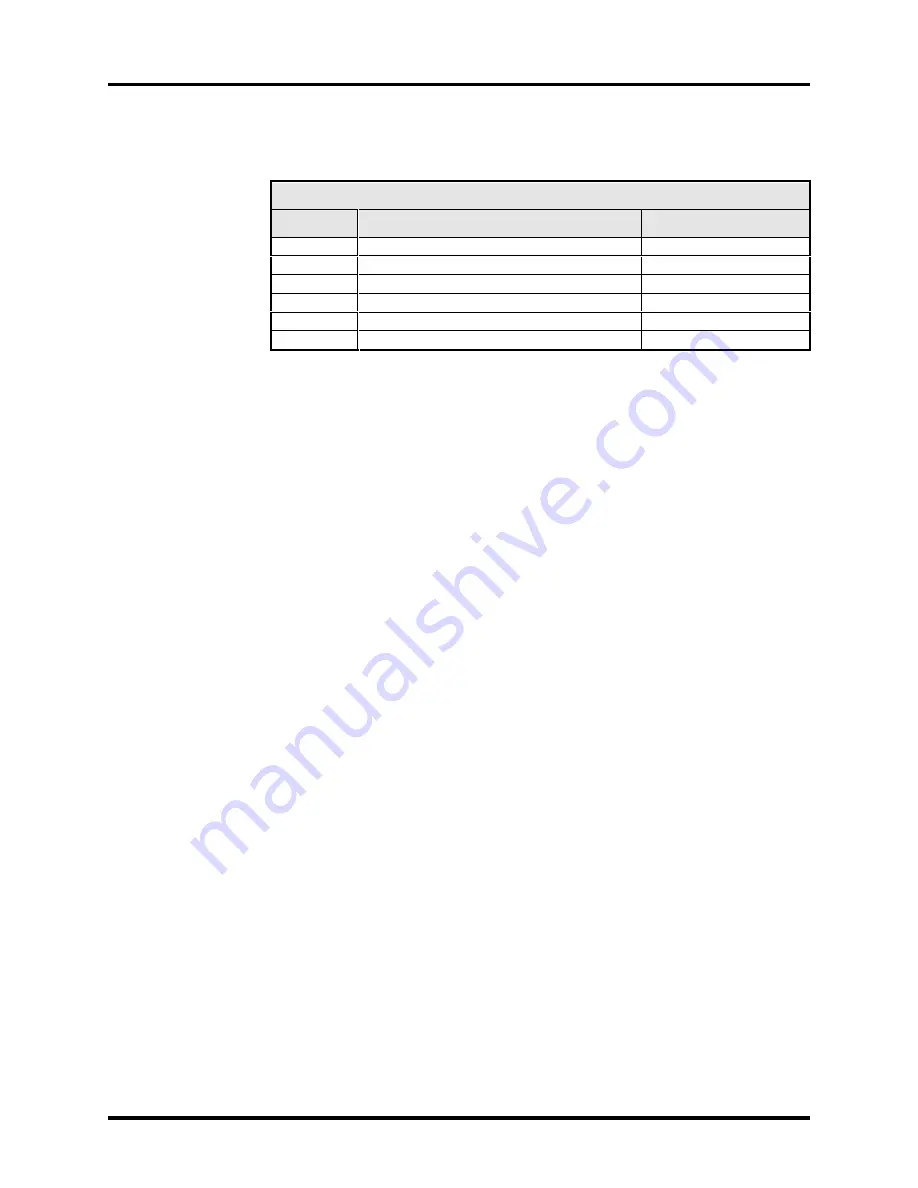
Parameters
U600 User’s Guide
C-108
Aerotech, Inc.
Version 1.4
Table C-18.
Status3 Bit Descriptions (Continued)
Status3 Task Parameter
Bit #
Description
Hexadecimal Value
25
Coord1Plane3
0h2000000
26
Coord2Plane1
0h4000000
27
Coord2Plane2
0h8000000
28
Coord2Plane3
0h10000000
29
Motion No Acceleration
0h20000000
30
Mirroring Mode Active
0h40000000
C.4.142.1.
Motion FeedHold Active
FeedHold has been seen by a synchronous motion statement (motion is either stopped or
decelerating).
C.4.142.2.
Motion Continuous Bit
This bit only has meaning while the controller is executing G0, G1, G2 or G3 motion
commands.
If this bit is OFF, then the controller will decelerate to zero speed at the end of the current
move, and wait until the current motion is done, before declaring the CNC line
completed.
If the bit is ON, then the controller will not decelerate, or will decelerate to a non-zero
speed, at the end of the current move. Additionally, the controller will not wait until
motion is “done”, before continuing to the next CNC command. When there is no
contoured motion executing (MOTIONSTATUS, PROFILING bit is on) the bit is set to
the previous state.
C.4.143.
TaskFault
Task faults are indicated by this task parameter when an error in the execution of a CNC
program occurs. For example, dividing by zero or trying to set a non-existent parameter
from a CNC program causes a task fault. Task Faults stop the CNC program executing on
the task, and also stop motion running on the task (see below for details).
There are many conditions that can cause task faults (for application programmers, any
error prefixed by “AER960RET_” in the file, \U600\Include\AerCode.H can potentially
be returned as a task fault). The user can also trigger a task fault manually, by setting the
TaskFault task parameter non-zero, although only certain values (mentioned above in the
‘AER960RET_’ series constants) will yield a recognizable description.
A special task fault, “physical axis fault” is generated when any axis contained in the
HaltTaskOnAxisFault Task parameter encounters an axis fault. This allows the user to
stop CNC programs in response to axis faults. By default, all axis faults stop all CNC
programs.
When a task fault occurs, the U600 MMI reports an explanation of the task fault in the
lower right-hand corner of the Run or Manual page. The user can view the task fault
description from AerDebug by typing “TK x”, (where x is the task number) and then
Содержание UNIDEX 600 Series
Страница 19: ...Table of Contents U600 User s Guide xviii Aerotech Inc Version 1 4...
Страница 27: ...Preface U600 User s Guide xxvi Aerotech Inc Version 1 4...
Страница 163: ...AerPlot U600 User s Guide 6 6 Aerotech Inc Version 1 4...
Страница 169: ...AerReg U600 User s Guide 8 4 Aerotech Inc Version 1 4...
Страница 177: ...AerPlotIO U600 User s Guide 10 4 Aerotech Inc Version 1 4...
Страница 179: ...Filter U600 User s Guide 11 2 Aerotech Inc Version 1 4...
Страница 219: ...PrmSetup U600 User s Guide 13 2 Aerotech Inc Version 1 4...
Страница 223: ...Glossary of Terms U600 User s Guide A 4 Aerotech Inc Version 1 4...
Страница 353: ......