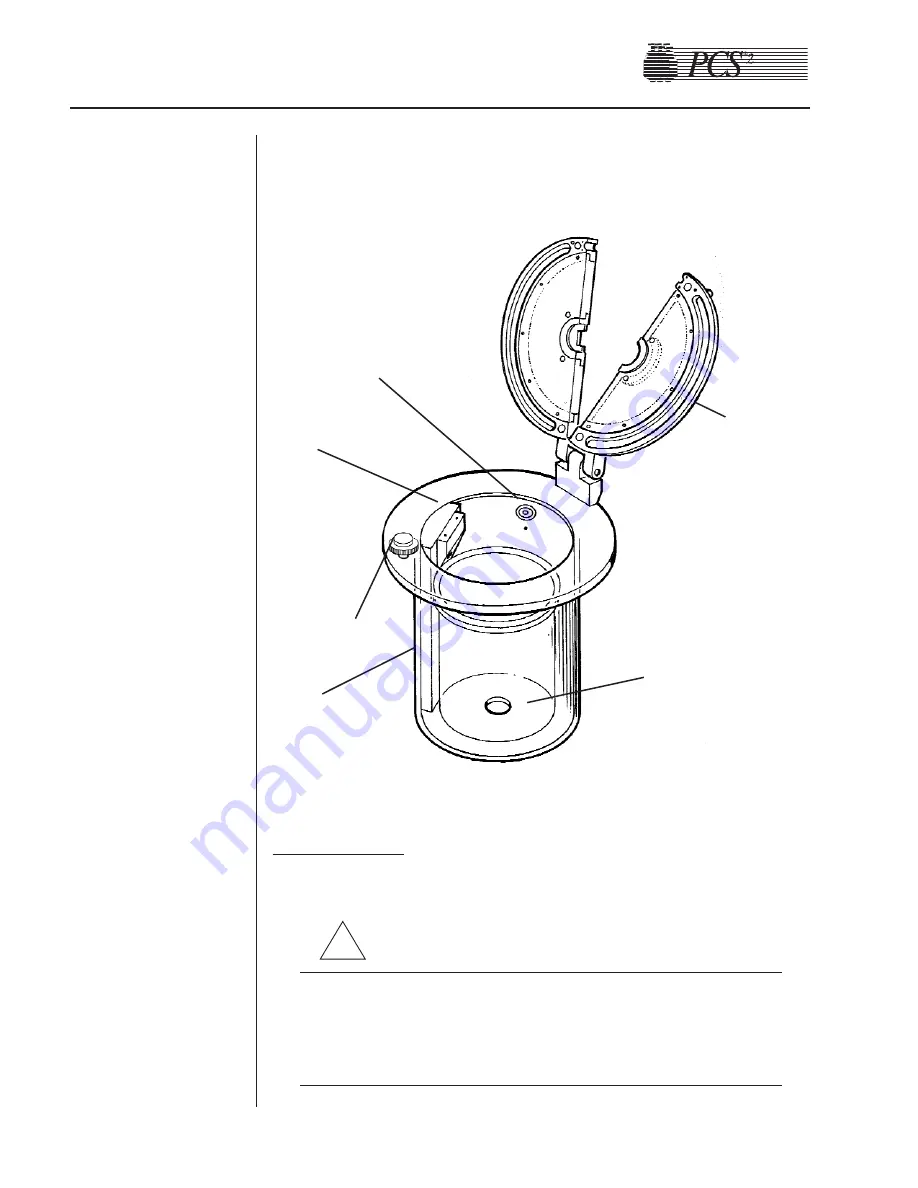
1. Gently wash the groove of the line sensor with lint-free gauze or
toweling moistened with distilled water.
2. Dry the groove with lint-free gauze or toweling.
Figure 8-1, Centrifuge Well Components
Centrifuge Well
Figure 8-1 is a view of the centrifuge well with components labeled. Refer
to this drawing to understand the cleaning instructions.
Warning!
Haemonetics recommends the use of rubber or vinyl gloves to
avoid contact with any spilled blood. When handling or discarding
potentially contaminated waste, comply with the policies and
procedures dictated by the Center’s Infection Control Plan, as
legally required by OSHA’s Bloodborne Pathogens Standard.
8-4
PCS2 Service Manual
!
Cover
Centrifuge
Chuck
Well
Centrifuge
Cover Latch
Bowl
Optics
Fluid
Sensor
!
Содержание PCS 2
Страница 1: ...HAEMONETICS PCS 2 Service and Maintenance Manual...
Страница 79: ...Notes 6 4 PCS2 Service Manual...
Страница 112: ...7 2 PCS2 Service Manual...