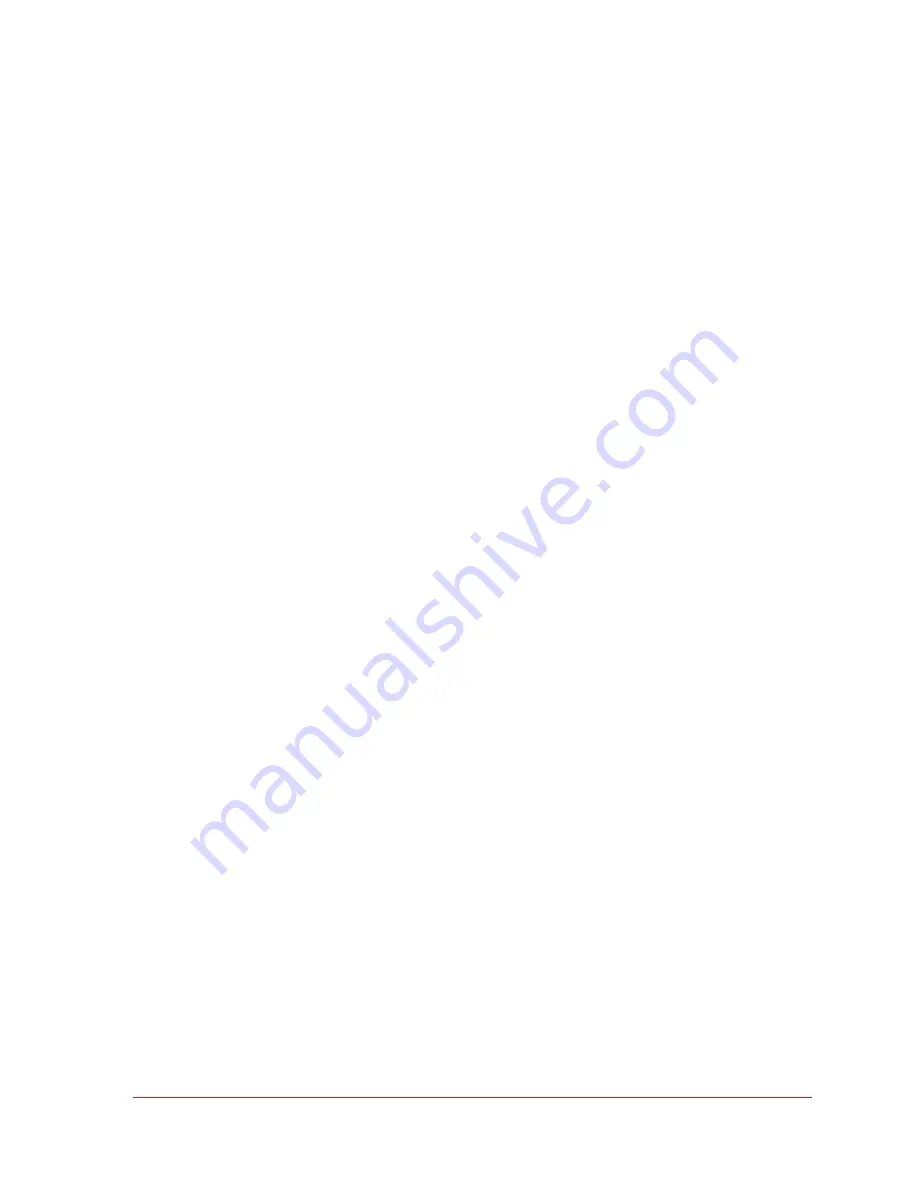
Operator’s Manual: ThermoJet
Chapter 7: System Operation
© SP Industries, Inc.
200-31974-999 Rev. 009
55
Shutdown Procedure
1. Terminate any test programs and raise the head assembly.
2. Return to the Manual operation screen and ensure that all temperature Set buttons are inactive,
system is in IDLE mode and under nozzle control.
3. Slowly rotate the holding arm so that the air delivery assembly directs the air flow away from
personnel, the test fixture, and any critical components.
4. Press the “Off” button located in the top left corner of the Manual operation screen.
5. The Shutdown Warning screen will appear and require a prompt to continue. Press “Yes” to
continue the shutdown.
6. The Shutdown Screen will appear and the ThermoJet will initiate its Shutdown routine, which
includes an automatic defrost cycle. The defrost cycle is implemented to ensure all moisture is
removed from the internal components of the refrigeration system. This process prevents
moisture from being discharged from the nozzle at system start up and reduces the possibility of
blowing moisture onto a component. The refrigeration system will shut down but air will continue
to flow through the system for two minutes before stopping.
This completes the Shutdown Procedure for the ThermoJet. The System Controller will
automatically continue the Shutdown routine until the system heat exchanger has reached a
temperature of about 40°C. At that point the System Controller will shut everything off except DC
voltage into the PLC and touch screen. The screen will go dark but will remain active. Touching
the blank screen will bring up the Restart screen.
Common Operating Methods
Control of the ThermoJet can be separated into three distinct methods:
•
Manual
•
Program
•
Computer
Manual Operation
In the Manual Mode, the operator works primarily with the three preset temperature setpoints, Set
1, Set 2 and Set 3 (Fig. 40). Pressing these buttons instructs the system to switch the control
setpoint to the respective temperatures in a stepwise manner (no ramp time). This operating
method is useful when repeating step changes between a few target temperatures. There is also
a manual mode ramp rate feature which can be selected. R&D work, troubleshooting, and
engineering design verification are the most common applications for this operating mode.
Two temperatures may be displayed simultaneously, one for the air temperature and the other for
the DUT (Device Under Test) temperature. The nozzle temperature is always displayed, but the
DUT temperature is only displayed when in the DUT control mode. When under Nozzle control,
the nozzle temperature is controlled via a simple PID loop. The nozzle temperature (process
variable) is compared to the user define setpoints and the controller output acts directly on the
heater. When under DUT control, a cascade control loop is used. Here, the DUT temperature
becomes the process variable and it is compared to the user defined setpoint. The output of the
“outer” DUT control loop becomes the setpoint for the fast acting “inner” nozzle control loop. The
Nozzle control mode is the default mode.
When one of the “Set” buttons is pressed, the following occurs:
•
Its indication changes to “Active” to signify the system is controlling at the associated
temperature.
•
The Status display changes to indicate the status of the system as it transitions to the set
temperature.
•
The head will lower to the down position (if not already down).
•
The airflow will increase to the set flow rate (if not already there).