
P130
For speed errors lower than or equal to 2% of the motor rated speed, the speed regulator adopts parameters
P126
and
P128
.
Error ≥
P131
If the speed error is higher than or equal to 20% of the rated motor speed, the speed regulator adopts parameters
P125
and
P129
.
Содержание PENTA MARINE
Страница 173: ...PROGRAMMING GUIDE SINUS PENTA 173 486 Figure 27 Response to the step based on the value of Kp when Ti is kept constant...
Страница 196: ...SINUS PENTA PROGRAMMING GUIDE 196 486 Figure 34 ANALOG Mode Figure 35 DOUBLE DIGITAL Mode...
Страница 197: ...PROGRAMMING GUIDE SINUS PENTA 197 486 Figure 36 General structure of the parameterization of a digital output...