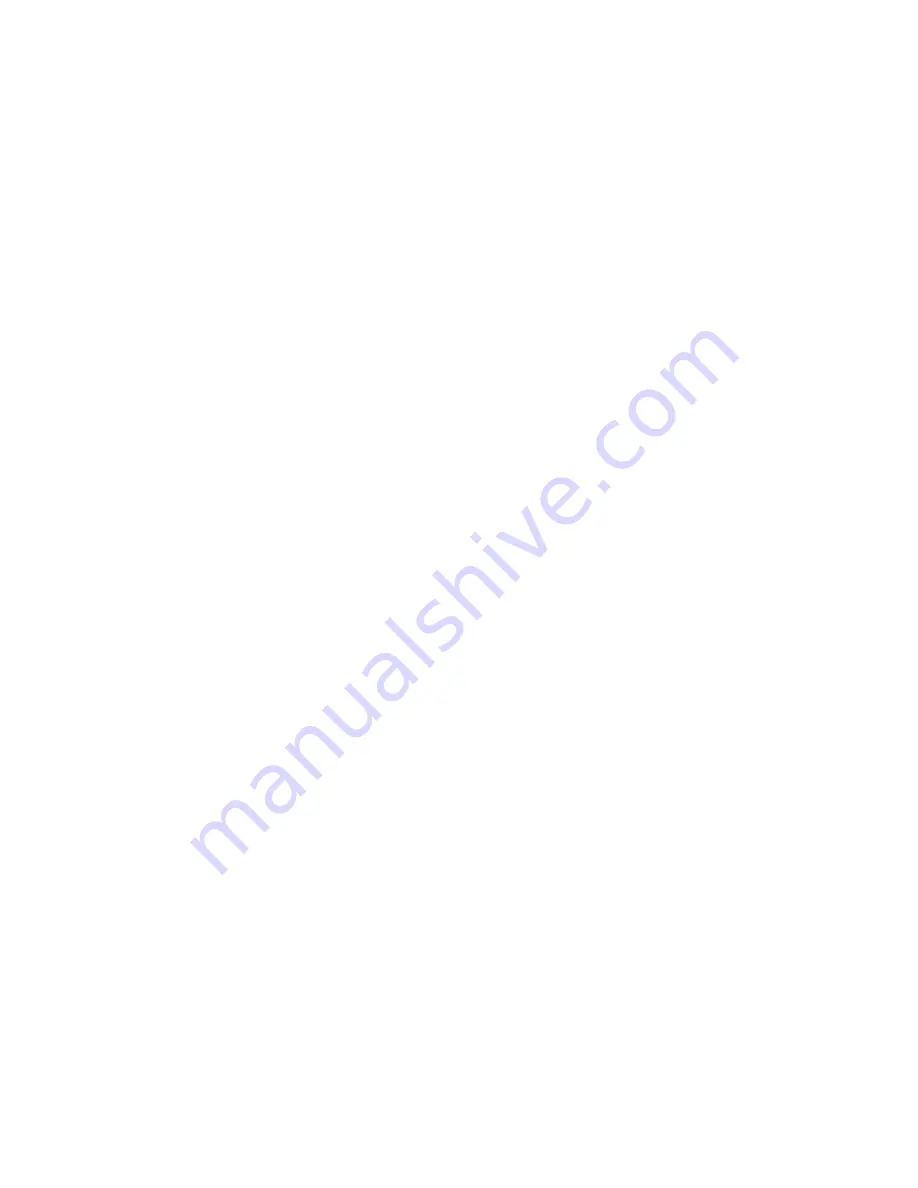
Appendix C—Optional Communication Cards
Power Xpert C445 Global Motor Management Relay
MN042003EN—January 2019
www.eaton.com
295
Fieldbus Motor Control Word
This control word applies to all Cyclic Modules with output
data except the Motor Management Profile shown above.
The Fieldbus Motor Control word is defined as follows:
Bit 0: Run1
Bit 1: Run2
Bit 2: Switch To Remote
Bit 3: Reset Fault
Bit 4: Reserved
Bit 5: Test Trip
Bits 6-15: Reserved
Bit 2, the Switch To Remote bit is only active when the
“Allow Remote Control Switch” parameter is Enabled.
This parameter can be found in the Operation Mode
category, in the Advanced parameters. This feature only
works with the Fieldbus Motor Control word.
The Motor Control bits cannot be assigned if the Fieldbus
Motor Control word is assigned.
If the Motor Control bits are assigned, then the Fieldbus
Motor Control word should not be assigned. In addition,
when the Motor Control bits are assigned, the first output
word to the C445 is a control word based on the bit
assignments. Subsequent word assignments such as
assigning the System Services or digital or analog output
words actually begin with the second output word sent to
the C445.
Module 2
: Cyclic Module 2
This profile includes one input byte. Each bit is
selectable via the C445 GSD file installed in the
PROFIBUS master’s configuration software tool.
Module 3
: Cyclic Module 3
This profile includes 2 input bytes. Each bit is
selectable via the C445 GSD file installed in the
PROFIBUS master’s configuration software tool.
Module 4
: Cyclic Module 4
This profile includes 1 output byte. The output data is
under the “Slave” module, after the Configuration
Parameters.
Module 5
: Cyclic Module 5
This profile includes 2 output bytes. The output data is
under the “Slave” module, after the Configuration
Parameters.
Module 6
: Cyclic Module 6
This profile includes 2 input bytes and 2 output bytes.
The input data is selectable under the cyclic module in
the PROFIBUS master’s programming software. The
output data is under the “Slave” module, after the
Configuration Parameters.
Module 7
: Cyclic Module 7
This profile includes 8 input bytes and 4 output bytes.
The input data is selectable under the cyclic module in
the PROFIBUS master’s programming software. The
output data is under the “Slave” module, after the
Configuration Parameters.
Module 8
: Cyclic Module 8
This profile includes total 6 output bytes and 10 input
bytes. The input data is selectable under the cyclic
module in the PROFIBUS master’s programming
software. The output data is under the “Slave”
module, after the Configuration Parameters.
Module 9
: Cyclic Module 9
This profile includes 2 input bytes. 1 word parameter
may be selected for the input data. The input data is
selectable under the module in the PROFIBUS
master’s programming software.
Module 10
: Cyclic Module 10
This profile includes 4 input bytes. 2 word parameters
may be selected for the input data. The input data is
selectable under the module in the PROFIBUS
master’s programming software.