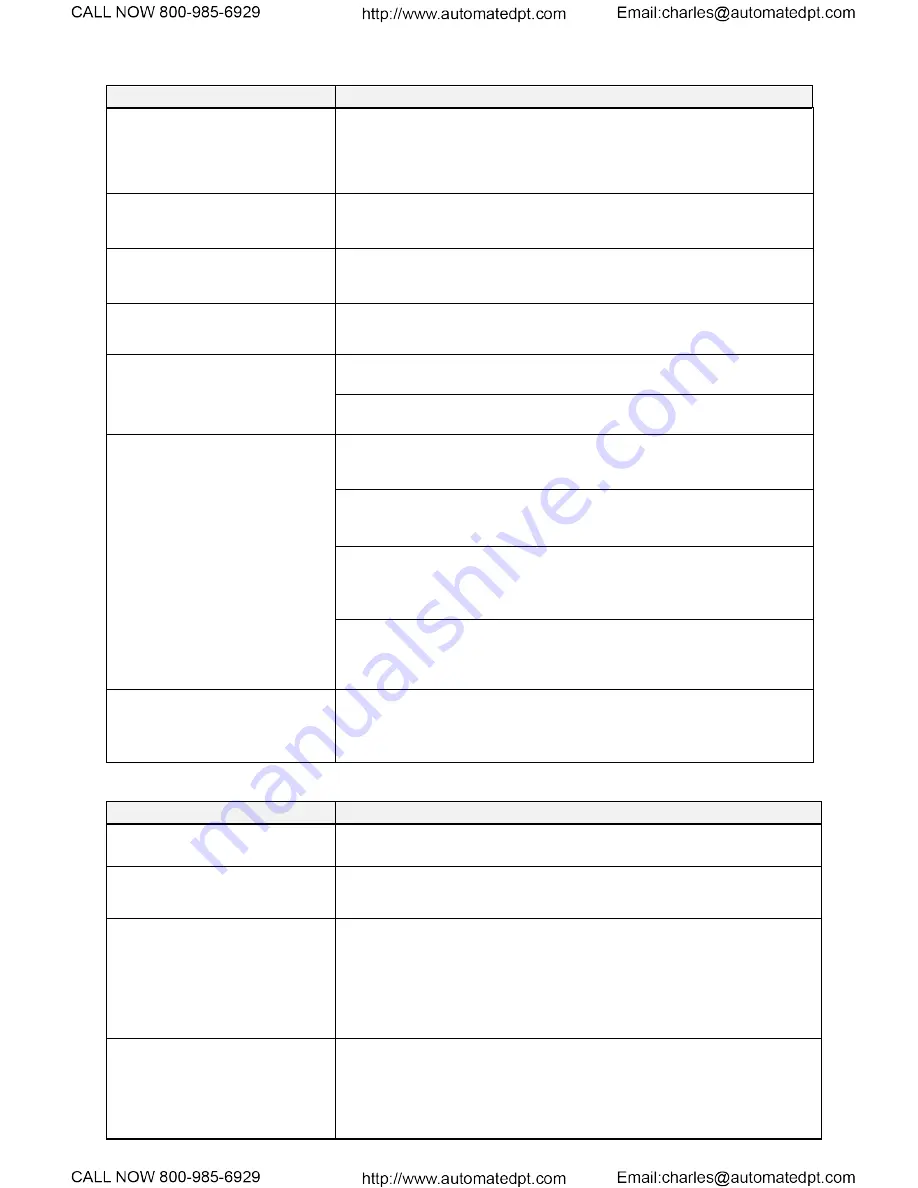
10-6
Possible Causes
What to Check and Suggested Measures
(8) A frequency command with
higher priority than the one
attempted was active.
Check the higher priority run command with Menu #2 "Data Checking" and
Menu #4 "I/O Checking" using the keypad, referring to the block diagram of
the frequency command block (refer to the EQ7 User's Manual, Chapter 6).
Correct any incorrect function code data (e.g. cancel the higher priority run
command).
(9) The upper and lower
frequencies for the frequency
limiters were set incorrectly.
Check the data of function codes F15 (Frequency limiter (High)) and F16
(Frequency limiter (Low)).
Change the settings of F15 and F16 to the correct ones.
(10) The coast-to-stop command
was effective.
Check the data of function codes E01 through E07, E98, and E99 and the
input signal status, using Menu #4 "I/O Checking" on the keypad.
Release the coast-to-stop command setting.
(11) Broken wires, incorrect
connection or poor contact with
the motor.
Check the wiring (Measure the output current).
Repair the wires to the motor, or replace them.
(12) Overload
Measure the output current.
Reduce the load (In winter, the load tends to increase.)
Check whether any mechanical brake is activated.
Release the mechanical brake, if any.
(13) Torque generated by the motor
was insufficient.
Check that the motor starts running if the value of torque boost (F09*) is
increased.
Increase the value of torque boost (F09*) and try to run the motor.
Check the data of function codes F04*, F05*, H50, H51, H52, H53, H65, and
H66.
Change the V/f pattern to match the motor's characteristics.
Check that the motor switching signal (selecting motor 1, 2, 3 or 4) is correct
and the data of function codes matches each motor.
Correct the motor switching signal.
Modify the function code data to match the connected motor.
Check whether the reference frequency is below the slip-compensated
frequency of the motor.
Change the reference frequency so that it becomes higher than the
slip-compensated frequency of the motor.
(14) Wrong connection or poor
contact of DC reactor (DCR)
Check the wiring.
Inverters of 100 HP or above require a DCR to be connected. Without a DCR,
these inverters cannot run.
Connect the DCR correctly. Repair or replace DCR wires.
[ 2 ] The motor rotates, but the speed does not increase.
Possible Causes
What to Check and Suggested Measures
(1) The maximum frequency
currently specified was too low.
Check the data of function code F03* (Maximum frequency).
Correct the F03* data.
(2) The data of frequency limiter
(High) currently specified was
too low.
Check the data of function code F15 (Frequency limiter (High)).
Correct the F15 data.
(3) The reference frequency
currently specified was too low.
Check that the reference frequency has been entered correctly, using Menu #4
"I/O Checking" on the keypad.
Increase the reference frequency.
Inspect the external frequency command potentiometers, signal converters,
switches, and relay contacts. Replace any ones that are faulty.
Connect the external circuit wires to terminals [13], [12], [11], [C1], and [V2]
correctly.
(4) A frequency command (e.g.,
multi-frequency or via
communications) with higher
priority than the one attempted
was active and its reference
frequency was too low.
Check the data of the relevant function codes and what frequency commands
are being received, through Menu #1 "Data Setting," Menu #2 "Data Checking"
and Menu #4 "I/O Checking," on the keypad by referring to the block diagram of
the frequency command (refer to the EQ7 User's Manual, Chapter 6).
Correct any incorrect data of function codes (e.g. cancel the higher priority
frequency command).