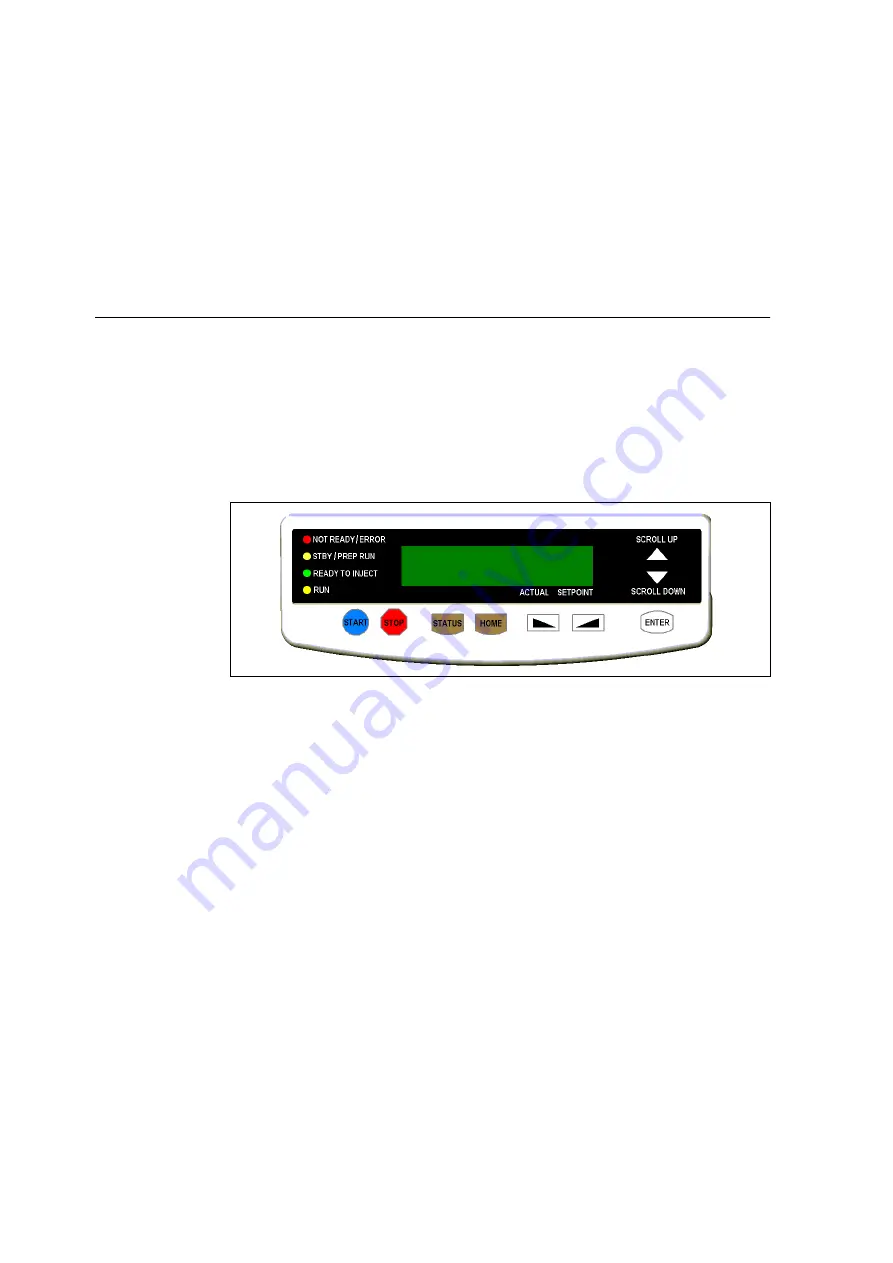
Chapter 2
The FOCUS GC User Interface
Overview
42
Overview
The user interface has three components:
•
two line display
•
display LEDs showing the instrument’s status
•
a keypad for data entry.
Figure 2-1 illustrates the complete FOCUS GC user interface.
Figure 2-1. The FOCUS GC User Interface
The Display
The display shows the menus you use to control the GC parameters, settings, and
configuration options. The data entry keys allow you to scroll through, set, and
modify the menu information.
Figure 2-2 shows the components of a typical menu display.
Summary of Contents for FOCUS GC
Page 4: ...iv InstructionManual ...
Page 70: ...Chapter 2 The FOCUS GC User Interface Info Diagnostics 70 Instruction Manual ...
Page 92: ...Chapter 4 Column Oven Oven Parameters 92 Instruction Manual ...
Page 124: ...Chapter 6 Purged Packed Column Injector PPKD PPKD Injector Menu 124 Instruction Manual ...
Page 170: ...Chapter 8 Flame Ionization Detector FID Detector Signal Parameters 170 Instruction Manual ...
Page 186: ...Chapter 9 Thermal Conductivity Detector TCD Detector Signal Parameters 186 Instruction Manual ...
Page 242: ...Chapter 13 SOP number P0473 04 E 02 May 2007 242 Instruction Manual ...
Page 336: ...Chapter 16 LAN Option Set up Set Up 336 Instruction Manual ...
Page 344: ...Glossary 344 Instruction Manual C min 1 instead of C min g L 1 instead of g L ...
Page 350: ...Index 350 Instruction Manual ...