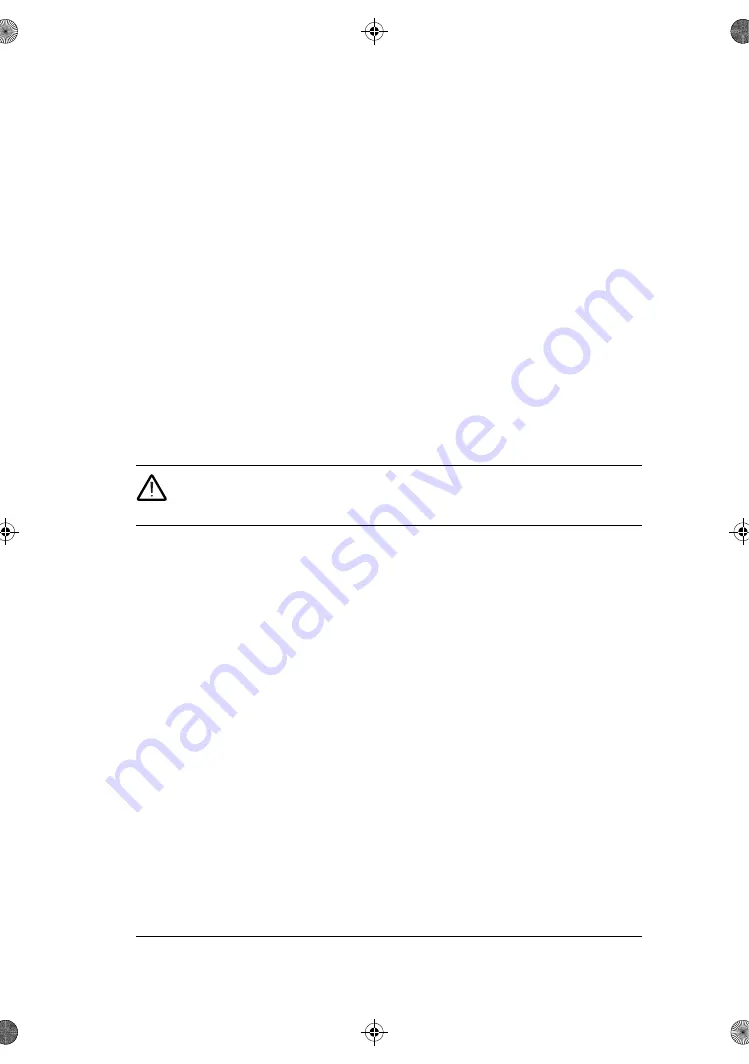
Program features 73
Tracking
In tracking mode, the PID block output is set directly to the value of parameter
).The internal I term of the PID controller is set so that no transient is allowed
to pass on to the output, so when the tracking mode is left, normal process control
operation can be resumed without a significant bump.
Settings and diagnostics
Parameter
(page
).
Parameter groups
(page
) and
(page
Events: -
PID trim function
The PID trim function is used to maintain the set tension either by trimming the drive
main speed reference or torque reference (speed controller output).
WARNING!
Make sure that the drive acceleration and deceleration time is set
to 0 when using the PID trim function. This is required to do quick tension
control by speed correction.
PID trim is implemented as one of the Process PID functions (parameter groups
). Both PID set 1 and PID set 2 can be
used for this functionality.
The trimmed output is calculated from parameter
or
is
used. This is based on the selection in parameter
(for process
PID set 1) or
(for process PID set 2). In most of the use
cases, the value of parameter
or
is set as
PID output
.
PID trim functionality in Variable Frequency Drives (VFD) is used in applications
where tension control of the material is essential. For example, auxiliary drives in
ACS180 FW.book Page 73 Tuesday, March 9, 2021 2:25 PM