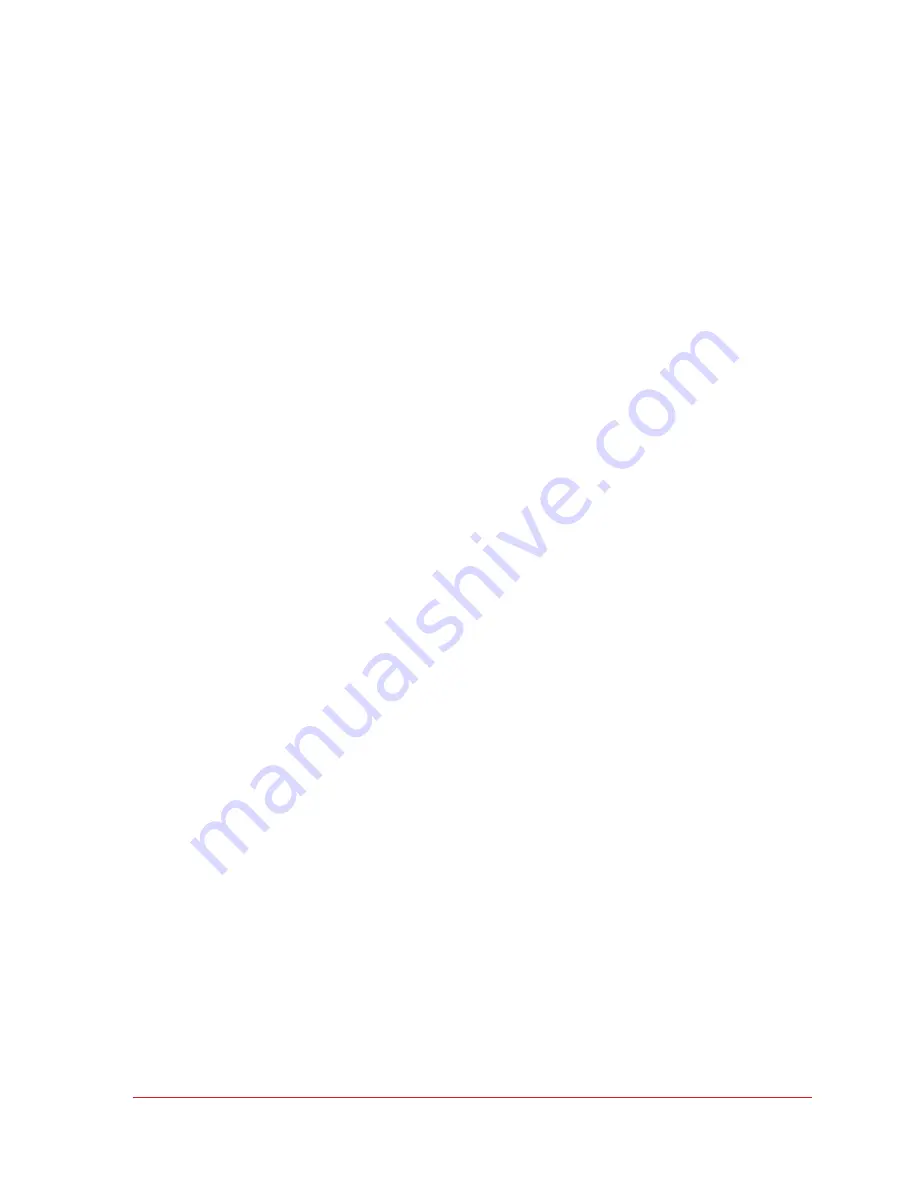
Operator’s Manual: ThermoJet
Chapter 5: Display Screens
© SP Industries, Inc.
200-31974-999 Rev. 009
33
When the START button is pressed, the system will begin calculating the upper limit temperature.
A cancellation button will appear on the auto-tuning screen. The system will automatically return
to the manual screen when the cancellation button is pressed.
Once the system finishes calculating the upper limit, it will then calculate the lower limit
temperature. When the lower limit is finished, the system will enter the auto-tuning sequence.
When the auto-tuning sequence is completed, the system will return to IDLE mode under DUT
control. The individual Proportional (P), Integral (I), and Derivative (D) parameters are displayed
on the auto-tuning screen. For added flexibility, these values can be fine-tuned by manually
entering a value to provide for more aggressive or conservative temperature control than is
calculated by the Auto-tuning feature. Following is a brief description of the P, I, and D values,
and how they effect the speed and stability of the DUT temperature control.
Proportioning Band
– Enter a value between 0.01 and 99.99, larger values for smaller DUT
thermal masses. Proportional band makes the controller output proportional to the difference
between set temperature and actual temperature.
(controller output) = (set temp./actual temp.) * 100/(proportional band)
Integral Time
– Enter a value between 0.01 and 99.99, smaller values for smaller DUT thermal
masses. An Integral Time value causes the controller output to be proportional to the amount of
time an error, (set temp./actual temp.), is present. Integral action reduces and/or eliminates offset
and gives the controller a large gain at low frequencies that results in eliminating offset and
reducing load disturbances.
(controller output) = (1/integral) (Integral of) e(t) d(t)
Derivative Time
– Enter a value between 0.01 and 99.99, smaller values for smaller DUT
thermal masses. Derivative action causes the controller output to be proportional to the rate of
change of error, (set temp./actual temp.). It takes action to inhibit more rapid changes of the
measurement than proportional action. When a load or set-point change occurs, the derivative
action causes the controller gain to move in the "wrong" direction when the measurement
approaches the set-point. Derivative action can stabilize loops and is often used to minimize
overshoot. The controller output is calculated by the rate of change of the measurement with
time.
d measurement
(controller output) = Derivative -----------------
d time