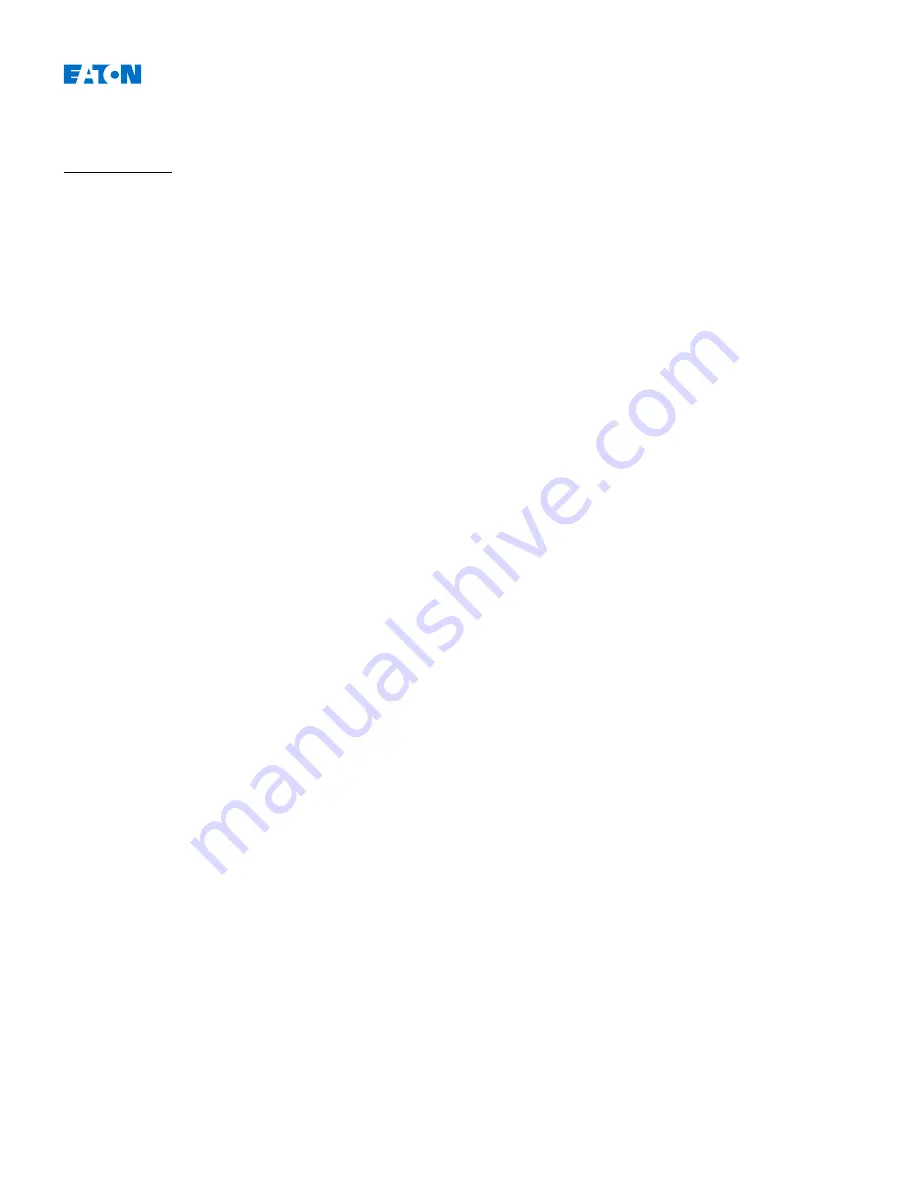
EMR-5000
IM02602012E
Motor Wellness
Available elements:
Motor Diagnosis
Broken Rotor Bar Detection
If there are enough broken rotor bars within a motor, the motor may not be able to develop sufficient accelerating torque
to start. The presence of broken rotor bars precipitates deterioration in other components that can result in the need for
time-consuming and expensive repairs. Replacement of the rotor core in larger motors is costly; therefore, by detecting
broken rotor bars early, such secondary deterioration can be avoided. The rotor can be repaired at a fraction of the
cost of rotor replacement.
After the phase current is sampled, a Fast Fourier Transform (FFT) is performed on the time-domain data to obtain a
frequency spectrum. The location of the frequency components of the current due to broken rotor bars in the frequency
spectrum is given by the formula:
f
sb
= f
1
(1±2s) Hz
Where: f
sb
= frequency components of the current due to broken rotor bars, also known as sidebands; f
1
= power
supply frequency (Hz); s = operating slip (per unit).
In the predictor equations, the ratios between the slip and the fundamental are the main input parameters. Other
parameters are:
•
Motor’s horse power;
•
Number of the rotor bars;
•
Number of pairs of poles'
•
Rotor’s diameter;
•
Rotor’s length; and
•
Load information.
Two algorithms are available and selectable. The first uses a standard FFT, while the second implements an enhanced
FFT, which provides better accuracy by introducing additional signal processing. Both require stable current signal
conditions and near full load current, which are continuously monitored by the algorithm. The algorithm will only
process data when these stable conditions are met.
The stator current is a non-stationary signal whose properties vary with respect to the time variant normal operation
conditions of the motors such as load torque and power operation supply. On the other hand, a rotor bar failure
develops very slowly, therefor it is not necessary to monitor continuously due to the signal unstable conditions.
There are two states which indicate the stage of Broken Bar Detection (BBD). An “alarm” state indicates a broken rotor
bar, while an additional state is indicated if the signal is not good enough to performing a reliable analysis.
Additional values give more detailed information about the signal condition:
“GREEN” (No fault), “YELLOW” (Unclear), or “RED” (broken rotor bar detected) statuses are displayed in real time.
Under a Yellow signal condition, any one of the following signal conditions may be display for clarity:
•
“INVALID_FREQUENCY”; The frequency with +-0.1 of the nominated frequency is required.
•
“INVALID_DATA”: Such as two consecutive zeros.
www.eaton.com
505
Содержание EMR-5000
Страница 62: ...EMR 5000 IM02602012E Ethernet RJ45 Terminal Marking www eaton com 62 1 8 TxD TxD RxD N C N C RxD N C N C...
Страница 271: ...EMR 5000 IM02602012E Fault Recorder Module Signals Signal Description Res record Signal Delete Record www eaton com 271...
Страница 524: ...EMR 5000 IM02602012E Motor Protection Curves Motor Protection Curve Example 1 www eaton com 524...
Страница 525: ...EMR 5000 IM02602012E Motor Protection Curve Example 2 without RTDs www eaton com 525...
Страница 526: ...EMR 5000 IM02602012E Motor Protection Curve Example 3 with RTDs www eaton com 526...
Страница 930: ...EMR 5000 IM02602012E Real Time Clock Running Reserve of the Real Time Clock 1 year min www eaton com 930...