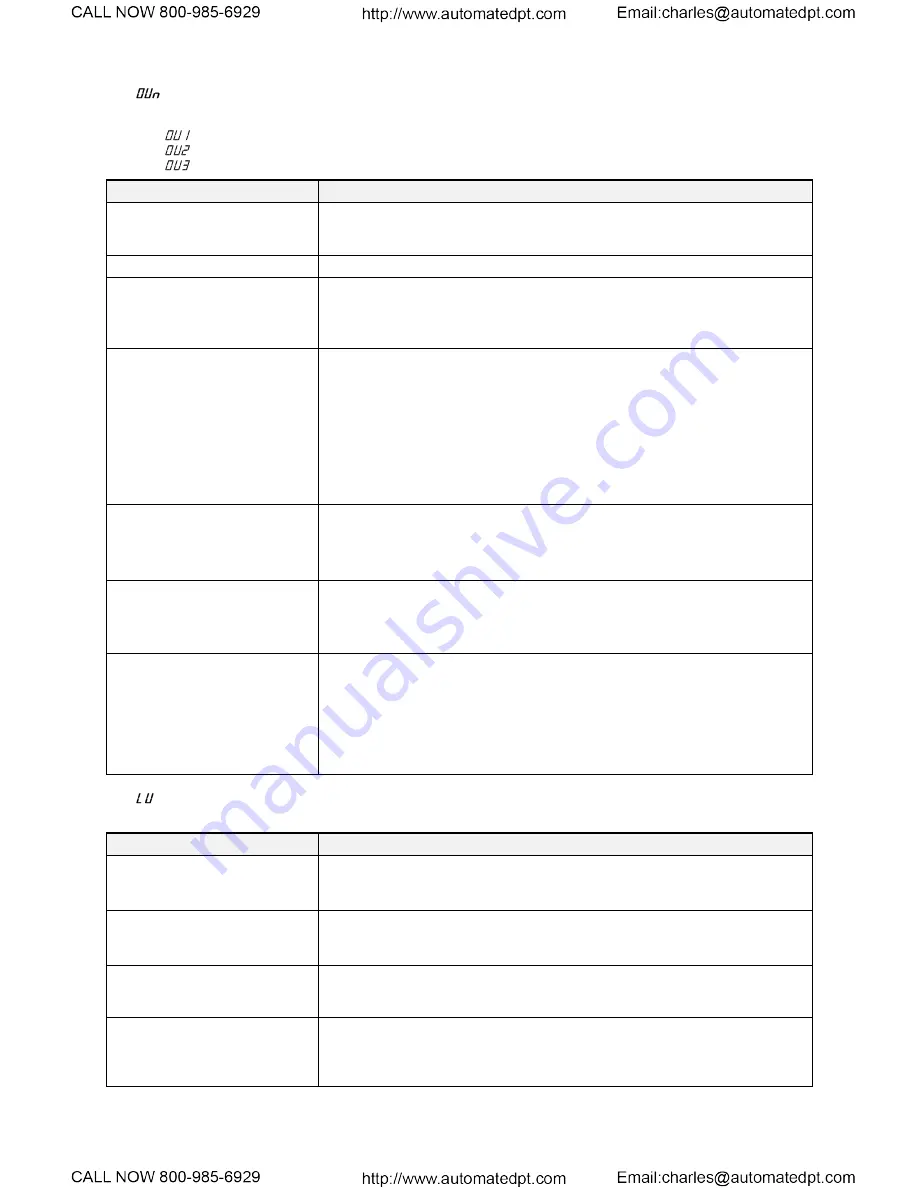
10-13
[ 3 ]
Overvoltage
Problem The DC link bus voltage was over the detection level of overvoltage.
Overvoltage occurred during acceleration.
Overvoltage occurred during deceleration.
Overvoltage occurred during running at constant speed.
Possible Causes
What to Check and Suggested Measures
(1) The power supply voltage
exceeded the inverter's
specification range.
Measure the input voltage.
Decrease the voltage to within the specified range.
Possible Causes
What to Check and Suggested Measures
(2) A surge current entered the
input power supply.
In the same power line, if a phase-advancing capacitor is turned ON/OFF or a
thyristor converter is activated, a surge (momentary large increase in the voltage
or current) may be caused in the input power.
Install a DC reactor.
(3) The deceleration time was
too short for the moment of
inertia for load.
Recalculate the deceleration torque based on the moment of inertia for the load
and the deceleration time.
Increase the deceleration time (F08, E11, E13, E15, and H56).
Enable the automatic deceleration (anti-regenerative control) (H69), or
deceleration characteristics (H71).
Enable torque limiter (F40, F41, E16, E17, and H73).
Set the rated voltage (at base frequency) (F05*) to "0" to improve the braking
capability.
Consider the use of a braking resistor.
(4) The acceleration time was
too short.
Check if the overvoltage alarm occurs after rapid acceleration.
Increase the acceleration time (F07, E10, E12, and E14).
Select the S-curve pattern (H07).
Consider the use of a braking resistor.
(5) Braking load was too heavy.
Compare the braking torque of the load with that of the inverter.
Set the rated voltage (at base frequency) (F05*) to "0" to improve the braking
capability.
Consider the use of a braking resistor.
(6) Malfunction caused by
noise.
Check if the DC link bus voltage was below the protective level when the
overvoltage alarm occurred.
Implement noise control measures. For details, refer to the EQ7 User's
Manual, "Appendix A."
Enable the auto-reset (H04).
Connect a surge absorber to magnetic contactor's coils or other solenoids (if
any) causing noise.
[ 4 ]
Undervoltage
Problem DC link bus voltage has dropped below the undervoltage detection level.
Possible Causes
What to Check and Suggested Measures
(1) A momentary power failure
occurred.
Release the alarm.
If you want to restart running the motor without treating this condition as an
alarm, set F14 to "3," "4," or "5," depending on the load type.
(2) The power to the inverter
was switched back to ON
too soon (when F14 = 1).
Check if the power to the inverter was switched back to ON while the control
power was still alive. (Check whether the LEDs on the keypad light.)
Turn the power ON again after all LEDs on the keypad go off.
(3) The power supply voltage
did not reach the inverter's
specification range.
Measure the input voltage.
Increase the voltage to within the specified range.
(4) Peripheral equipment for the
power circuit malfunctioned,
or the connection was
incorrect.
Measure the input voltage to find which peripheral equipment malfunctioned or
which connection is incorrect.
Replace any faulty peripheral equipment, or correct any incorrect
connections.