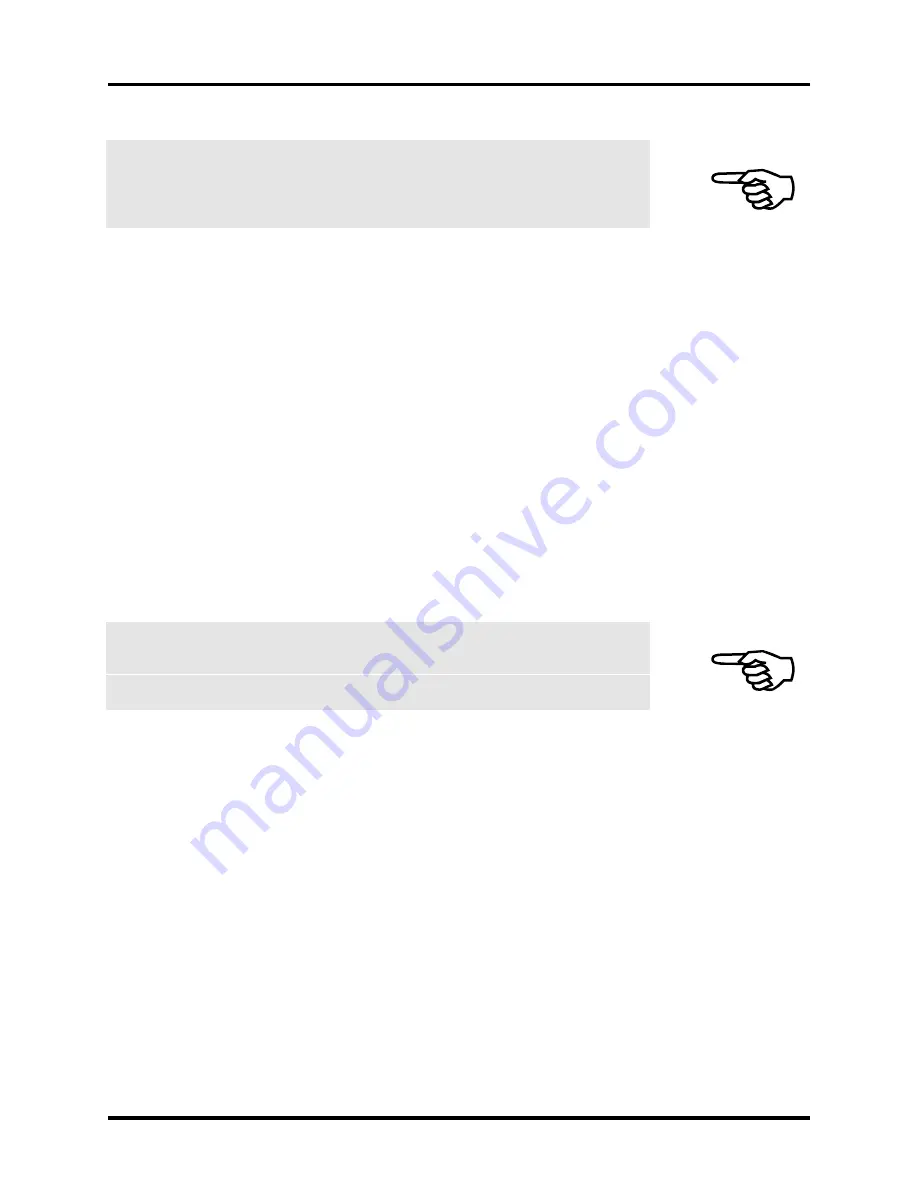
U600 User’s Guide
Parameters
Version 1.4
Aerotech, Inc.
C-47
The error “Parameter too high” can occur when setting this parameter from a CNC
program. The message may not refer to this parameter, but can also refer to the
MaxFeedRateRPM machine parameter, which is “reset” when this parameter is set.
C.3.5.
CntsPerInch
This machine parameter is used by the CNC interface to convert user units into machine
steps, it is specified in counts per inch, even if programming in millimeters (G71). The
sign of this parameter determines motor direction, a positive value indicates that a
positive command will cause motion in the CW motor direction. A negative value
indicates a positive command will cause motion in the CCW motor direction, which will
cause the end of travel limits to appear to be inverted. A negative scale factor will cause a
more positive display position, to encounter the CCW limit and a more negative position
will encounter the CW limit position. This conversion factor is only used for linear axes
(axes whose Type machine parameter is equal to 0).
For brushless linear motors, the value entered here is the number of counts per electrical
cycle of the motor.
Normally this parameter is automatically set by the Parameter Configuration Wizard
during the motor configuration process. This parameter should not be set “on-the-fly”
during program execution is dangerous and not recommended as it will rescale the system
and may cause unusual motion. Use the ScaleFactor parameter if you want to deliberately
rescale the system coordinates during program execution.
The error “Parameter too high” can occur when setting this parameter from a CNC
program. The message may not refer to this parameter, but can also refer to the
MaxFeedRateIPM machine parameter, which is “reset” when this parameter is set.
C.3.6.
ControllingTask
This read only machine parameter indicates which task, if any, controls the axis. The
values 0 through 3 indicate the four tasks respectively and a value of -1 indicates that the
axis is not controlled by any task. An axis is controlled by a task if it is bound or captured
by it.
For example, when the controller is reset, the ControllingTask value for axis 1 is –1. After
task 1 binds axis 1 to X, then the ControllingTask value for axis 1 is 0. If task 3 later
captures axis 1, then the ControllingTask value is 2. After task 3 releases axis 1, the
ControllingTask value reverts back to 0.
Содержание UNIDEX 600 Series
Страница 19: ...Table of Contents U600 User s Guide xviii Aerotech Inc Version 1 4...
Страница 27: ...Preface U600 User s Guide xxvi Aerotech Inc Version 1 4...
Страница 163: ...AerPlot U600 User s Guide 6 6 Aerotech Inc Version 1 4...
Страница 169: ...AerReg U600 User s Guide 8 4 Aerotech Inc Version 1 4...
Страница 177: ...AerPlotIO U600 User s Guide 10 4 Aerotech Inc Version 1 4...
Страница 179: ...Filter U600 User s Guide 11 2 Aerotech Inc Version 1 4...
Страница 219: ...PrmSetup U600 User s Guide 13 2 Aerotech Inc Version 1 4...
Страница 223: ...Glossary of Terms U600 User s Guide A 4 Aerotech Inc Version 1 4...
Страница 353: ......