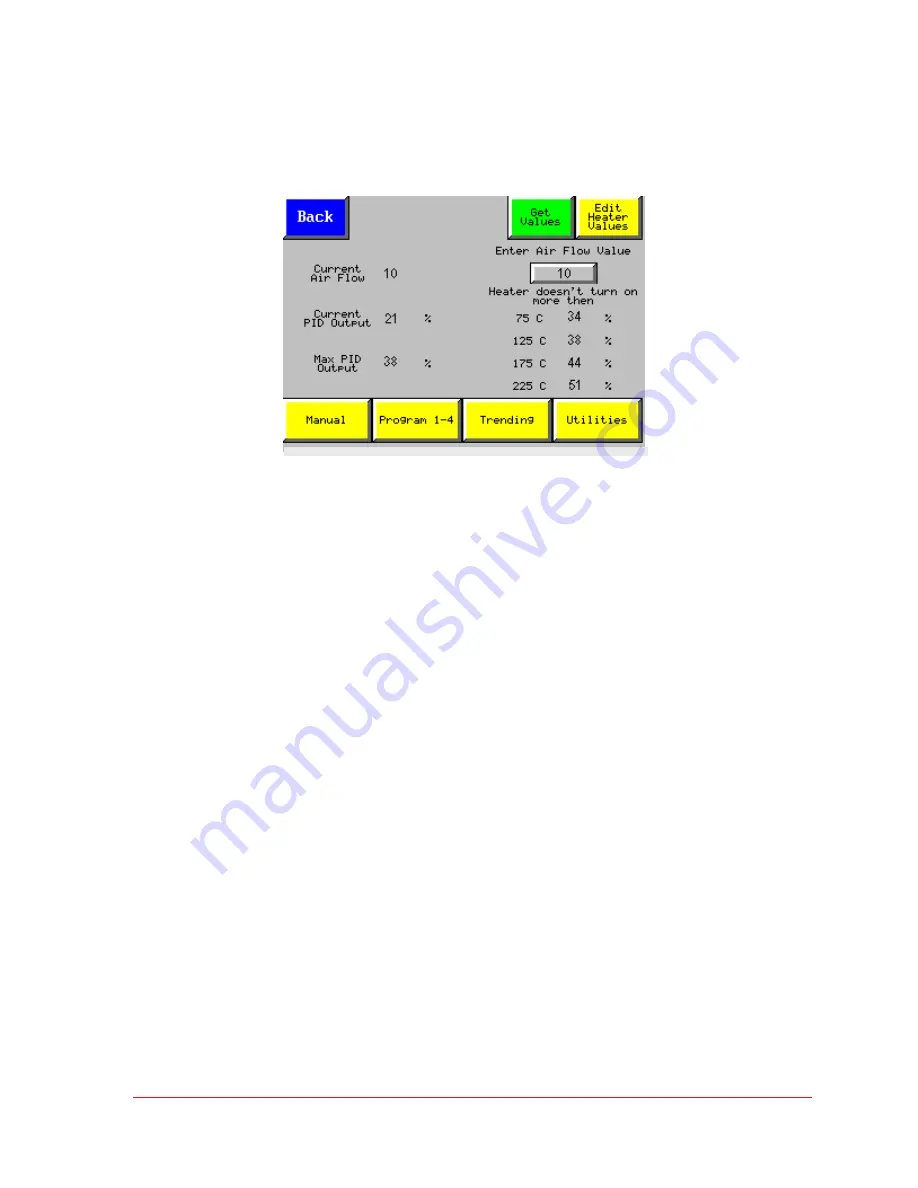
Operator’s Manual: ThermoJet
Chapter 5: Display Screens
© SP Industries, Inc.
200-31974-999 Rev. 009
39
From the Heater Output Values Screen you can also go to the Edit Heater Output Values Screen.
Figure 24 – Heater Output Values Screen
Back –
returns to the Setup screen
Current Air Flow -
indicates the systems current airflow, this may differ from the value in the
“Enter Air Flow Value” field.
Current PID Output -
indicates the current heater output value.
Max PID Output -
indicates corresponds to the “Max Air Temp” which is located and set on the
Auto-tuning screen.
Get Values Button –
will display the heater values for the air flow value which is in the “Enter Air
Flow Value” field, this may differ from the systems “Current Air Flow”
Edit Heater Values –
Brings you to the Edit Heater Values Screen.
Enter Air Flow Value –
the value entered to this field will be the values which are displayed
when the “Get Values” button is pressed.
When the “Get Values” button is pressed the heater values will be displayed as a percentage.
The percentage will appear next to the appropriate temperature (75, 125, 175, 225).
How to use this screen:
•
Enter the Air Flow value which you would like to see
•
Press the “Get Values” Button.
•
From the example above, you will see that the Heater out put values is 34% at 75ºC….. 51%
at 225 ºC
NOTE: T
he “Max PID Value” is 38% which indicates that the “Max Air Temp” must be set to
125ºC.
If a value is chosen in between 75, 125, 175, 225, the software will use the equation (y=mx+b) to
calculate the appropriate “Max PID Output”. See example 2 following.
Heater Output Values Screen