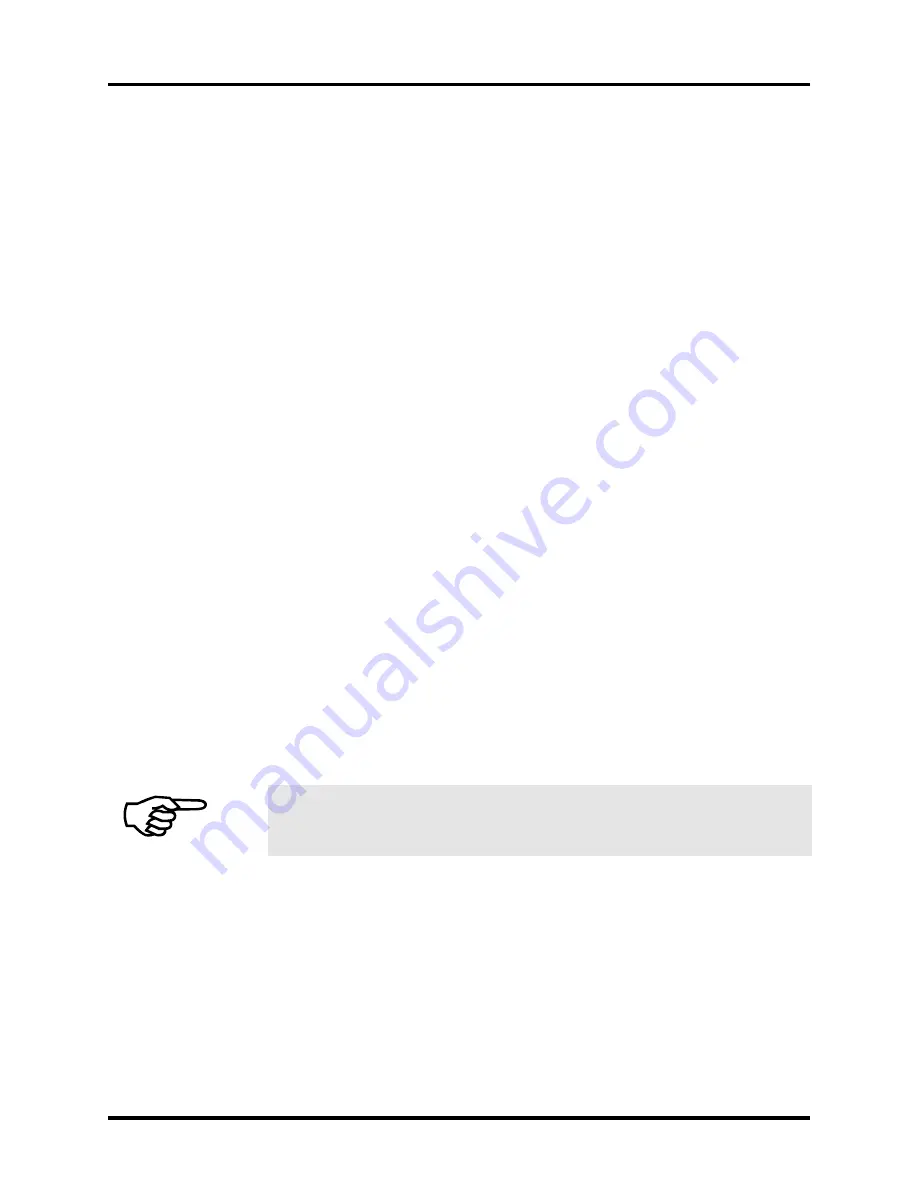
Parameters
U600 User’s Guide
C-86
Aerotech, Inc.
Version 1.4
C.4.81.
MFO
This task parameter sets the Manual Feedrate Override ratio for this task. This ratio can
vary from 0 to infinity, where 1 is 100% of the programmed feedrate and 0% is zero
feedrate. The MSO changes on the MMI600 screens are more restricted. This ratio is
multiplied by the programmed feedrate for all rapid (G0), contoured (G1, G2, G3, G12,
G13) and asynchronous motion (INDEX, MOVETO, etc., except async. home ) in order
to obtain the true feedrate of the move. G0 type moves will not exceed 100% of the
feedrate, as determined by the RapidFeedRateIPM (RapidFeedRateRPM for rotary axes).
This parameter will not affect camming motion (SYNC command). This parameter will
not effect contoured moves (G1, G2, G3, G12, and G13) if the move is in the “Decel
phase” (is currently decelerating to zero speed at the end of the move). This parameter is
sampled at the rate indicated by the AvgPollTimeSec global parameter.
This parameter does not affect homing moves or a spindle velocity. The MSO affects the
spindle. This parameter cannot be changed if the MFOLock task mode bit is active. Also,
if the AnalogMFOInput task parameter is not -1, then the controller over-writes this
parameter with the value obtained from the specified analog input. Additionally, this
parameter reflects only the requested feedrate override, the MaxFeedRateIPM or
MaxFeedRateRPM machine parameters may limit the maximum feedrate. This will not be
reflected in the MFO value.
Normally, the operation of a MFO change during a contoured move will be delayed by a
time interval of (UpdateNumEntries * UpdateTimeSec) seconds. By default, this will be
300 milliseconds.
The acceleration/deceleration during MFO changes is the same as the
acceleration/deceleration followed at the beginning and end of the current move, which is
determined by the motion type, as defined in the Accel/Decel Overview.
C.4.82.
Mode1
This task parameter is a bitmask. Each bit represents a current state of the task. In general,
these states are modes that are toggled by G codes. For example, the current G70 /G71 or
English/Metric programming mode state is indicated by Bit 0. However, a few modes,
such as Auto/Single Step, are not accessible via G codes.
You may view the state of most modal G codes from the MMI600 within the G-Code
Display.
The CNC programmer may also toggle these bits using the Mode1 task parameter. For
example, ‘Mode1 = Mode1 || 0x3’ would be equivalent to ‘G70 G90 ’. However, when
setting the modes directly, you should be sure to ‘’logically or’’ the new bits, so as to not
reset all the other modes.
The user should consult the G code listed in the right column of the table below, for more
information on the modal G code.
Содержание UNIDEX 600 Series
Страница 19: ...Table of Contents U600 User s Guide xviii Aerotech Inc Version 1 4...
Страница 27: ...Preface U600 User s Guide xxvi Aerotech Inc Version 1 4...
Страница 163: ...AerPlot U600 User s Guide 6 6 Aerotech Inc Version 1 4...
Страница 169: ...AerReg U600 User s Guide 8 4 Aerotech Inc Version 1 4...
Страница 177: ...AerPlotIO U600 User s Guide 10 4 Aerotech Inc Version 1 4...
Страница 179: ...Filter U600 User s Guide 11 2 Aerotech Inc Version 1 4...
Страница 219: ...PrmSetup U600 User s Guide 13 2 Aerotech Inc Version 1 4...
Страница 223: ...Glossary of Terms U600 User s Guide A 4 Aerotech Inc Version 1 4...
Страница 353: ......