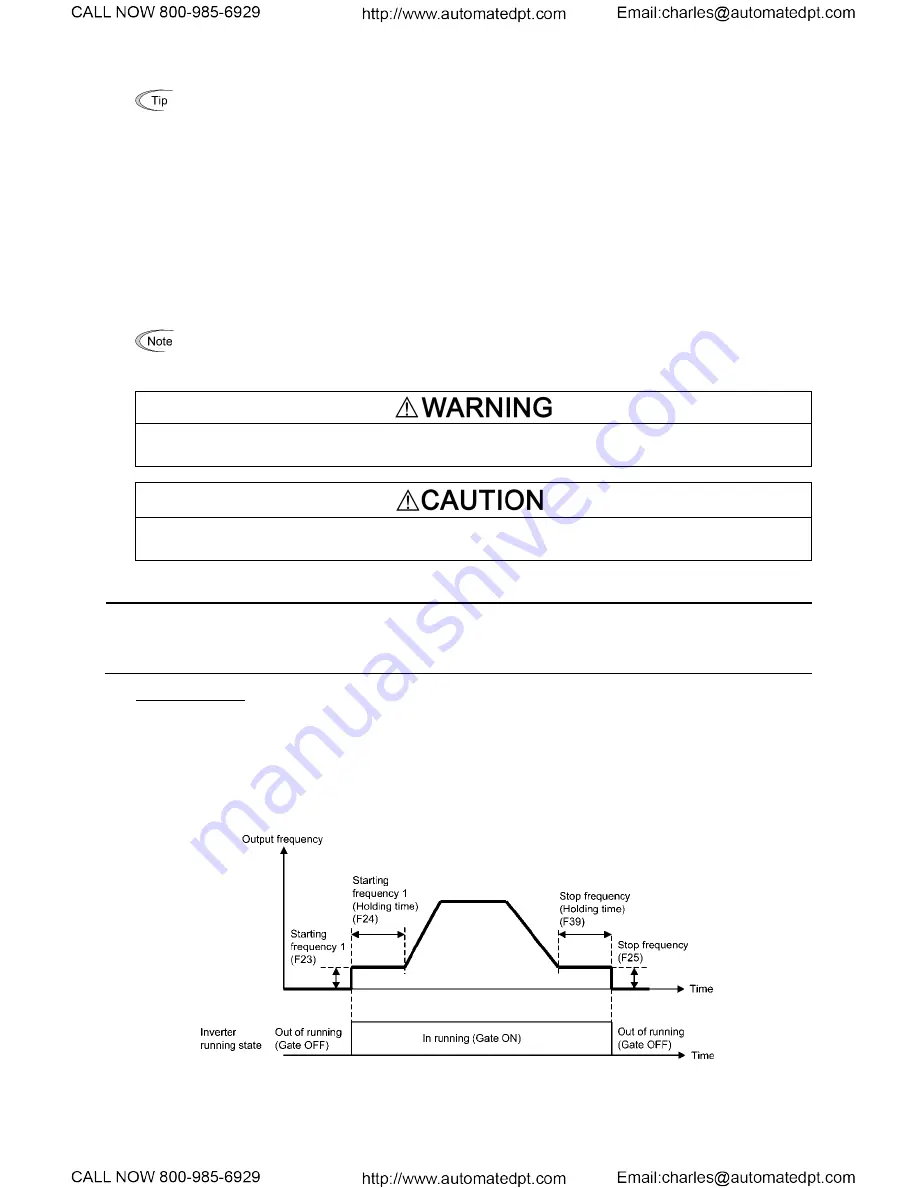
4-51
It is also possible to use an external digital input signal as an "Enable DC braking" terminal command
DCBRK
. As long as the
DCBRK
command is ON, the inverter performs DC braking, regardless of the
braking time specified by F22.
(
Refer to E01 through E07, data =13.)
Turning the
DCBRK
command ON even when the inverter is in a stopped state activates the DC braking.
This feature allows the motor to be excited before starting, resulting in smoother acceleration (quicker
build-up of acceleration torque) (under V/f control).
When vector control without/with speed sensor is selected, use the pre-exciting feature for establishing
the magnetic flux. (
For details, refer to H84.)
In general, DC braking is used to prevent the motor rotation by inertia during the stopping process. Under
vector control with speed sensor, however, zero speed control will be more effective for applications
where load is applied to the motor even in a stopped state.
If the zero speed control continues for a long time, the motor may slightly rotate due to a control error. To
eliminate any rotation, use the servo-lock function. (
For details, refer to J97.)
In general, specify data of function code F20 at a value close to the rated slip frequency of motor. If
setting is at an extremely high value, control may become unstable and an overvoltage alarm may result
in some cases.
Even if the motor is stopped by DC braking, voltage is output to inverter output terminals U, V, and W.
An electric shock may occur.
The DC brake function of the inverter does not provide any holding mechanism.
Injuries could occur.
F23 to F25 Starting Frequency 1, Starting Frequency 1 (Holding time), Stop Frequency
F38 (Stop Frequency (Detection mode)) F39 (Stop Frequency (Holding time))
H92 (Continuity of Running (P)
H93 (Continuity of Running (I)
d24 (Zero Speed Control)
Under V/f control
At the startup of an inverter, the initial output frequency is equal to the starting frequency. The inverter shuts off its
output when the output frequency reaches the stop frequency.
Set the starting frequency to a level at which the motor can generate enough torque for startup. Generally, set the
motor's rated slip frequency as the starting frequency.
Specifying the holding time for the starting frequency compensates for the delay time for the establishment of a
magnetic flux in the motor; specifying that for the stop frequency stabilizes the motor speed at the stop of the
inverter.
Starting frequency 1 (F23
)
Data setting range: 0.0 to 60.0 (Hz)
F23 specifies the starting frequency at the startup of an inverter. Under V/f control, even if the starting frequency is
set at 0.0 Hz, the inverter starts at 0.1 Hz.