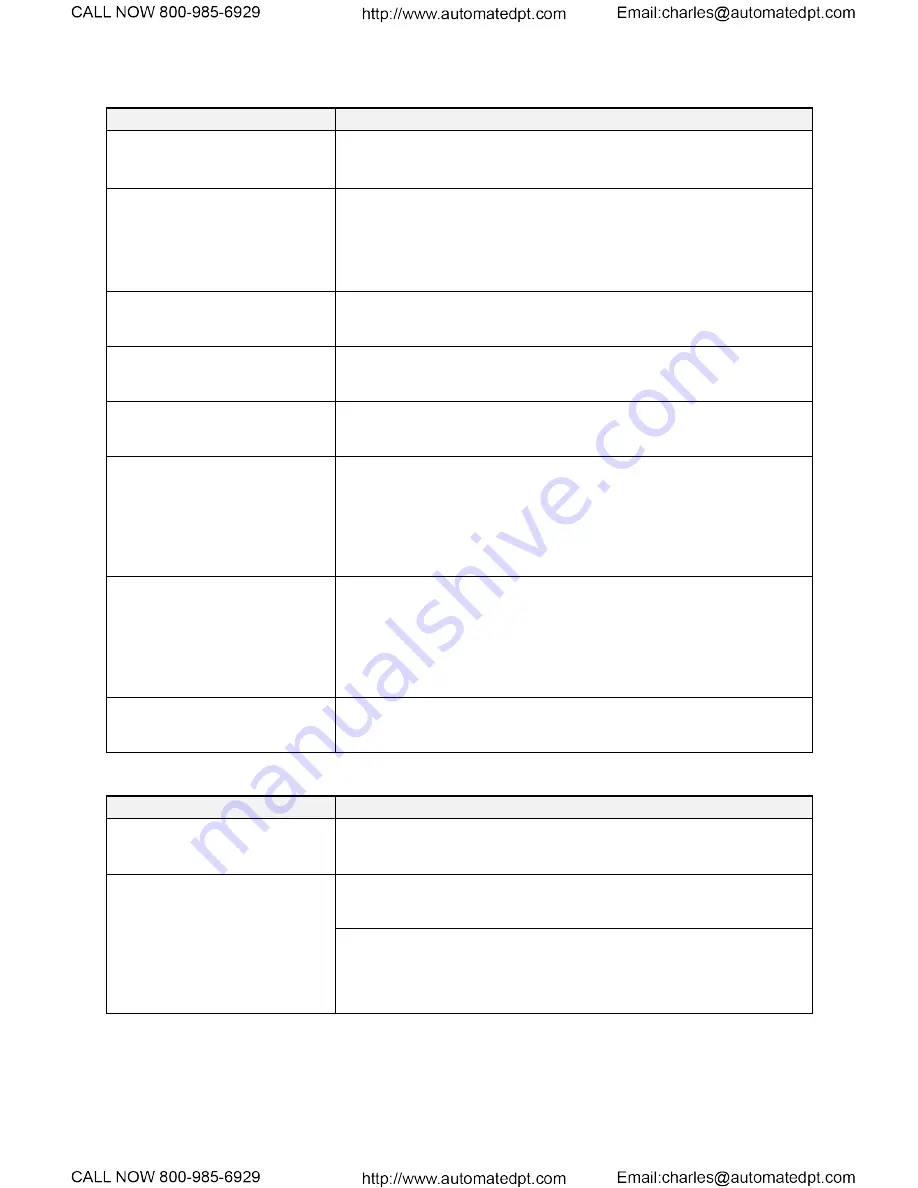
10-9
[ 6 ] The motor does not accelerate or decelerate within the specified time.
Possible Causes
What to Check and Suggested Measures
(1) The inverter runs the motor
with S-curve or curvilinear
pattern.
Check the data of function code H07 (Acceleration/deceleration pattern).
Select the linear pattern (H07 = 0).
Shorten the acceleration/deceleration time (F07, F08, E10 through E15).
(2) The current limiting operation
prevented the output frequency
from increasing (during
acceleration).
Make sure that F43 (Current limiter (Mode selection)) is set to "2: Enable
during acceleration and at constant speed," then check that the setting of F44
(Current limiter (Level)) is reasonable.
Readjust the setting of F44 to appropriate value, or disable the function of
current limiter with F43.
Increase the acceleration/deceleration time (F07, F08, E10 through E15).
(3) The automatic deceleration
(Anti-regenerative control) is
enabled during deceleration.
Check the data of function code H69 (Automatic deceleration (Mode
selection)).
Increase the deceleration time (F08, E11, E13, and E15).
(4) Overload.
Measure the output current.
Reduce the load (For fans or pumps, decrease the frequency limiter value
(F15).) (In winter, the load tends to increase.)
(5) Torque generated by the motor
was insufficient.
Check that the motor starts running if the value of the torque boost (F09*) is
increased.
Increase the value of the torque boost (F09*).
(6) An external potentiometer is
used for frequency setting.
Check that there is no noise in the control signal wires from external sources.
Isolate the control signal wires from the main circuit wires as far as
possible.
Use shielded or twisted wires for control signals.
Connect a capacitor to the output terminal of the external frequency
command potentiometer or set a ferrite core on the signal wire. (Refer to
Chapter 2.)
(7) The output frequency is limited
by the torque limiter.
Check whether data of torque limiter related function codes (F40, F41, E16
and E17) is correctly configured and the
TL2
/
TL1
terminal command ("Select
torque limiter level 2/1") is correct.
Correct the data of F40, F41, E16 and E17 or reset them to the factory
defaults.
Set the
TL2
/
TL1
correctly.
Increase the acceleration/deceleration time (F07, F08, E10 through E15).
(8) The specified acceleration or
deceleration time was
incorrect.
Check the terminal commands
RT1
and
RT2
for acceleration/deceleration
times.
Correct the
RT1
and
RT2
settings.
[ 7 ] The motor does not restart even after the power recovers from a momentary power failure.
Possible Causes
What to Check and Suggested Measures
(1) The data of function code F14
is either "0," "1," or "2."
Check if an undervoltage trip (
lu)
occurs.
Change the data of function code F14 (Restart mode after momentary
power failure (Mode selection)) to "3," "4," or "5."
(2) The run command remains
OFF even after the power has
been restored.
Check the input signal with Menu #4 "I/O Checking" using the keypad.
Check the power recovery sequence with an external circuit. If necessary,
consider the use of a relay that can keep the run command ON.
In 3-wire operation, the power to the control printed circuit board (control PCB)
has been shut down once because of a long momentary power failure time, or
the "Enable 3-wire operation" signal
HOLD
has been turned OFF once.
Change the design or the setting so that a run command can be issued
again within 2 seconds after the power has been restored.