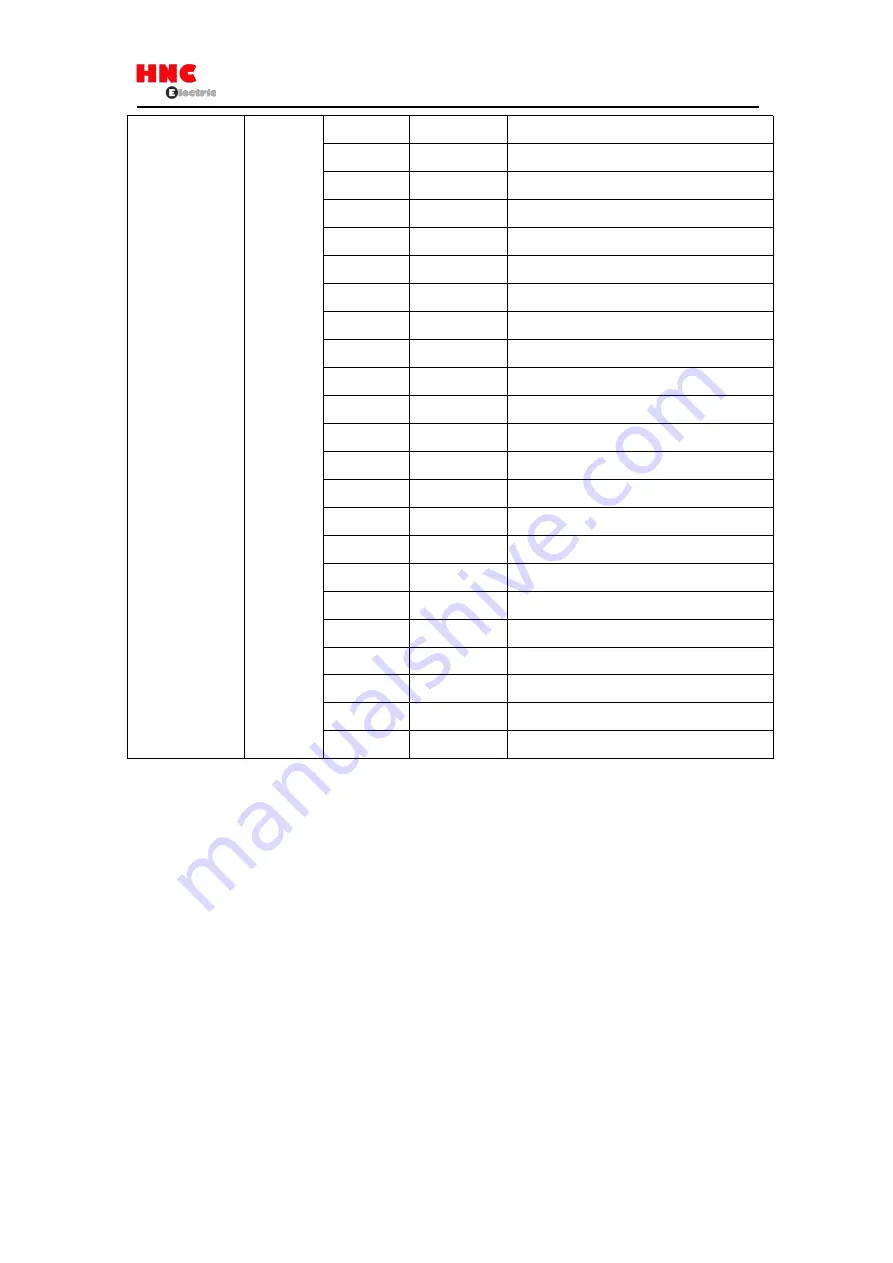
104
28
-
Reserved
29
-
Reserved
30
-
Reserved
31
-
Reserved
32
A SPEED
Analog speed command input
33
A_GND
Analog speed command input ground
34
-
Reserved
35
-
Reserved
36
OUT_A
Encoder A phase output
37
/OUT_A
Encoder /A phase output
38
OUT_B
Encoder B phase output
39
/OUT_B
Encoder /B phase output
40
OUT_Z
Encoder Z phase output
41
/OUT_Z
Encoder /Z phase output
42
SG
Signal ground
43
485
EIA-485 communication data
44
/485
EIA-485 communication /data
45
SG
Signal ground
46
NC2
Reserved(Disconnected)
47
-
Reserved
48
-
Reserved
49
-
Reserved
50
-
Reserved
Содержание SV-E3 Series
Страница 21: ...21 ...
Страница 25: ...25 ...
Страница 27: ...27 ...
Страница 28: ...28 ...
Страница 29: ...29 ...
Страница 30: ...30 3 5 Dimensions of servo drive Same dimensions for SV E3 ...
Страница 41: ...41 Figure 5 3 1 ...