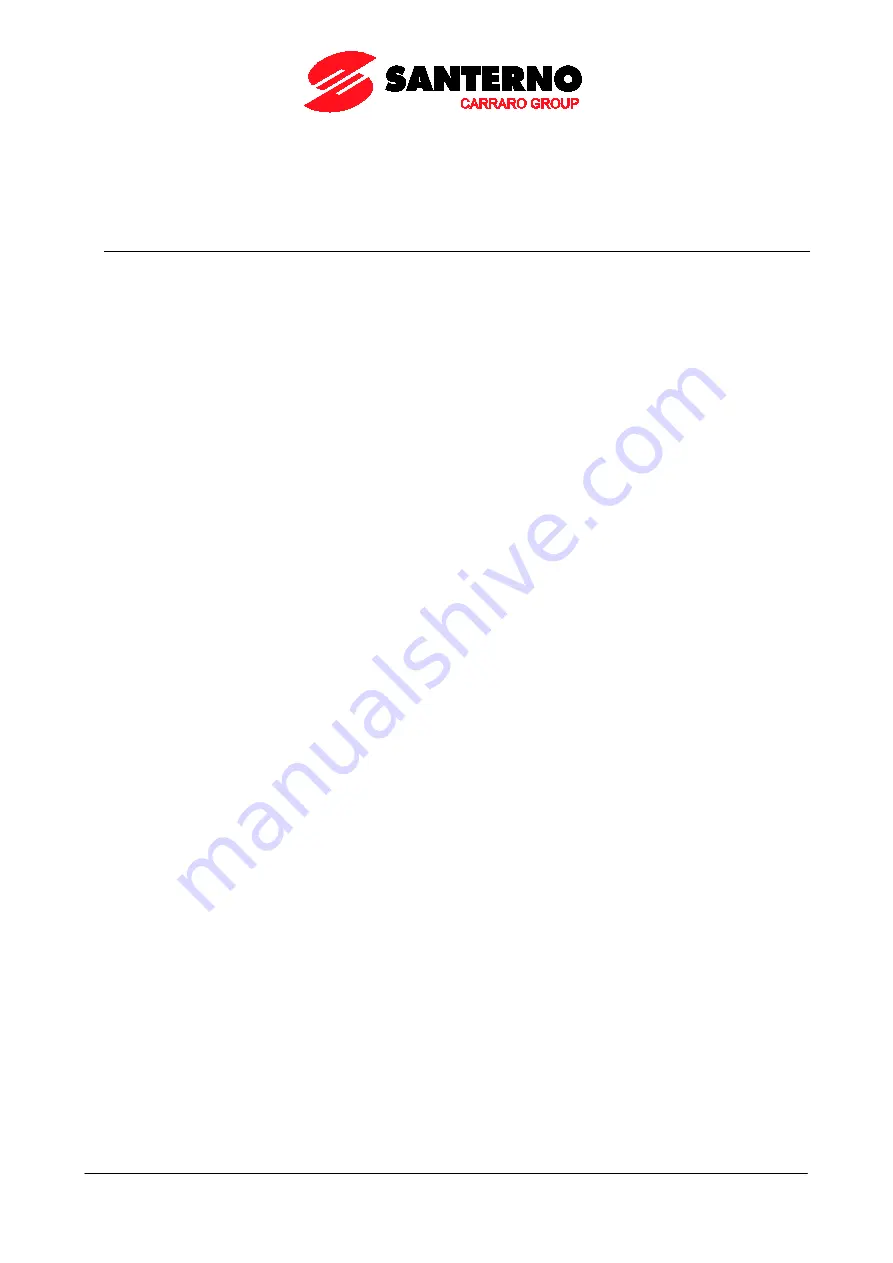
SINUS PENTA
PROGRAMMING GUIDE
40
/
486
7. FIRST
STARTUP
For the signal wiring and power wiring, please refer to the Sinus Penta’s
Parameter programming is detailed in the START-UP MENU.
7.1. “IFD” Control Algorithm
SINUS PENTA drives are factory set with the IFD (
C010
) control algorithm for the first startup of the equipment. The
default functions of the drive terminals are given in the table below. For more details, please refer to the Sinus Penta’s
1) Wiring:
Follow the instructions stated in the “Caution Statements” and “Installation” sections
(Installation Guide).
2) Power on:
Power on the drive and do not close the link to the
ENABLE-A
and
ENABLE-B
inputs to prevent the motor from running. Check if the display/keypad turns on.
3) Parameter setting:
The equipment startup is made easier by the START-UP MENU, which is a wizard
for the set-up of the main motor control parameters.
From the START-UP MENU, set the following:
1. The real
power supply voltage in
C008
. It is possible to select the rated
mains voltage range or the power supply from a DC-bus stabilized by a
Regenerative Penta;
2. The motor ratings by way of:
•
C015
(fmot1) rated frequency
•
C016
(rpmnom1) rated rpm
•
C017
(Pmot1) rated power
•
C018
(Imot1) rated current
•
C019
(Vmot1) rated voltage
•
C029
(Speedmax1) max. allowable speed.
The motor V/f pattern may be programmed in
C013
. For loads with quadratic torque
in respect to the rpm (centrifugal pumps, fans, etc.), set
C034
(preboost1) to 0%.
4) Autotune
(motor
stopped):
In case of IFD motor control when slip compensation is inactive (
C039
=0%) no
autotune is required. On the other hand, when slip compensation is active, it is
recommended to compute stator resistance
C022
.
The steps to take to perform motor autotune are the following:
With the
ENABLE-A
and
ENABLE-B
commands open, access the AUTOTUNE
MENU and set
I073
= [1: Motor Tune] and
I074
= [0: All Ctrl no rotation]. Use the
ESC
key to accept changes.
Close the
ENABLE-A
and
ENABLE-B
commands and wait until tune is complete
(Warning “
W32
Open Enable” is displayed). The drive has computed and saved the
values for
C022
(stator resistance).
If alarm “
A097
Motor Wires KO” trips, check the motor wiring. If alarm “
A065
Autotune KO” trips, this means that the
ENABLE
command has opened before
autotune was complete. In this case, reset the drive by sending a command from
terminal MDI3, or press the
RESET
key in the display/keypad and perform the
autotune procedure again.
5) Overload:
Set parameters
C043
,
C044
and
C045
as the maximum desired overload current.
6) Startup:
Activate the
ENABLE-A
input (terminal 15),
ENABLE-B
input (terminal S) and the
START
input (terminal 14) and send a speed reference: the
RUN
LED and
REF
LEDs will come on and the motor will start running. Make sure that the motor is
rotating in the correct direction. If not, set parameter
C014
(Phase Rotation) to
[1:Yes], or open the
ENABLE-A,
ENABLE-B
and
START
inputs, remove voltage
from the drive and, after waiting at least 20 minutes, swap two of the motor phases.
Содержание PENTA MARINE
Страница 173: ...PROGRAMMING GUIDE SINUS PENTA 173 486 Figure 27 Response to the step based on the value of Kp when Ti is kept constant...
Страница 196: ...SINUS PENTA PROGRAMMING GUIDE 196 486 Figure 34 ANALOG Mode Figure 35 DOUBLE DIGITAL Mode...
Страница 197: ...PROGRAMMING GUIDE SINUS PENTA 197 486 Figure 36 General structure of the parameterization of a digital output...