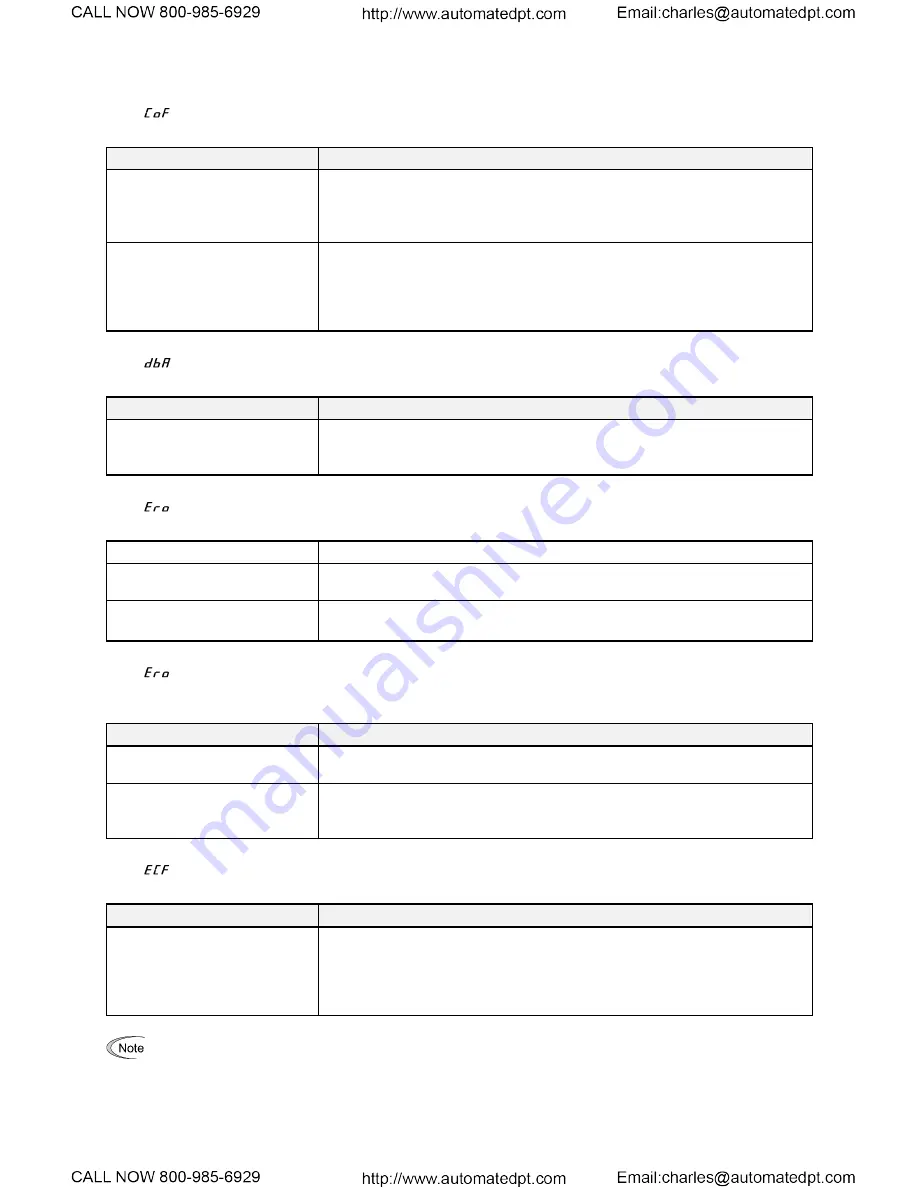
10-24
[ 31 ]
PID feedback wire break
Problem The PID feedback wire is broken.
Possible Causes
What to Check and Suggested Measures
(1) The PID feedback signal
wire is broken.
Check whether the PID feedback signal wires are connected correctly.
Check whether the PID feedback signal wires are connected correctly. Or,
tighten up the related terminal screws.
Check whether any contact part bites the wire sheath.
(2) PID feedback related circuit
affected by strong electrical
noise.
Check if appropriate noise control measures have been implemented (e.g.,
correct grounding and routing of signal wires, communication cables, and main
circuit wires).
Implement noise control measures.
Separate the signal wires from the main power wires as far as possible.
[ 32 ]
Braking transistor error
Problem A braking transistor error is detected.
Possible Causes
What to Check and Suggested Measures
(1) The braking transistor is
broken.
Check whether resistance of the braking resistor is correct or there is a
misconnection of the resistor.
Consult your TECO-Westinghouse Motor Company representative for repair.
[ 33 ]
Positioning control error (Servo-lock)
Problem An excessive positioning deviation has occurred when the servo-lock function was activated.
Possible Causes
What to Check and Suggested Measures
(1) Insufficient gain in
positioning control system.
Readjust the settings of J97 (Servo-lock (Gain)) and d03 (Speed control 1 P
(Gain)).
(2) Incorrect control completion
width.
Check whether the setting of J99 (Servo-lock (Completion width)) is correct.
Correct the setting of J99.
[ 34 ]
Positioning control error (Synchronous control)
Problem An excessive positioning deviation has occurred when the synchronous control function was activated.
For details, refer to the instruction manual of the PG interface card.
Possible Causes
What to Check and Suggested Measures
(1) Insufficient gain in
positioning control system.
Readjust the settings of d72 (Synchronous Control Parameters (APR P gain))
and d03 (Speed control 1 P (Gain)).
(2) Incorrect control completion
width.
Check whether the setting of d78 (Synchronous Control Parameters
(Over-deviation detection width)) is correct.
Correct the setting of d78.
[ 35 ]
Enable circuit failure
Problem The circuit that detects the status of the enable circuit is broken.
Possible Causes
What to Check and Suggested Measures
(1) Circuit related to the Enable
circuit affected by strong
electrical noise.
Check if appropriate noise control measures have been implemented (e.g.,
correct grounding and routing of signal wires, communication cables, and main
circuit wires).
Implement noise control measures.
Separate the signal wires from the main power wires as far as possible.
The "Reset alarm" terminal command
RST
cannot reset this alarm
ecf
. If even a power-off reset cannot restore
the inverter state, the inverter needs to be repaired.