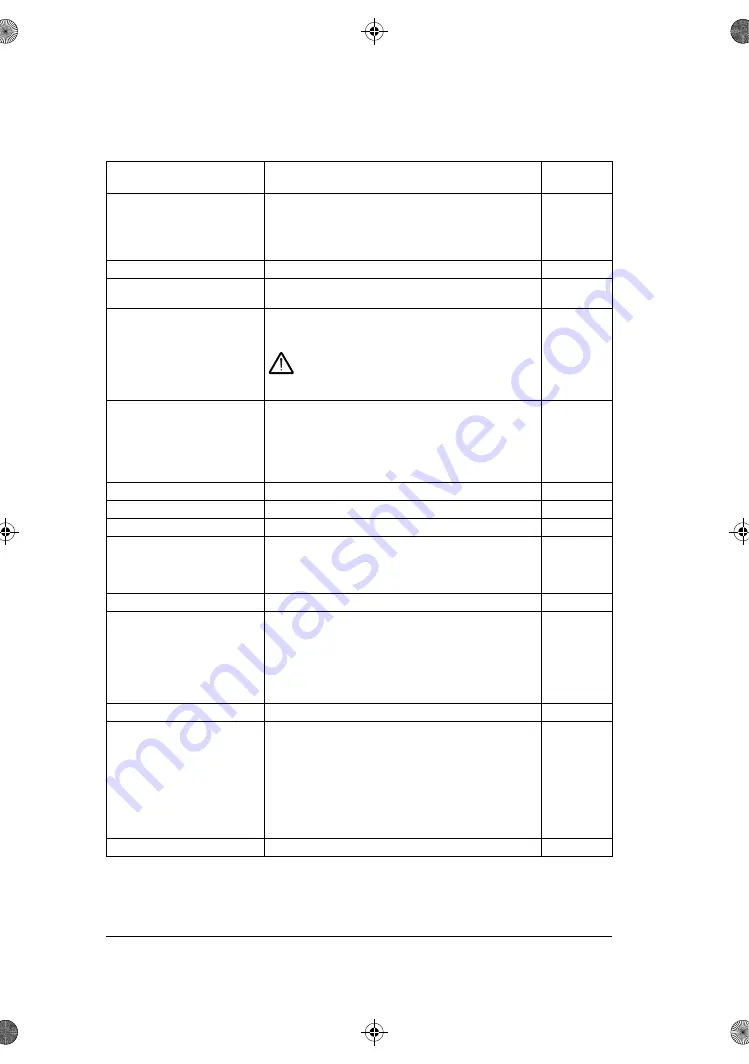
286 Parameters
Defines the level of flux braking power. (Other stopping
and braking modes can be configured in parameter group
).
Note:
This is an expert level parameter and should not be
adjusted without appropriate skill.
Disabled
Flux braking is disabled.
0
Moderate
Flux level is limited during the braking. Deceleration time
is longer compared to full braking.
1
Full
Maximum braking power. Almost all available current is
used to convert the mechanical braking energy to thermal
energy in the motor.
WARNING!
Using full flux braking heats up the
motor especially in cyclic operation. Make sure
that the motor can withstand this if you have a
cyclic application.
2
Defines the source of flux reference.
Notes:
• This is an expert level parameter and should not be
adjusted without appropriate skill.
• Do not use this parameter in scalar control mode, if the
parameter
is set to
Zero
0
User flux reference
.
1
-
Defines the flux reference when parameter
Note:
• ABB recommends the range of 20.00%...120.00%.
100.00%
0.00...200.00%
User-defined flux reference.
100 = 1%
This parameter can be used to improve the control
dynamics of a synchronous reluctance motor or a salient
permanent magnet synchronous motor.
As a rule of thumb, define a level to which the output
torque must rise with minimum delay. This will increase
the motor current and improve the torque response at low
speeds.
0.0%
0.0...1600.0%
Optimizer torque limit.
10 = 1%
Rotor time constant tuning.
This parameter can be used to improve torque accuracy in
closed-loop control of an induction motor. Normally, the
motor identification run provides sufficient torque
accuracy, but manual fine-tuning can be applied in
exceptionally demanding applications to achieve optimal
performance.
Note:
This is an expert level parameter and should not be
adjusted without appropriate skill.
100%
25…400%
Rotor time constant tuning.
1 = 1%
No.
Name/Value
Description
Default
FbEq 16
ACS180 FW.book Page 286 Tuesday, March 9, 2021 2:25 PM