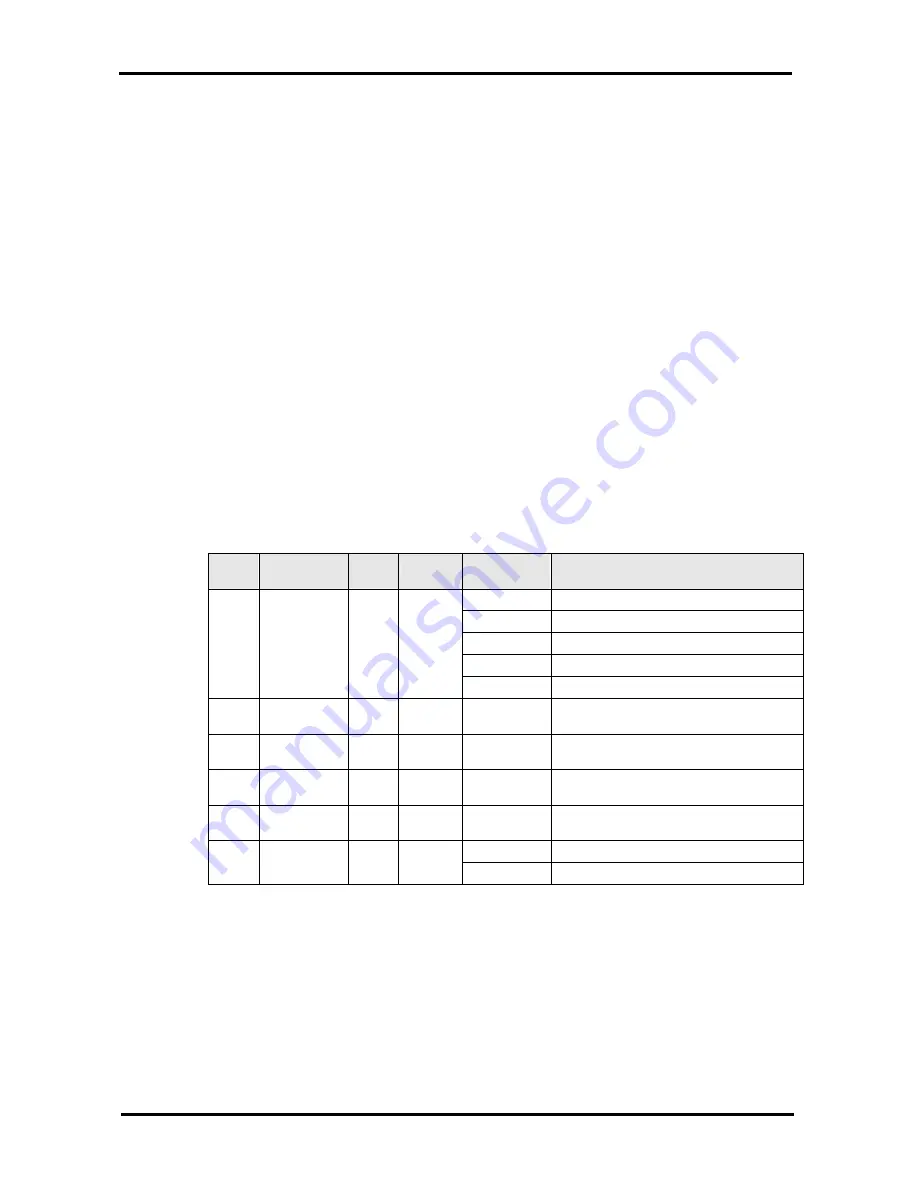
N700 Operating Instructions and Parts Manual
11. Explanation of C-Group
125
11.3
Torque limit function (TL, TRQ1, TRQ2)
(1) This function limits motor output torque when sensorless vector control(5), sensored vector
control (6), 0Hz domain sensored vector control(7) in vector control with sensor are selected.
(2) In torque limit function method, the following three are selected in C006 torque limit selection
screen.
①
4 quadrant individual setting mode :
This mode sets torque limit in 4 quadrant, forward driving and regenerating, reverse
driving and regenerating, to digital operator setting code C007-C010 individually.
②
Terminal changing mode :
By combination of torque limit changing terminals 1and2, this mode changes and uses
torque limit 1-4 set by in digital operator setting. Selected torque limit range is valid in
every driving condition.
③
Analog input mode :
This mode sets torque limit value by voltage given to 02 terminal of control Terminal. 0-
10V is equal to torque limit value 0-200%. Selected torque limit value is valid in every
driving condition. (If the code F010 is set as 01, this function do not work and torque limits
change to 200%)
④
Option 1, Option 2 : Reserved
Code Function name
Initial
value
Unit
Setting range
Contents
0 Individual
setting
1 Terminal
2
Analog input :
3 OPT1
(Reserved)
C006
Torque limit
selection
0 -
4 OPT2
(Reserved)
C007 Torque limit 1
200
%
0~200
In the case of 4 upper limits individuation
setting, forward driving
C008 Torque limit 2
200
%
0~200
In the case of 4 upper limits individuation
setting , reverse restoration.
C009 Torque limit 3
200
%
0~200
In the case of 4 upper limits individuation
reverse driving
C010 Torque limit 4
200
%
0~200
In the case of 4 upper limits individuation
setting, forward restoration.
0 Invalid
C011
Torque LAD
Stop selection
0 -
1 Valid
Table 11- 5 Torque limit function (TL, TRQ1, TRQ2)
(3) When torque control valid / invalid function (TL) is set to intelligent input terminal, torque limit
function is valid only during the signal turning ON. During OFF, torque limit setting is invalid,
torque control value is 200% of maximum. And when torque control valid / invalid function
(TL) is not set, torque limit function is always valid.
(4) Torque limit value in this function is 200% of maximum current which inverter can output.
Therefore, output torque may change in accordance with motors combined. Make sure that
the absolute value of torque does not appeared.