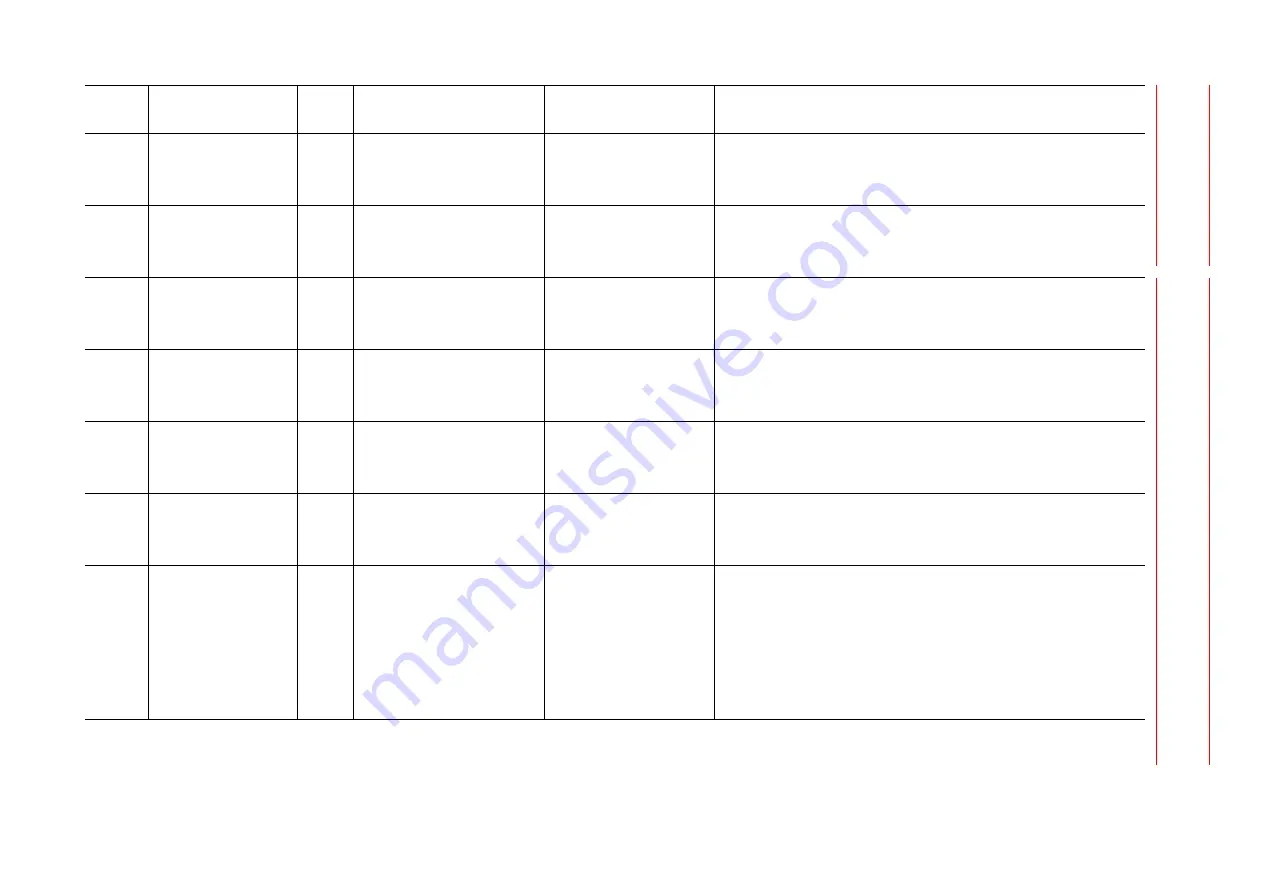
Alar
m List
Alar
m Nu
mbe
r (4
00
0 to
4
9
99
)
Alarm List-573
14
Path control position data
error of pre-reading bank
Software operation error
occurred
(1)Reset the alarm, and then try again.
(2)If the alarm occurs again, save the CMOS.BIN in maintenance
mode, and then contact your Yaskawa representative about
occurrence status (operating procedure).
16
Station/base axis motion
command error
Software operation error
occurred
(1)Reset the alarm, and then try again.
(2)If the alarm occurs again, save the CMOS.BIN in maintenance
mode, and then contact your Yaskawa representative about
occurrence status (operating procedure).
18
User coordinates number
error
Software operation error
occurred
(1)Reset the alarm, and then try again.
(2)If the alarm occurs again, save the CMOS.BIN in maintenance
mode, and then contact your Yaskawa representative about
occurrence status (operating procedure).
19
Processing error in re-
preparation of segment
control data
Software operation error
occurred
(1)Reset the alarm, and then try again.
(2)If the alarm occurs again, save the CMOS.BIN in maintenance
mode, and then contact your Yaskawa representative about
occurrence status (operating procedure).
20
Pre-reading task not
completed at master in twin
synchronous system
Software operation error
occurred
(1)Reset the alarm, and then try again.
(2)If the alarm occurs again, save the CMOS.BIN in maintenance
mode, and then contact your Yaskawa representative about
occurrence status (operating procedure).
23
Dynamic model arithmetic
error
Software operation error
occurred
(1)Reset the alarm, and then try again.
(2)If the alarm occurs again, save the CMOS.BIN in maintenance
mode, and then contact your Yaskawa representative about
occurrence status (operating procedure).
24
Speed limit control error
(excessive moment of gravity)
Setting error
(1)Check the following settings.
∙
The allowable breaking torque was exceeded only by the gravity
moment. Set the gravity value of the tool within payload of the
manipulator.
∙
Teach the manipulator orientation that does not become the overload
for each-axes of the manipulator.
(2)If the alarm occurs again, save the CMOS.BIN in maintenance
mode, and then contact your Yaskawa representative about
occurrence status (operating procedure).
Alarm
Number
Alarm Name
Sub
Code
Meaning
Cause
Remedy